The success story of the Würth Group began on a very small scale back in 1945. In the early days, the goods offered by screw wholesaler Adolf Würth were still brought to Künzelsau train station by cart before being transported to the company’s customers from there. In the space of 75 years, the two-man business has evolved into a global trading group with 79,139 employees, over 33,000 of whom work as members of the sales force. Thanks to its worldwide presence, the company now reaches customers across the globe.
In its core business, the sale of assembly and fastening materials, the Würth Group is a firmly established market player. Other trading and production companies, known as the Allied Companies, operate in related business areas, ranging from the electrical wholesale and electronics to financial services. The Würth Group comprises more than 400 companies represented by around 2,300 branches in more than 80 countries. The Group generated sales of EUR 14.4 billion in the 2020 fiscal year.
In its anniversary year of 2020, Adolf Würth GmbH & Co. KG, the nucleus of the company, looked back on its 75-year success story. At the same time, Reinhold Würth, who took over the business at the age of 19 following his father’s death, also celebrated his 85th birthday. The family business serves as a role model in terms of its social and cultural commitment.
Today, the Würth Collection comprises more than 18,300 works of art that can be seen in five museums and ten associated galleries of the Würth Group across Europe. As recently as June 2020, Museum Würth 2 opened its doors to the public as an extension of Carmen Würth Forum at the company’s Gaisbach location. The museum showcases centerpieces of modern and contemporary art from the Würth Collection. Reinhold Würth is convinced that the juxtaposition of art and day-to-day working life provides inspiration for new ideas. All of the company’s museums are open to the public with free admission.
Over its 75-year history, the company has repeatedly pursued new avenues and, as a family business, its actions are geared towards ensuring sustainable and long-term growth. At the same time, the Würth Group is particularly aware of its social responsibility and, alongside its commitment to art and culture, is involved in a large number of initiatives in areas such as sports, social affairs, and education.
A wide array of activities has also been launched to promote environmental sustainability, most of them still at the level of individual companies. The Central Managing Board has decided to bundle these activities within the Würth Group and, in this context, to lay the foundation for Group-wide reporting, including quantitative targets. A sustainability report is planned to provide information on these efforts at the Group level in 2022.
But even when venturing down new avenues, the company always remains loyal to its philosophy and values: Openness, gratitude, respect, curiosity, responsibility, and humility are the cornerstones of our success and form the basis for our cooperation with each other, with our business partners and with our customers. This is the strategy that has accompanied us for 75 years and will continue to accompany us going forward. Corporate culture at Würth? Like!
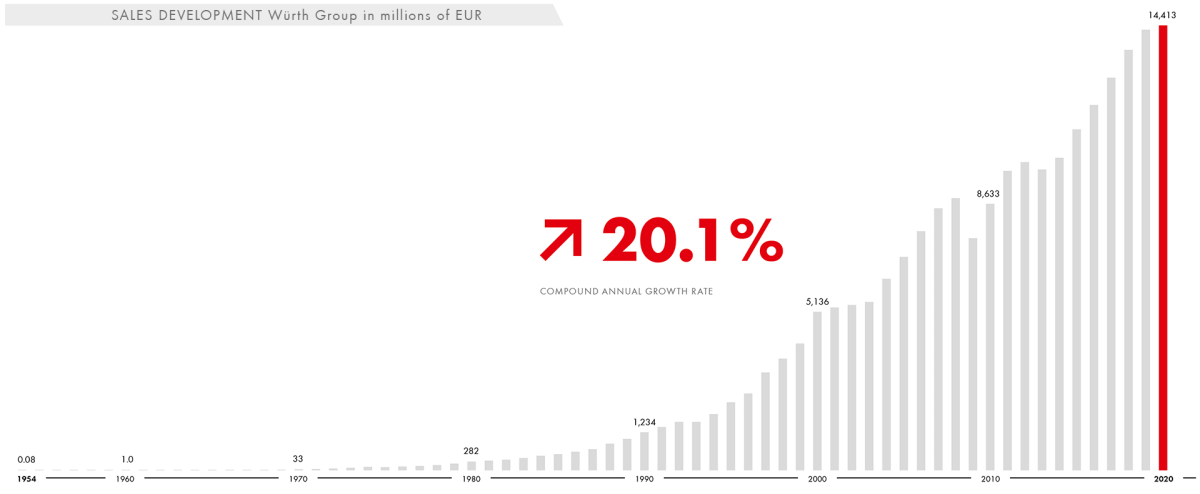
The COVID-19 crisis plunged the German economy into the second most severe recession witnessed in the post-war era. Over and above the battle against the pandemic, events were dominated by ongoing tension in the South China Sea and the Middle East, a growing wave of populism and protectionism associated with Brexit, and the unpredictable nature of Donald Trump’s US presidency. The escalating trade dispute between the US and China and the ongoing quarrels over the future of the EU were also major factors in 2020.
These risk factors were not new and had been taken into account worldwide. The situation with the hitherto unknown SARS-CoV-2 virus was a different matter entirely: It triggered the biggest economic slump seen in modern times. It was not possible to correct the marked downward trajectory before the end of the year. According to the World Bank, global economic output fell by 4.3 percent in 2020, compared with 2.8 percent growth one year earlier. With only a slight increase in gross domestic product in China (+ 2.0 percent) and a contraction in the US (–4.6 percent), the world’s two largest economies lost considerable steam.
- COVID-19 pandemic sends shockwaves through German economy after ten-year growth phase
- Economic slump in almost all sectors of economy—service sector and parts of industry hit particularly hard
- Construction only exception with 2.8 percent increase in gross value added
Economic output in Germany, the Würth Group’s largest single market, plunged by 5.0 percent last year (2019: + 0.6 percent). The only time the economy showed a more dramatic contraction was during the global financial crisis in 2009, when gross domestic product (GDP) plummeted by 5.7 percent. Employment also declined overall: The unemployment rate averaged 5.9 percent in 2020 (2019: 5.0 percent).
Compared with the eurozone, Germany has nevertheless fared relatively well during the crisis. The construction industry in particular, a sector of the economy that is especially important for Würth, made a significant contribution to the trend. While macroeconomic gross output (excluding construction) declined in 2020, it increased by 2.8 percent in the construction sector (2019: + 4.0 percent). In the mainstream construction sector, sales rose by 5.9 percent in nominal terms (2019: 6.7 percent). In addition, the corporate sector created roughly another 22,500 new jobs in 2020 (2019: + 33,385). Last year, incoming orders rose by 0.5 percent in nominal terms (2019: + 8.2 percent), but fell slightly by 2.6 percent in real terms (2019: + 3.0 percent). This can be explained by various COVID-19-related restrictions, such as isolated construction site shutdowns, the partial unavailability of foreign skilled workers due to border closures, or missing material deliveries and canceled orders.
It was a similar story in the trades, another decisive key market for the Würth Group: Here, sales were 1.4 percent higher in 2020 than they had been in 2019 (+ 3.9 percent). Despite the positive figures, the industry recorded the weakest sales growth witnessed in the last seven years. Numerous companies are still struggling due to the shortage of skilled workers. A large number of vocational traineeship positions remained unfilled. What is more, craft businesses have a number of bureaucratic hurdles to overcome, which also has the effect of inhibiting growth.
Since 2018, companies in the metal and electrical industry (M+E) have been grappling with a recession and an urgent need for structural change, including digital transformation. This was compounded by the effects of the COVID-19 pandemic last year. After 2019 saw a decline of 4.5 percent, 2020 was the second year of severe recession for the M+E industry, another key pillar for the Würth Group. Looking at 2020 on average, M+E production was down by 14.1 percent on the previous year. The job creation witnessed in recent years came to an end in mid-2019. The export-oriented mechanical engineering sector also recorded a 14.0 percent slump in production in 2020 (2019: – 2.0 percent). One reason for this was the sharp decline in production in the automotive industry due to the crisis. Last year, the number of vehicles sold by car manufacturers was down by almost one-fifth on the year before. A total of 2.9 million new cars were registered in 2020, 19.1 percent less than in 2019 (2019: – 5.0 percent). This development was replicated across the globe: Sales bans, economic uncertainty, and production downtimes translated into negative results in Europe, as well as in Asia, Russia, and the United States.
The picture for the eurozone as a whole is even bleaker: The European Commission estimates that GDP contracted by 6.8 percent in 2020 (2019: + 1.3 percent). Economic output in other major EU countries, France, Italy, Spain and Great Britain, for example, fell by between 8.3 percent and 11.0 percent. Unemployment in the EU also soared in a year dominated by COVID-19. Almost two million more people found themselves out of work. As a result, the unemployment rate rose from 6.5 percent in December 2019 to 7.5 percent at the end of 2020, according to Eurostat.
France was forced to impose another hard lockdown starting in November 2020 to control the COVID-19 outbreak. Thus, the European Commission expects GDP to have declined by 8.3 percent. GDP was still growing at a rate of 1.5 percent in 2019. The unemployment rate has increased in France: from 8.5 percent in 2019 to 8.9 percent in 2020.
Italy was able to contain the spread of infection in the fourth quarter by taking distinct measures for each region. This allowed it to prevent the sort of full nationwide lockdown seen in the spring. For 2020 as a whole, experts at the European Commission predict an 8.8 percent drop in GDP (2019: + 0.3 percent). In 2019, the unemployment rate was 9.9 percent, while it rose to 11.0 percent during the COVID-19 crisis.
Spain, much like Italy, responded to the renewed rise in infections in the fall by implementing a range of different measures according to region. Nevertheless, economists predict that growth in Spain will have slumped by 11.0 percent (2019: + 2.0 percent), which is also reflected in a very high unemployment rate of 16.8 percent (2019: 14.1 percent).
The COVID-19 pandemic and partial economic standstill maneuvered Great Britain into an economic crisis of historic proportions in 2020. A healthcare system on its last legs after years of funding cuts, an extremely high population density, and political failures on a massive scale allowed the virus to spread widely unchecked. For the year as a whole, Great Britain recorded a 9.9 percent drop in economic output (2019: + 1.5 percent). The unemployment rate also increased by 1.6 percentage points to 5.4 percent (2019: 3.8 percent).
China is the only major economy that did not contract in 2020. With GDP growth of 2.0 percent (2019: + 6.1 percent), the People’s Republic can report higher growth than any other country, but also hefty losses as a result of COVID-19.
Tough measures to contain the pandemic also slammed the brakes on India’s economy. GDP slumped by 9.6 percent in 2020 (2019: + 4.2 percent).
In the US, GDP contracted by 4.6 percent (2019: + 2.2 percent). While the government was late in its response to the pandemic, it went on to launch a generous rescue package.
Last year, Latin America’s economy experienced the biggest economic slump in decades. Gross domestic product fell by an average of 7.6 percent in 2020 (2019: + 0.1 percent).
Last year was also dominated by a barrage of bad news for the Russian economy. Production closures due to the lockdown to combat the COVID-19 pandemic, the slump in oil prices, and the depreciation of the ruble sent GDP sliding by 4.0 percent (2019: + 1.3 percent).
- Sales up slightly to EUR 14.4 billion
- Operating result slightly above previous year’s level
- Digitalization drive ensures above-average growth in e-commerce business
In 2020, the Würth Group generated sales of EUR 14.4 billion, up slightly on the previous year (2019: EUR 14.3 billion). This represents growth of 1.0 percent. After adjustments to reflect exchange rate effects, the rate of growth came out at 2.0 percent.
The recurring theme of 2020 was the COVID-19 pandemic with its huge global impact. The economic development of the Würth Group was also heavily influenced by the pandemic. While sales slumped by more than 20 percent in April 2020, with the decline making it into the double digits again in May 2020, growth improved month over month thereafter, resulting in double-digit sales growth in December, which allowed the Group to close the fourth quarter of 2020 with the strongest growth.
The Group maintained its performance at a high level thanks to its multi-channel strategy, the diversification of risk resulting from its international positioning and also diversification across various business areas. The 2020 sales trend also reflects the varying impact that the pandemic had on individual sectors and markets: While the Construction division (+12.2 percent) and Electrical Wholesale Germany (+10.8 percent) performed very well, reporting double-digit sales growth, sales in areas that are direct suppliers to the automotive and mechanical engineering industries declined.
Germany proved to be very robust during the COVID-19 pandemic. The Würth Group achieved 2.9 percent growth in this market, with Adolf Würth GmbH & Co. KG, the nucleus of the Group, growing by 7.4 percent. Outside of Germany, the Group saw its sales drop by 0.4 percent.
E-business sales showed above-average growth of 5.8 percent, climbing to EUR 2.8 billion in 2020. This brought their share of Group sales up by one percentage point to 19.3 percent. Due to contact restrictions and lockdowns, business shifted increasingly to digital sales channels. Be it via the online shop, the Würth App, or e-procurement solutions: Thanks to the systematic pursuit of its digitalization strategy and its financial stability, Würth remained a reliable partner and supplier to its customers even during the pandemic. E-business has become even more important as part of the multi-channel strategy.
At EUR 775 million, the operating result was up slightly year on year (2019: EUR 770 million). This is a very good result considering the global pandemic and was achieved thanks to stringent cost discipline and relatively stable gross profit margins. The rate of return remained constant year on year at 5.4 percent (2019: 5.4 percent). In order to implement its planned strategies, the Würth Group is making sustainable investments in its various business areas and markets. Capital expenditure on intangible assets and property, plant and equipment came to EUR 473 million in 2020.
Despite the COVID-19 crisis, the Würth Group did not implement any structural job cuts. On the contrary: In 2020, the number of employees increased by 453 from 78,686 to a new high of 79,139. The number of employees in Germany is now 24,514, representing an increase of 0.7 percent. As in the past, the majority of the employees are still based in Germany. Würth is a sales company at its core. Including sales-related areas, almost 50,000 employees have direct contact with customers, with 33,176 of them working as sales representatives.
- COVID-19 pandemic hampers Würth Group growth worldwide
- Germany remains biggest individual market
- Spain benefits from company acquisition
Germany is the most important individual market for the Würth Group, accounting for 42.1 percent of sales. Although the growth momentum in 2020 varied considerably from business unit to business unit, a satisfactory result was achieved overall with 2.9 percent growth in Germany. Outside of Germany, the companies recorded a 0.4 percent drop in sales, almost all of which was attributable to the COVID-19 pandemic and the associated restrictions and which affected virtually all continents and regions.
Decentralization has always been one of the Würth Group’s strengths. In 2020, geographical diversification was particularly helpful to us, as the more than 400 companies in over 80 countries were affected by the pandemic to very different degrees. The lockdowns imposed varied in their timing, intensity, and length, and the classification of the systemic importance of our business units also differed from region to region. We were hit by temporary restrictions on customer visits by sales representatives, pick-up shop closures, and even by the closure of national companies in some cases.
The multi-channel strategy we have been pursuing for years now proved all the more successful. In addition to telephone sales, the focus on e-business was a key component of our sales activities as we sought to maintain proximity to our customers and ensure that they were supplied with materials.
In the 2020 fiscal year, sales of EUR 6,073 million were generated in Germany, up by 2.9 percent (2019: EUR 5,900 million). Against the backdrop of the COVID-19 pandemic, this is a very positive development. The German companies benefited from buoyant construction activity in both the private and public sectors, as well as from their stable business models, allowing them to respond very quickly to the challenges associated with the onset of the COVID-19 crisis in Germany from March and April 2020. The companies in the German Electrical Wholesale unit showed particularly encouraging development, led by Fega & Schmitt Elektrogroßhandel GmbH, which reported a double-digit increase in sales, although companies in the chemicals sector also reported encouraging development. Companies that are direct suppliers to the automotive and mechanical engineering sectors and had already been affected by the downward trend in these sectors were hit hard by the COVID-19 pandemic. By way of example, this translated into lower sales at the subsidiary Arnold Umformtechnik, which specializes in connection technology for the automotive manufacturing industry. Our major German tool distributors Hahn+Kolb, Sartorius, and Hommel Hercules also reported declining sales.
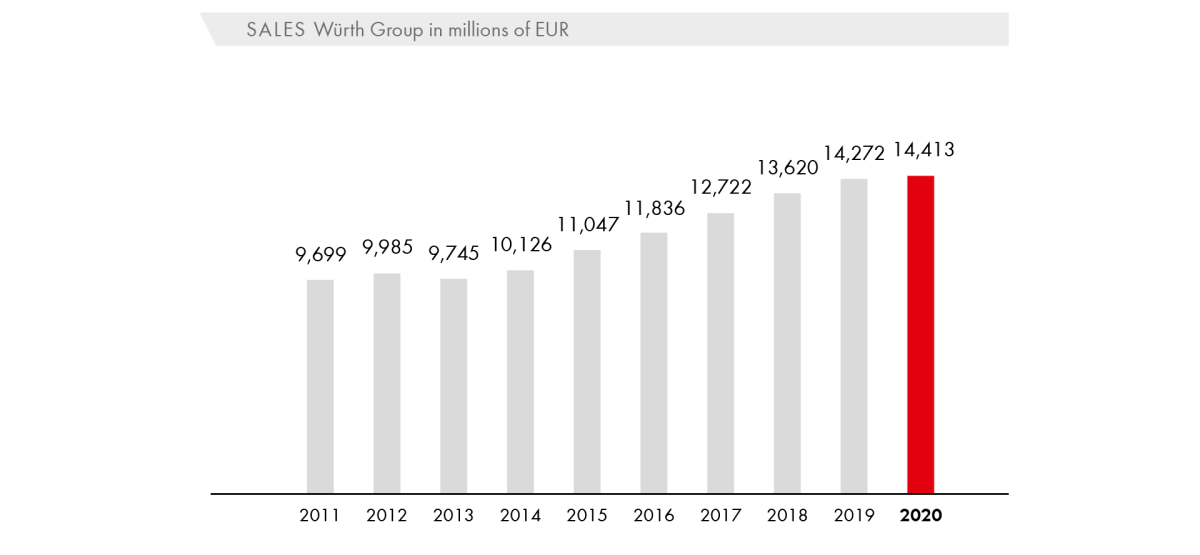
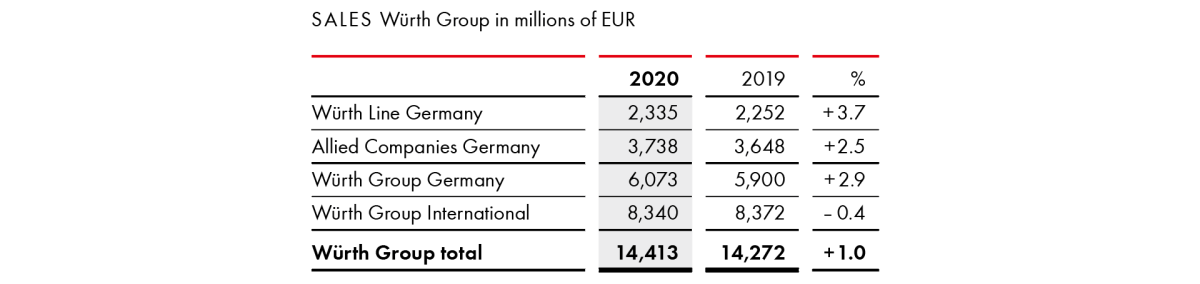
Developments at Adolf Würth GmbH & Co. KG tell a completely different story. Established back in 1945, it is the nucleus of the Würth Group and celebrated its 75th anniversary in 2020. It started operations on 14 July 1945 in Künzelsau as the screw wholesaler Adolf Würth. This marked the first chapter in the story of a global corporation. In the fiscal year under review, its 7,477 employees reached another milestone, generating sales of EUR 2,215 million, including intra-Group sales. This corresponds to an increase of 5.8 percent, outstripping the average figure for the Group by a wide margin. Alongside the sales force and in-house sales staff, the more than 550 pick-up shops are key to the company’s positive development. Even during the lockdown phases in Germany, these shops were open throughout due to their systemic importance, and our customers were able to cover their immediate needs at any time. This puts our Group’s flagship closer to our customers than any of our competitors. The response to physical distancing was a successful further expansion of e-business reliant on trust-based cooperation between sales force employees and our customers. Professionalism, both internally and externally, is one of the reasons behind the company’s high level of profitability. For the first time in the Würth Group’s history, a company managed to achieve an operating result in excess of EUR 200 million.
This earnings power is also a prerequisite for investments in forward-looking sales, logistics, and product solutions, for instance, the construction of the new Innovation Center that is being built on the campus in Künzelsau.
Overall, Germany accounted for an operating result of EUR 376 million (2019: EUR 389 million), making it the most profitable region.
Western Europe is home to many of the Group’s more established companies as it was there that the internationalization of the Würth Group began: one of the Group’s major success factors. Sales were down only slightly, by 1.1 percent to EUR 1,994 million. The region benefited from the continued positive development of the companies in Switzerland, especially the Swiss direct selling company, which was able to shift up a gear again after a period of restructuring. The companies in Austria were able to maintain the sales level they achieved in 2019. France is the country with the highest sales in the region, accounting for a share of over 35 percent. The companies based in France were able to hold their own relatively well during the COVID-19 crisis. Despite a macroeconomic downturn—including a full lockdown in the month of April and a large number of restrictions in May—considerable success was achieved in e-business. By way of example, the strategic focus on digital channels such as the online shop, the Würth App, and e-procurement led to 29.1 percent growth in Würth France’s e-business segment. The United Kingdom is also part of the Western European region. It is impossible to assess conclusively whether the 7.6 percent drop in sales in local currency terms in 2020 is an early consequence of Brexit or can be traced back to the COVID-19 pandemic.
The Americas, which includes both the US and Brazil, make up the continent that has been hit the hardest by the COVID-19 pandemic. In 2020, over 27 million people were infected in these two countries alone, with severe secondary effects on private and public life. In particular, the drop in sales witnessed during the first wave of the pandemic in April and May 2020 prevented the region from reporting better performance, with sales down by 3.1 percent in total. The strong euro also held sales growth back. In local currency terms, sales in the Americas region were slightly higher than in the previous year. In the US, the largest single market, developments varied significantly from business unit to business unit. Companies with significant activities in the personal protective equipment or chemicals product segments closed the year significantly better than those that rely heavily on the industrial sector.
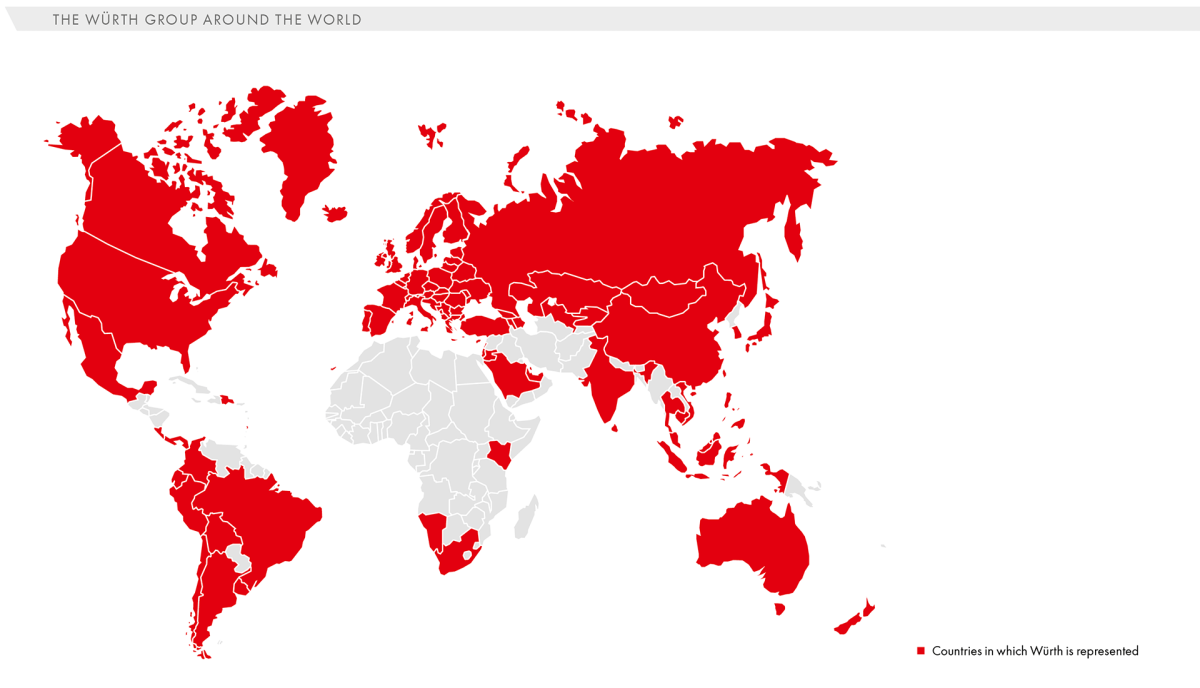
Another dominant topic last year was the US election campaign, the outcome of which has global implications far beyond the country’s own borders. The traditional pillar of the US economy, a low unemployment rate, relinquished some of its strength last year. Millions of people in the US have lost their jobs as a result of the crisis. From the Würth Group’s perspective, it is also crucial for private consumption in the US to be stimulated again and for global trade conflicts to be contained.
The companies in South America were able to close the year with respectable sales growth of 10.1 percent in local currency terms thanks to a strong fourth quarter of 2020.
Apart from Germany, Southern Europe was the only region to record an increase in sales. The 4.6 percent growth was, however, boosted by the 2019 acquisition of Grupo Electro Stocks, S. L. U., headquartered in Barcelona, Spain. It has always been part of the Group’s growth strategy to add targeted acquisitions to successful business areas where it makes sense to do so. After adjustments to reflect this acquisition, the Southern European companies closed the 2020 fiscal year with a 4.2 percent drop in sales. In terms of the absolute share of sales, Italy is the dominant country in the Southern European region, followed by Spain. In both countries, the effects of the first wave of COVID-19 in Europe were particularly dramatic. By taking fast, systematic action in response to the truly exceptional situation, supported by many years of trust-based cooperation with customers and suppliers, the Würth Group was able to generate growth over the year as a whole that can be considered satisfactory given the circumstances. In order to continue to drive growth dynamically in the region in the future, the number of employees was increased by 2.3 percent. Out of the 12,774 employees, more than 60 percent work as sales representatives.
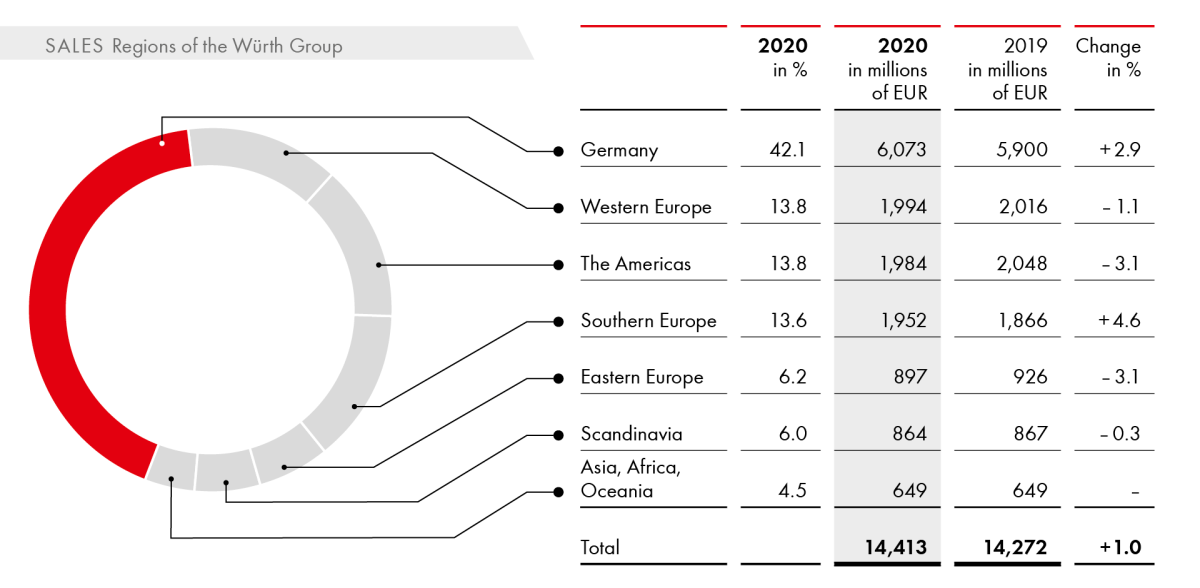
Sales in Eastern Europe slid by 3.1 percent; in local currency terms, the region remained on a par with the previous year. Countries such as Estonia, Hungary, and Russia also proved that growth can be achieved even in difficult times. The Würth Group employs more than 8,200 people in the region.
The structure of companies in the Scandinavian region has been relatively stable in recent years, which also reflects the maturity of the market. This stability was also evident in 2020, when sales charted only a very slight decline of 0.3 percent. This region is home to one of the model companies in the Würth Group, Würth Finland. With more than four decades of operations under its belt, the company consistently impresses with its excellent market penetration and high profitability. Würth Finland also spearheaded the spread of the successful “pick-up shops” sales concept within the Würth Line. The company now has 189 pick-up shops, four of which were added over the last 12 months.
Asia, Africa, and Oceania still only play a minor role for the Würth Group at present. The share of sales attributable to this region has been stable at a level of under five percent for years now.
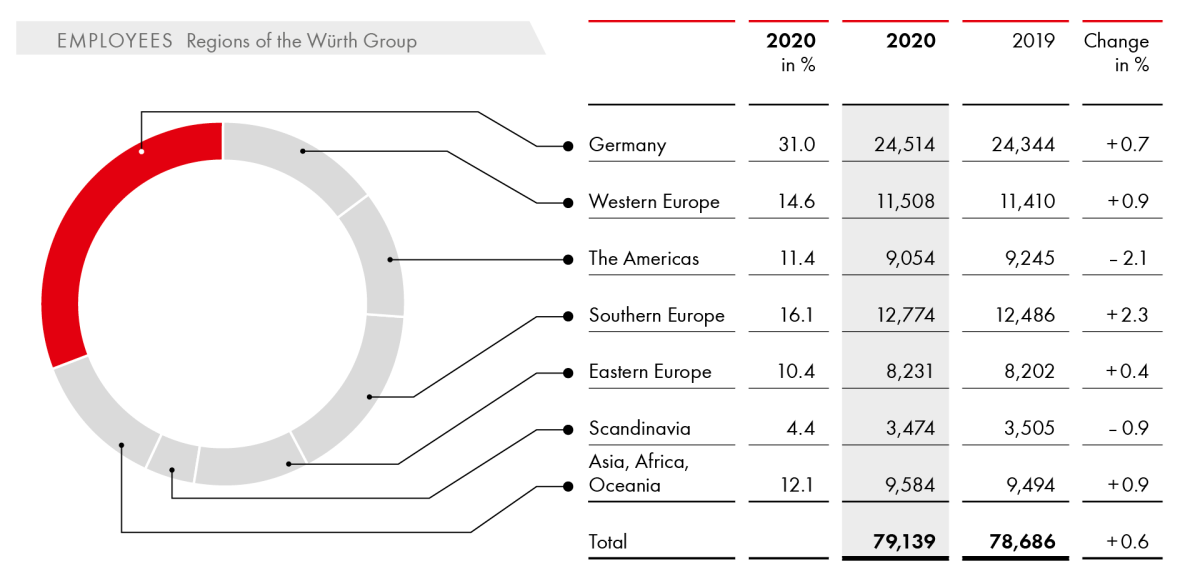
The divisions of the Würth Line
Würth Line operations focus on assembly and fastening materials, supplying customers in both trade and industry. Within the Würth Line, the operating business units are split into Metal, Auto, Industry, Wood, and Construction divisions.
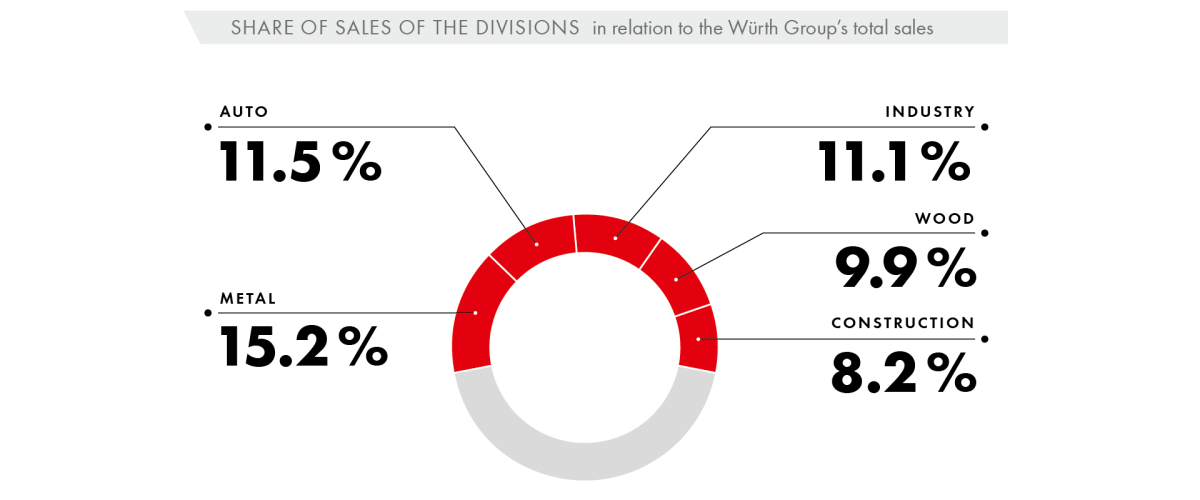
Metal division
The Metal division offers its customers innovative solutions to support them in their daily work today and in the future. Our core competency, direct selling, coupled with our pick-up stops and the various options for placing orders online, allows us to offer our customers top-quality advice and options for purchasing our products to suit everyone.
Metal subdivision
This subdivision directly serves customers in the metalworking and metal processing industries, and its main customers include metal and steel fabricators, fitters, and machine and vehicle manufacturers.
Installations subdivision
This subdivision concentrates on electricians, gas, heating and water installation firms, and air-conditioning and ventilation system engineers.
Maintenance subdivision
This subdivision addresses customers with in-house repair shops from a whole range of sectors, such as industrial enterprises, hotels, shopping centers, airports, and hospitals.
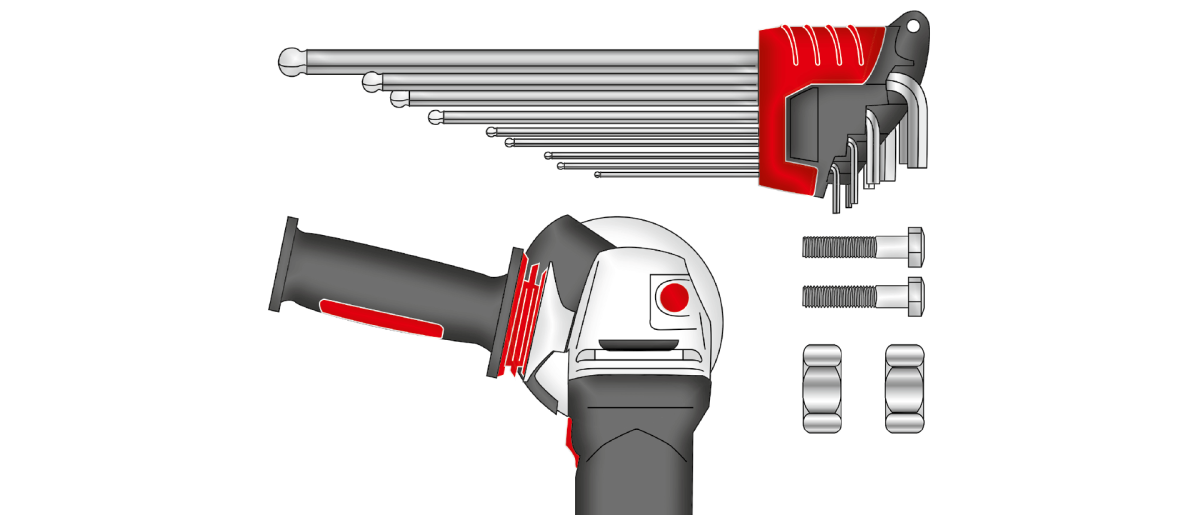
Auto division
Proximity to customers is a key success factor for the Auto division, along with an extensive range of top-quality products, as well as systems and services that make our customers’ processes easier and more efficient. In complementary specialist areas such as the special tools segment, we help our customers to meet the rapidly changing demands of the automotive and commercial vehicle market. We also offer solutions for alternative drive systems and the increasing digitalization in the automotive aftersales segment.
Car subdivision
The customers in the car subdivision include vehicle manufacturers, brand-specific and independent car dealers, customers with large vehicle fleets, bodywork specialists, vehicle restorers, tire changing businesses, and businesses in the bike segment.
Cargo/Commercial Vehicles subdivision
The customers of this subdivision are authorized commercial vehicle repair shops, independent commercial vehicle repair shops, repair businesses focusing on construction and agricultural machinery, transportation and logistics companies, bus companies, businesses specializing in repairing and renting working platforms and forklifts, public-sector municipal utilities and waste disposal companies, as well as companies from the agricultural and forestry sector.
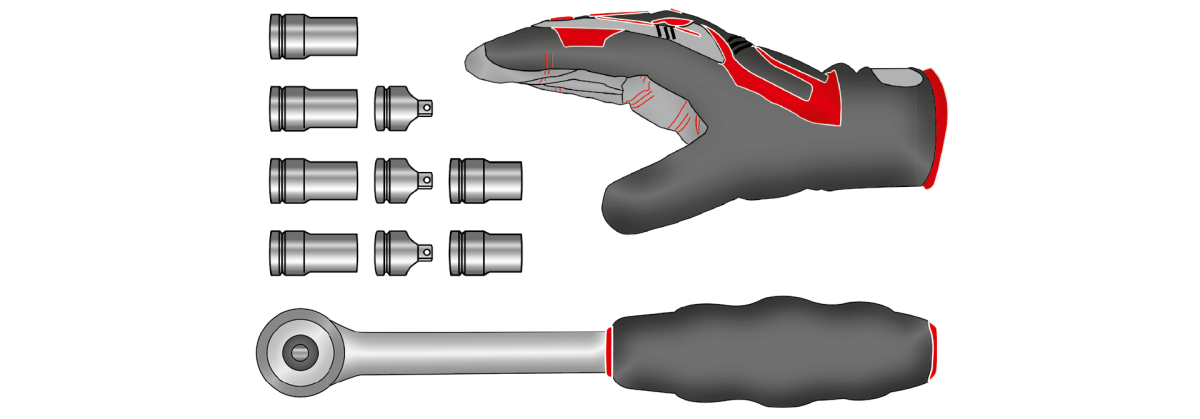
Industry division
The entities of the Industry division are specialized companies with a complete range of assembly and connecting materials for industrial production, maintenance, and repair. In addition to this comprehensive standard range, the division’s strength lies in customized logistics concepts for supply and service, along with the provision of technical consulting.
The innovative further development of procurement and logistics systems within the Industry division emphasizes the role of full automation and systems in stocking and replenishing Würth products for manufacturing customers. One key focus remains the maximum security of C-part supplies directly at the place of consumption, in the warehouse and at the workstation. All solutions are made available as part of a holistic approach to the supply of production and operating resources. As in the past, the focus is on expanding digital processes and sales channels.
The strategic focus remains on personal on-site customer service thanks to a global network of companies and, as a result, the same high standards for quality, products, and processes across the globe.
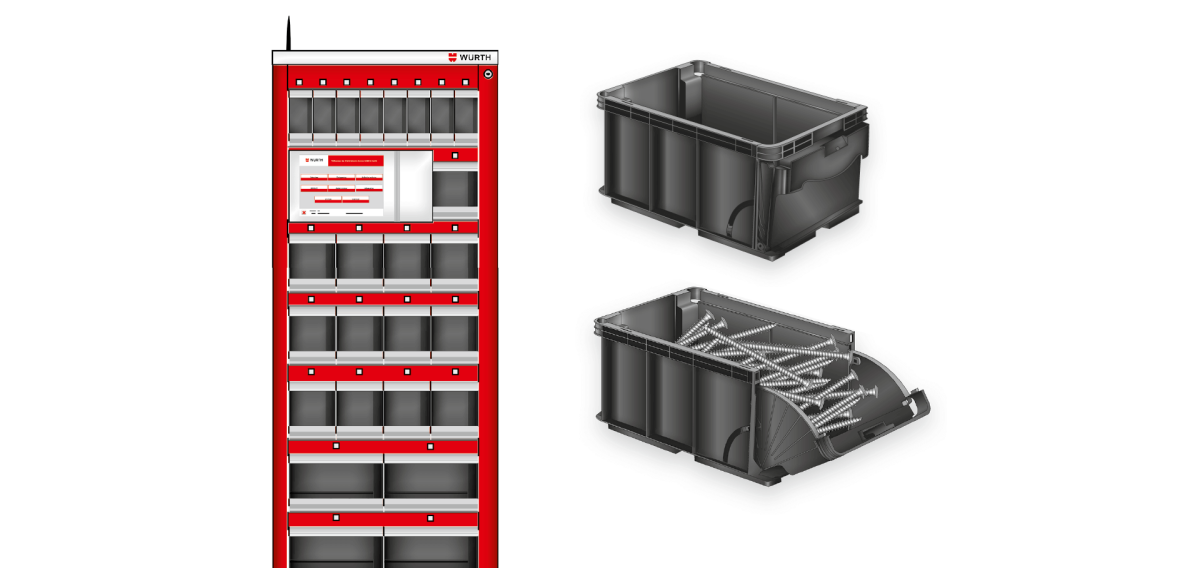
Wood division
The Wood division supports its customers in the entire woodworking and wood processing trade with a tailored product portfolio and specific application solutions. The product range includes wood screws, fittings, chemical-technical products, as well as material treatment and structural connection products.
Thanks to a high level of expertise and holistic sales solutions, we not only offer our customers products that are perfectly tailored to suit their needs, we also see ourselves as a personal advisor, assisting our clients from the preparation of their initial plans to the completion stage.
In these endeavors, the Wood division is responding to the latest trends in the industry: The WÜDESTO online configurator already allows customers to create customized furniture elements and order semi-finished parts with exact dimensions in Germany and Austria.
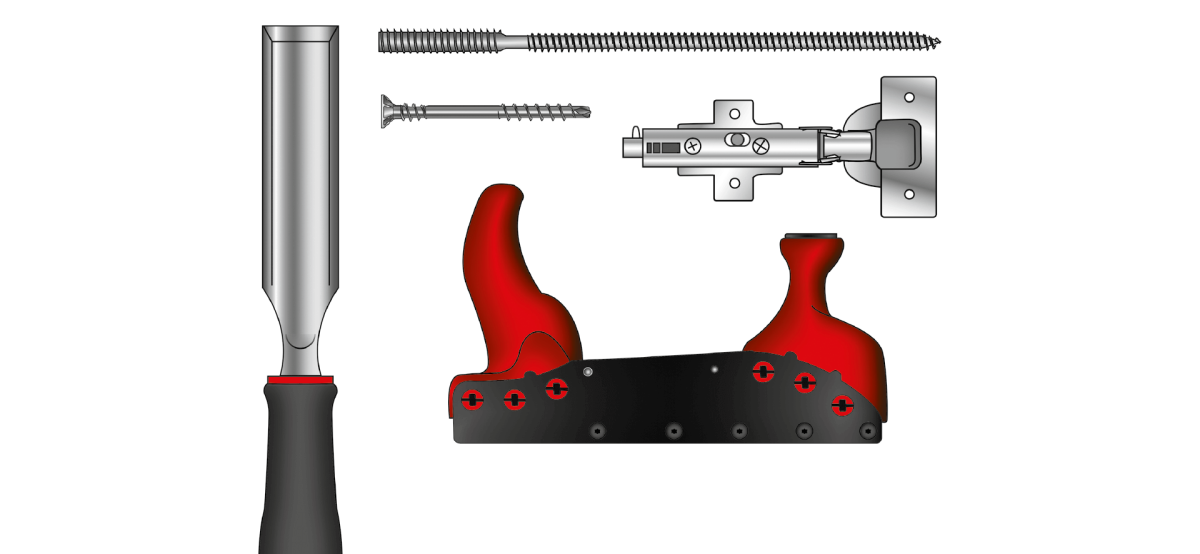
Construction division
The Construction division aims to supply construction companies across the globe at the regional, national, and international level with high-end products and services that are as standardized as possible. The pick-up shops are the ideal port of call for customers looking to cover their immediate needs. Sales representatives act as a permanent point of contact at the construction site. They are responsible for optimizing the processes associated with the main trades involved in the shell construction phase and in the various technical building installations as part of the project business.
The Construction division encompasses all sales units responsible for serving customers in the building and civil engineering industry and the finishing trades. Cultivation of the market focuses on construction companies, technical building equipment, roof and wood construction customers, finishing and facade specialists, and direct supplies to construction sites. Customized service and logistics solutions are also provided, such as equipped material stores directly at the construction site. There is an increasing focus on strategic target groups such as builders, planners, architects, and project managers.
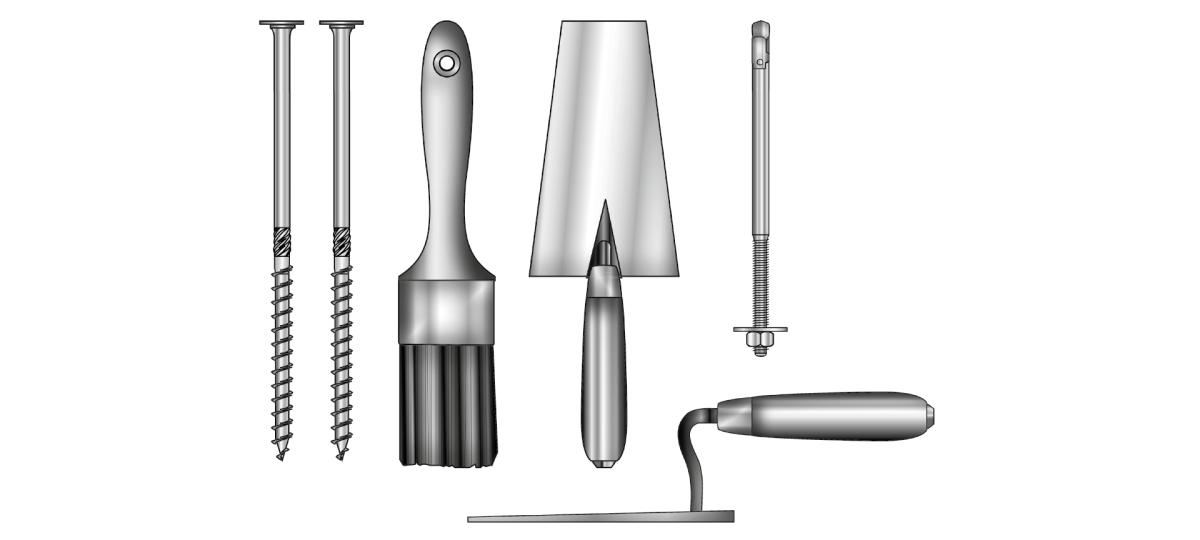
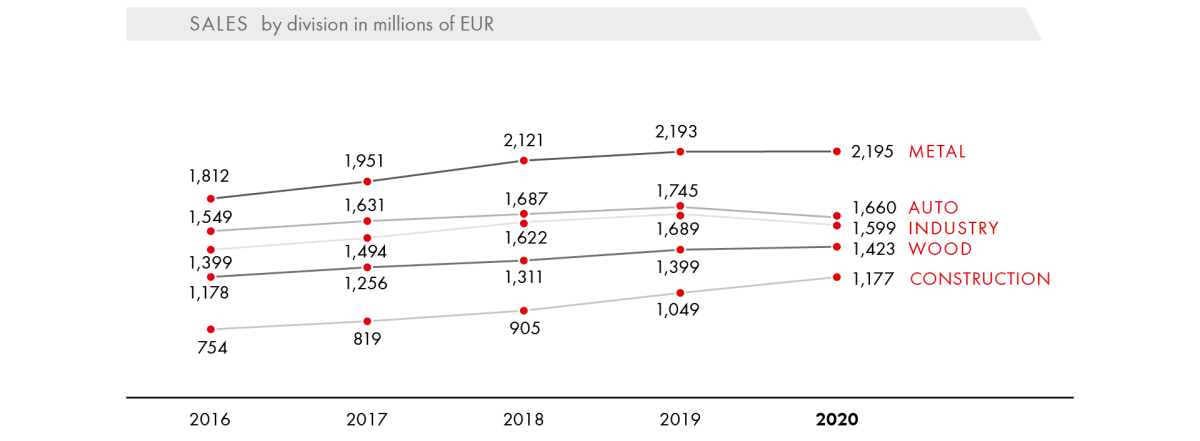
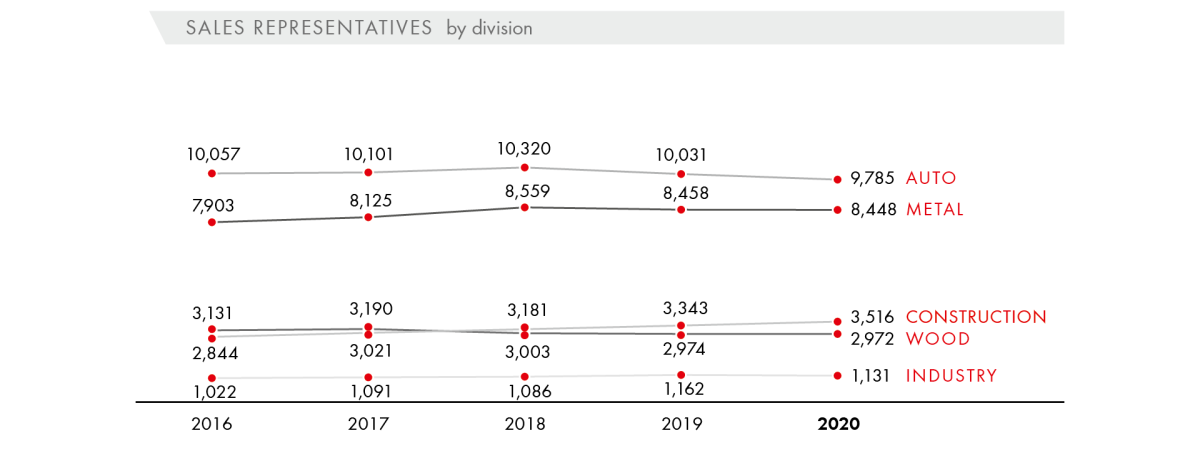
The business units of the Allied Companies
The Allied Companies operate either in business areas related to the Group’s core business or in diversified business areas, rounding off the Würth Group’s portfolio. They are divided into nine strategic business units. With the exception of a small number of manufacturing companies, the majority are sales companies operating in related areas.
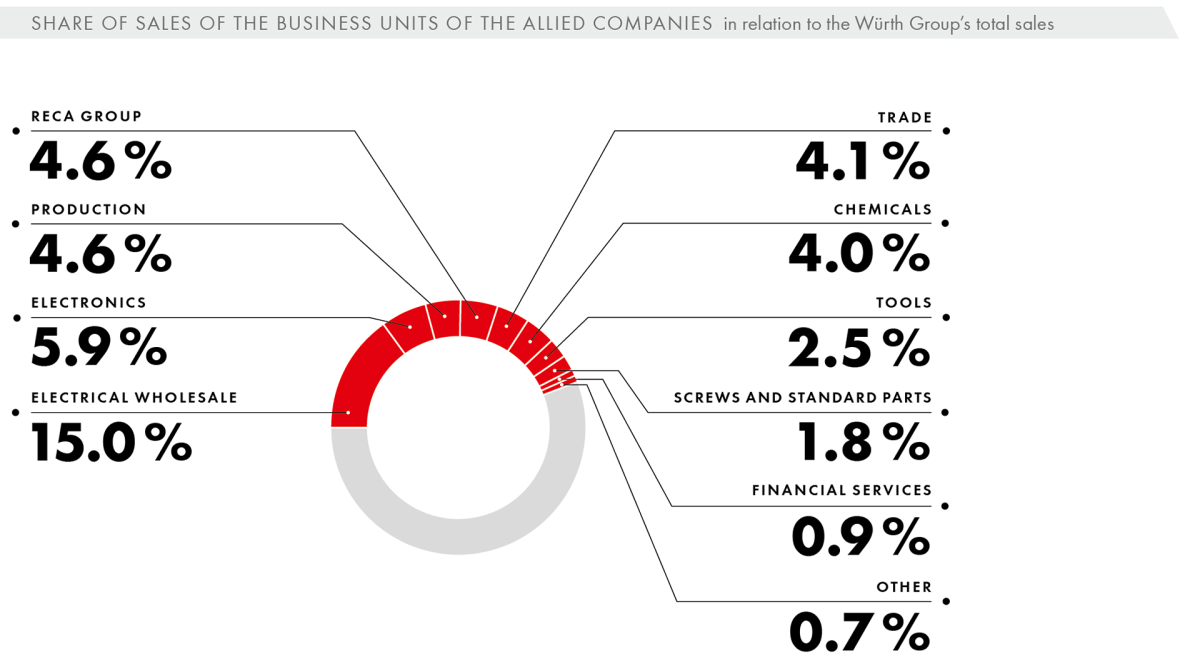
Electrical Wholesale
The business activities of these companies include products and systems covering the areas of electrical installation, industrial automation, cables and lines, tools, data and network technology, lighting and illumination, household appliances and multimedia products, as well as electrical domestic heating technology and regenerative power generation. Trading activities are supplemented by extensive consultancy and service ranges and are aimed at professional customers from the trade, industry, and retail/wholesale sector.
- Electrical Wholesale reaps benefits from COVID-19 pandemic: secure power supply considered “systemically important”
- Growth outstrips market trend: electrical wholesalers achieve sales in excess of EUR 2.0 billion for first time in 2020
- More than 5,600 employees
- Double-digit sales growth in German market
- Italy and Spain hit particularly hard by COVID-19 pandemic, but comparatively few restrictions on companies and satisfactory development thanks to systemic importance
- Pandemic gives extra boost to fast-growing e-commerce business
- Early moves to build up product stocks and extensive COVID-19 precautions ensure unrestricted supplies to customers during pandemic
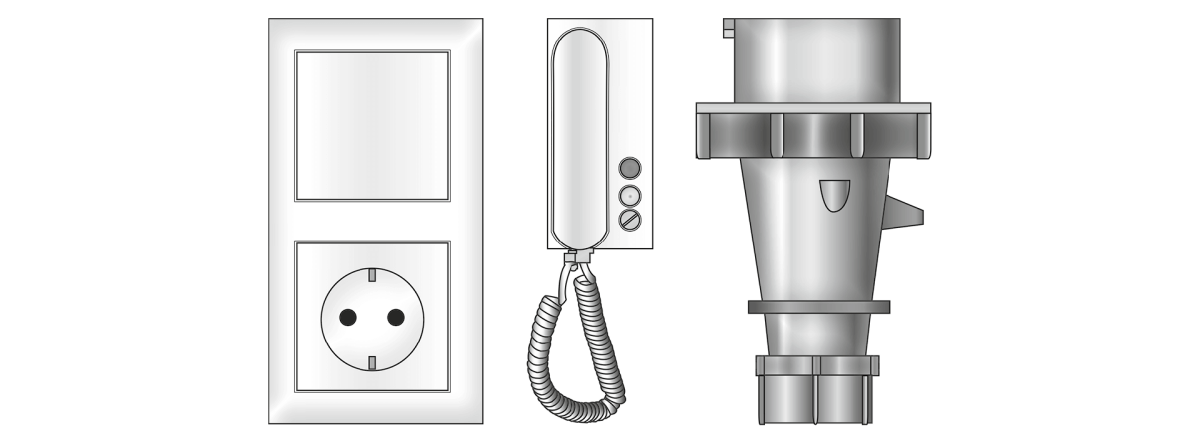
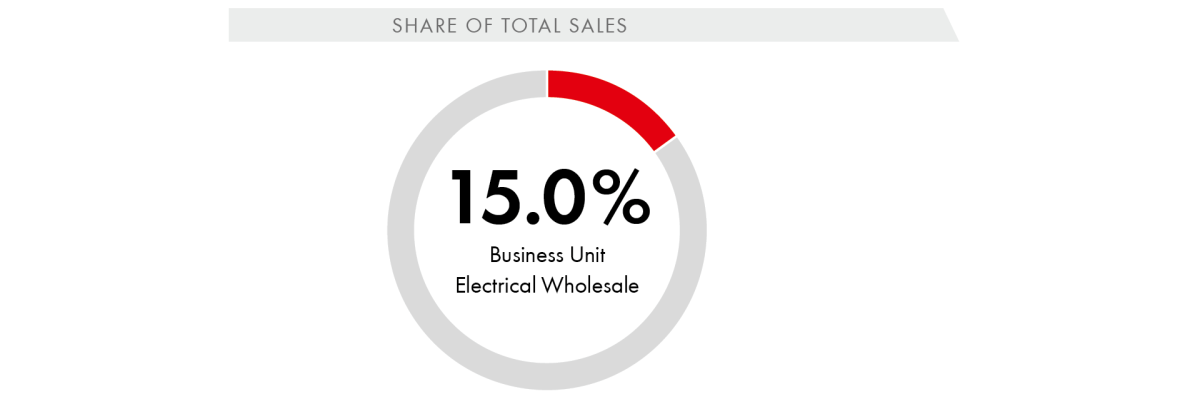
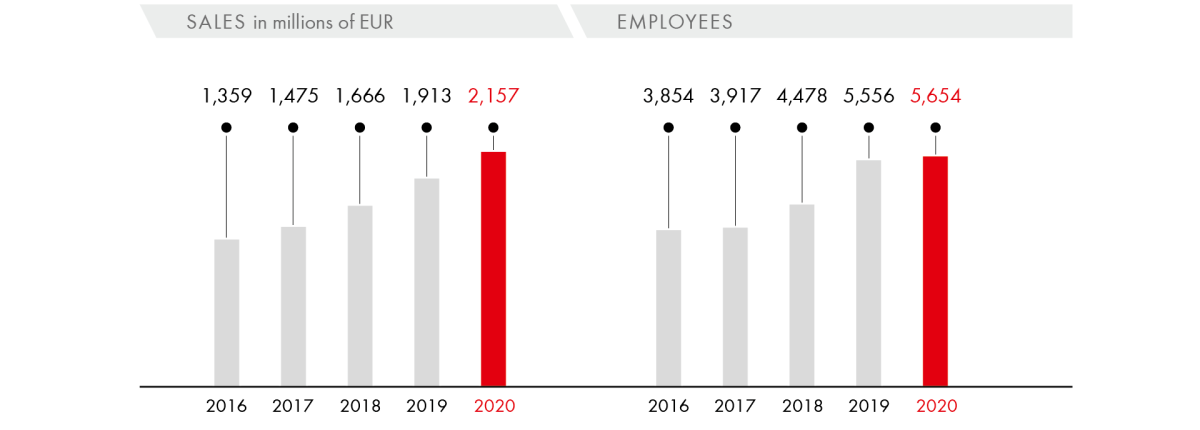
Electronics
The Electronics unit produces and sells electronic components such as printed circuit boards, electronic and electro-mechanical elements, and full system components from smart power and control systems.
- Despite challenges associated with COVID-19 pandemic, successful year overall
- Focus on digital sales solutions, trade fairs and product landscapes
- Second place as product of the year in the readers’ choice of industry magazine ELEKTRONIK for Würth Elektronik eiSos WE-LAN AQ (LAN transformer manufactured by means of full automation with innovative coil winding technique)
- German Electrical and Electronic Manufacturers’ Association (Zentralverband Elektrotechnik- und Elektronikindustrie) confirms Würth Elektronik CBT’s leading position among Europe’s printed circuit board manufacturers
- Würth Elektronik eiSos relies on more sustainable alternatives for packaging materials, such as filling material and adhesive tape made of recycled paper
- Successful structural adjustment of Würth Elektronik CBT plant in Schopfheim to ensure future competitiveness
- Relocation of Wurth Electronics ICS USA to new company site in Miamisburg, Ohio, featuring twice previous production area
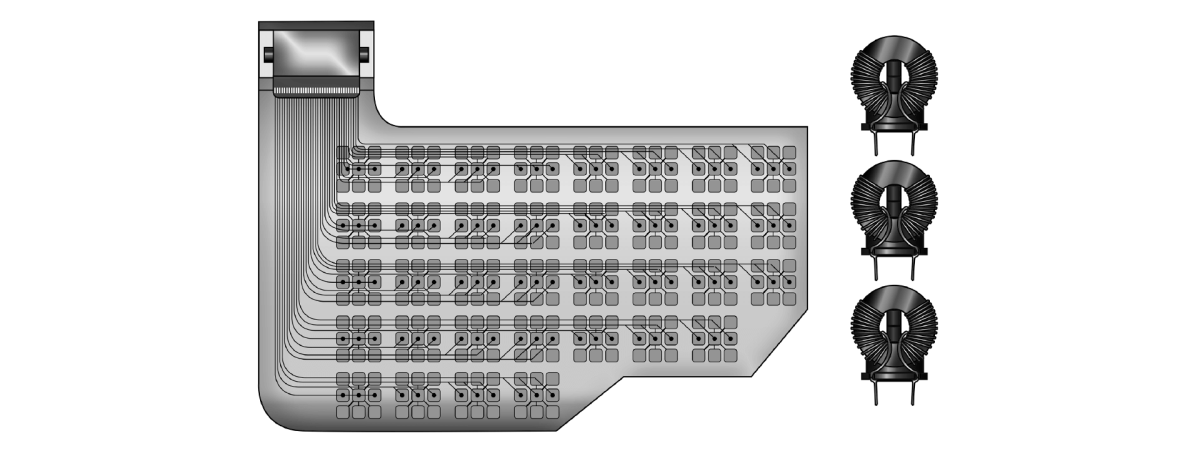

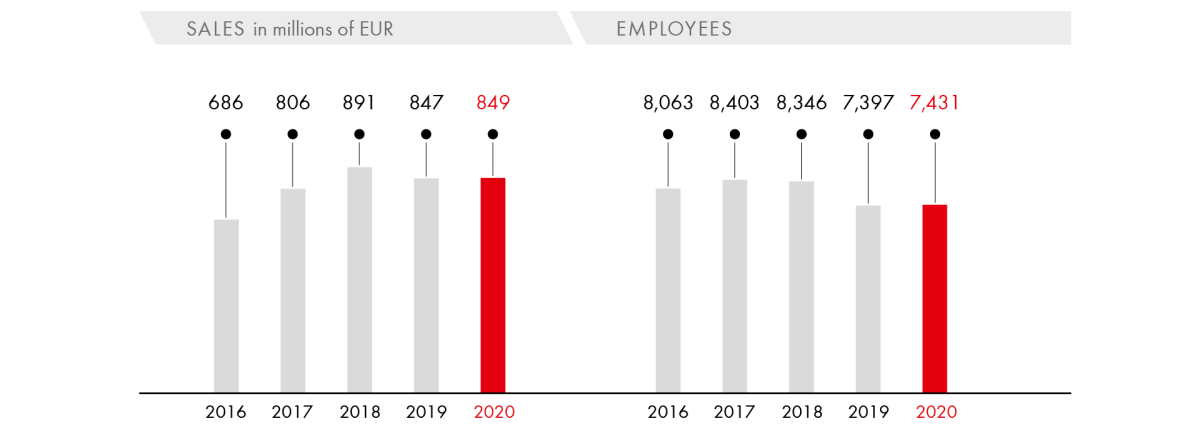
Production
The range in this business unit includes the production of cold-formed parts, forming and punching tools, a variety of fasteners and fastening systems, furniture fittings, plastic assortment and storage boxes, as well as factory and vehicle equipment. The business unit supplies a range of customers, including customers from the construction sector, the automotive industry, manufacturers of kitchens and household appliances, and wholesalers.
- Automotive sector hit hard by pandemic, otherwise only minor or no losses, although growth targets not achieved
- Commissioning of new production hall at SWG Schraubenwerk Gaisbach: beech roof structure considered pioneering project
- Completion of production hall spanning useful area of 13,000 m² at Arnold Umformtechnik to speed up work processes and bring the Fastening Systems and System Development areas together in one location
- FELO expands usable floor space by 1,600 m² with building extension
- Successful consolidation of Grass warehouses thanks to completion of new warehouse building in Hohenems
- Further development of Vionaro drawer system: Grass expands range to feature 8-millimeter Slim Line Drawer side made of steel
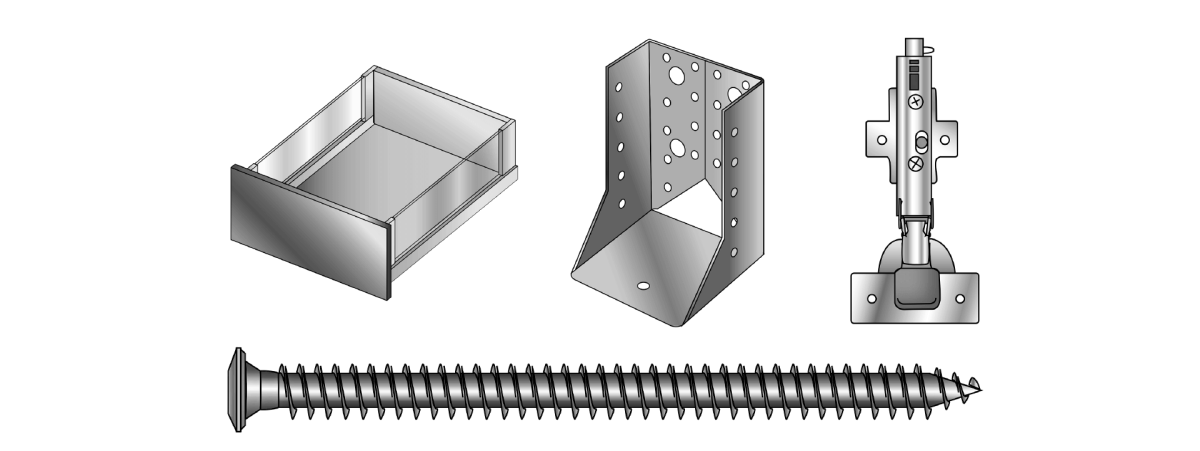
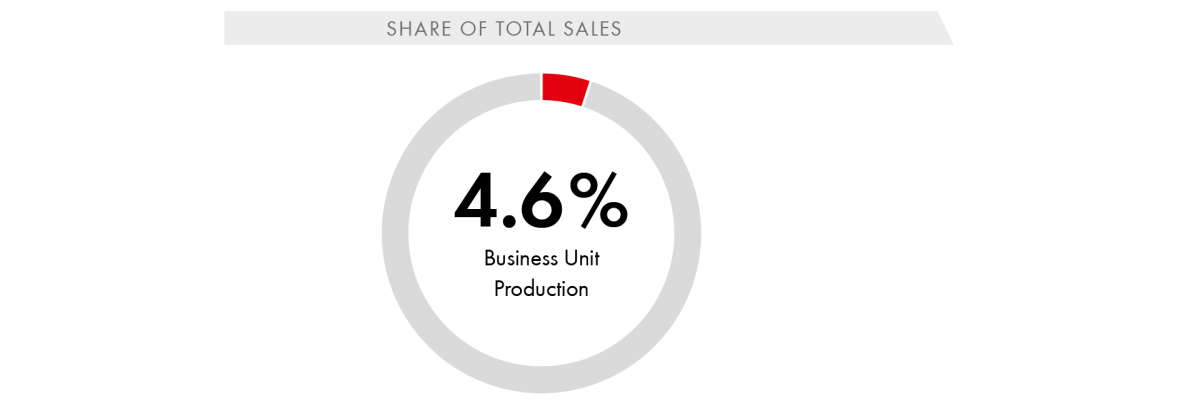
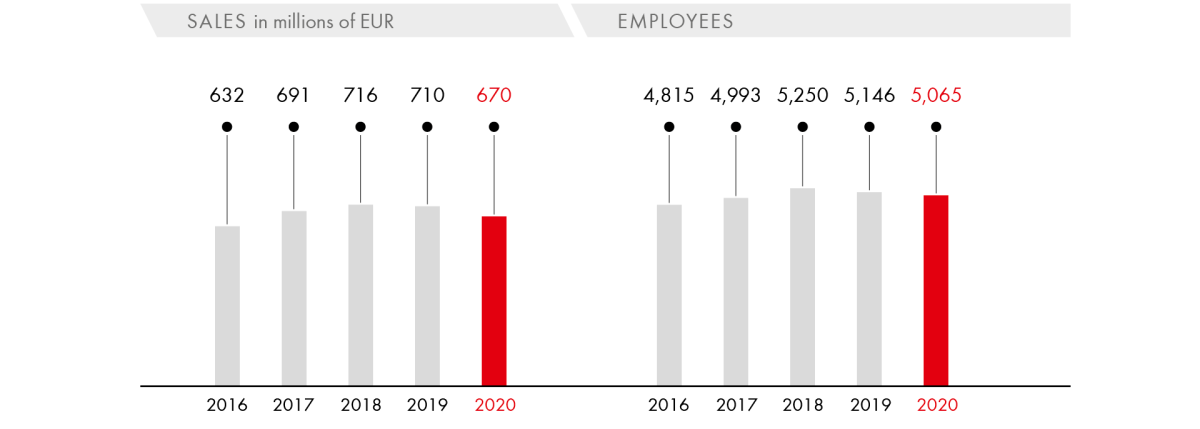
RECA Group
The RECA Group companies supply tools, assembly and fastening materials, and C parts to industry and directly to construction, wood, metal, and car business customers, as well as to customers in the cargo sector, in 19 European countries. Specialists in workwear, advertising materials, and vehicle equipment complement the company portfolio.
- Declining sales in industrial business, where impact of COVID-19 pandemic significantly more pronounced than in slightly growing craft sector
- Focus on services that help customers reduce procurement costs for small parts, such as KANBAN and RFID-supported storage systems, SECO® shelf management system (service concept) for trade customers, shelf and vending solutions for direct retrieval of goods, and automated reordering for customers
- Expansion of central logistics in Wels, Austria, to provide logistical support for growth activities in years ahead (delivery capability, service level)
- Continued good prospects for future thanks to combination of digital sales systems and customer support by traditional sales force on site and by telephone
- Tapping markets by implementing trading partner concept in (mainly European) countries in which RECA Group has not been active to date
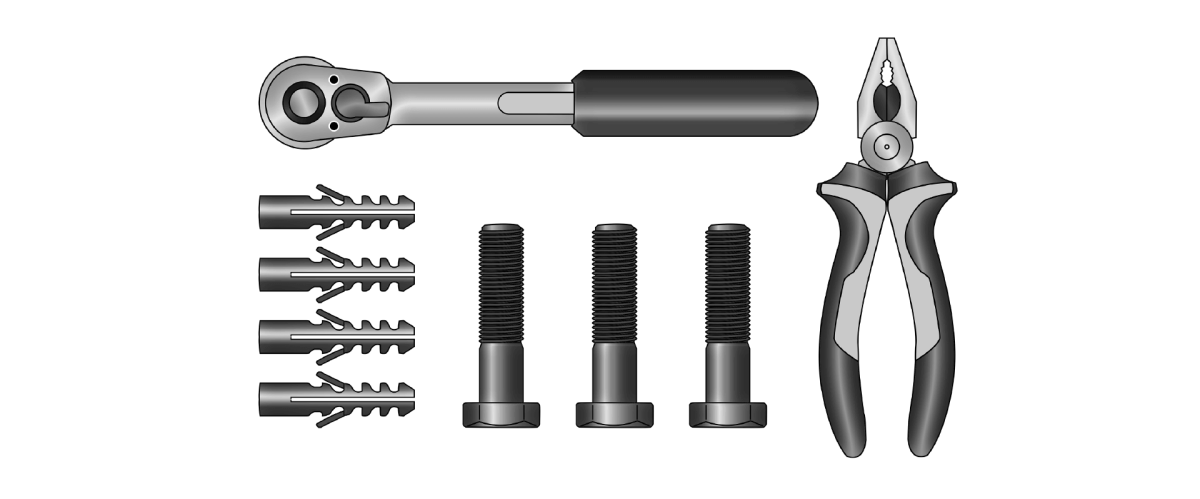
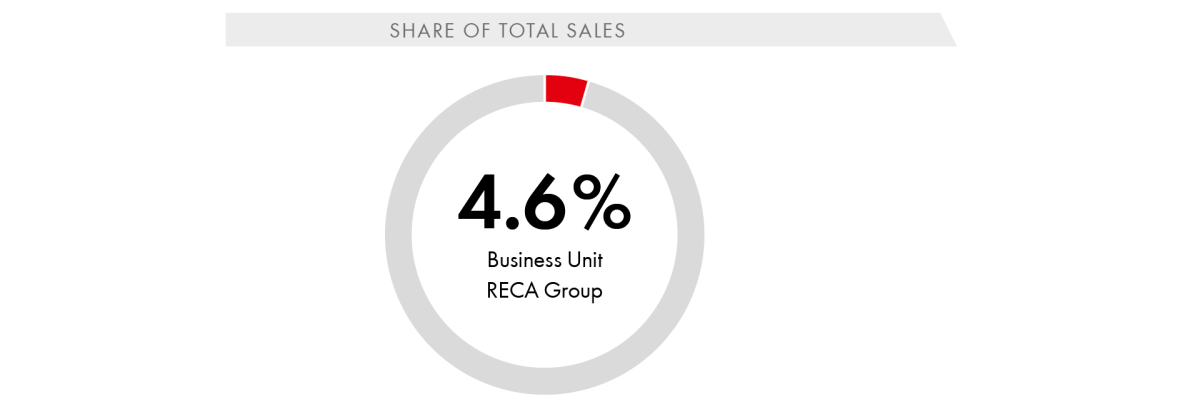
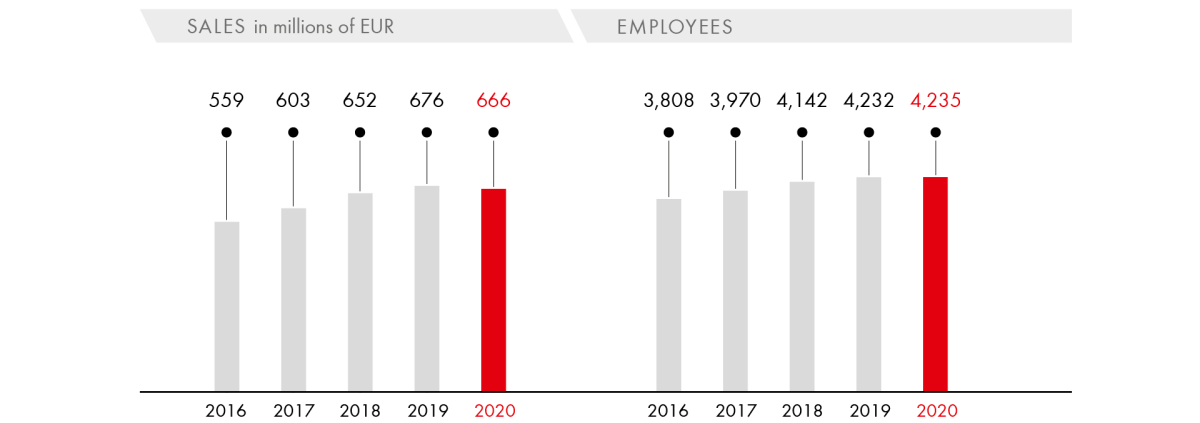
Trade
Companies in this business unit sell installation, sanitary, fastening and assembly materials, garden products, power tools, and hand tools. The range also includes furniture fittings for specialist stores and retailers as well as products for DIY stores and discount stores.
- Despite slump in sales in April, the exceptional year 2020 closed on positive note due to boom in DIY and home improvement sector sparked by the pandemic
- Expansion of e-commerce and digitalization
- Investments in IT infrastructure and forward-looking technologies such as electronic shelf labels
- Find-it shelf: newly developed all-in-one solution for stationary retail to allow products to be found on shelf in electronically controlled process
- Strengthened social media presence featuring dedicated company blogs, as well as use of new platforms
- Reduced packaging variety for better sustainability and compliance with highest environmental and safety standards based on customer specifications
- Special solutions tailored to customer needs and requirements
- Customer segmentation for optimum and targeted customer support
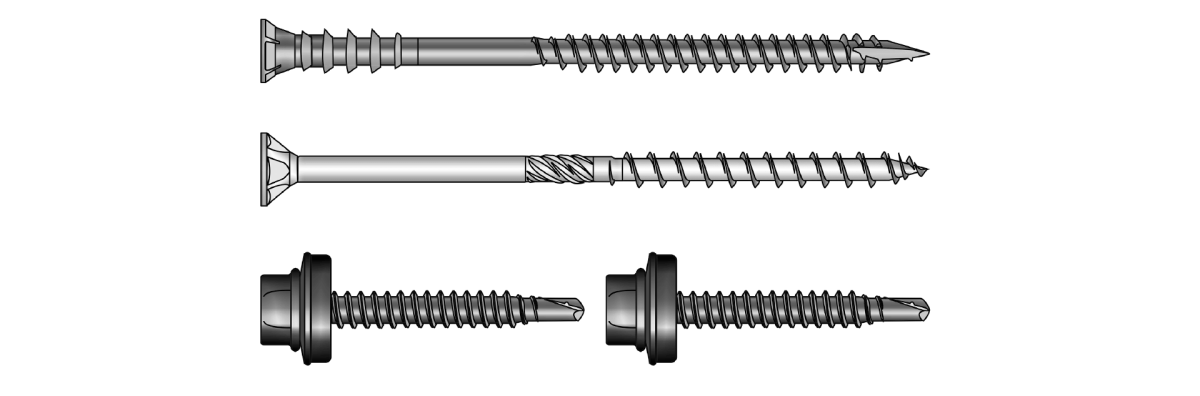
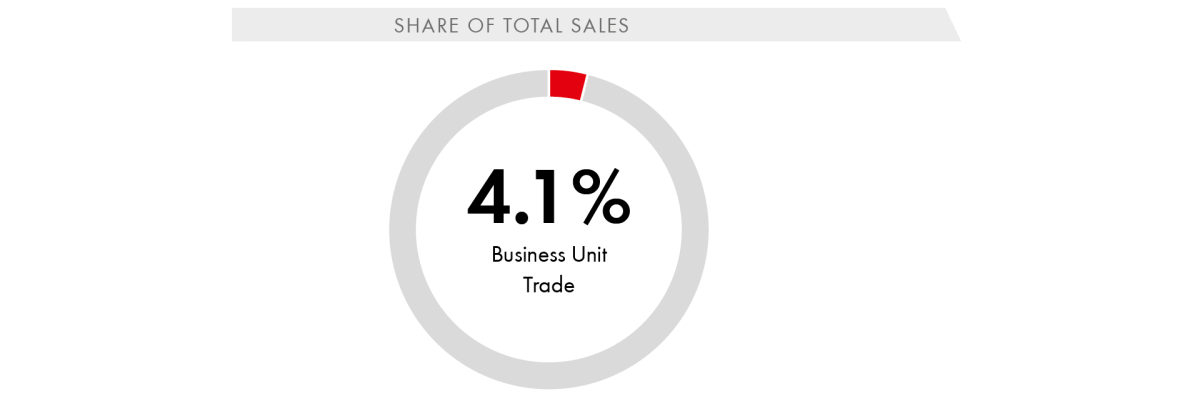
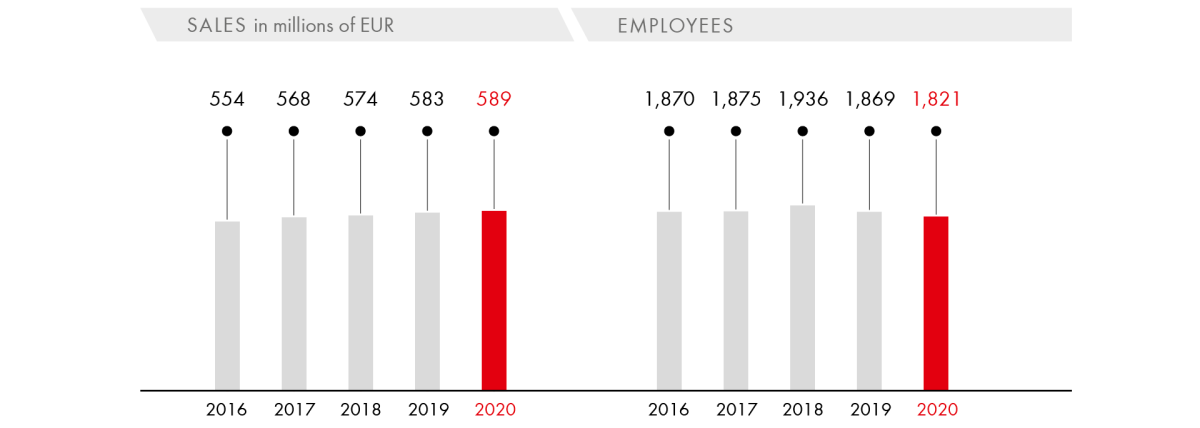
Chemicals
The companies in the Chemicals unit are responsible for the development, manufacturing, and distribution of chemical products for the automotive, industrial, and cosmetics sectors. They distribute both their own brands and private-label products and are renowned as innovation specialists and experts in their niche areas.
- TUNAP Group: positive sales development thanks to disinfectant products
- AP Winner China: new sustainable, antibacterial and VOC-reduced/VOC-free cleaners in novel, refillable spray bottles that spray like aerosols, but without propellants
- Relaunch of Dinitrol brand (corrosion protection, sealants, and adhesives) in Germany
- Increased focus on cost structures
- Promotion of digitalization in companies by expanding use of webinars
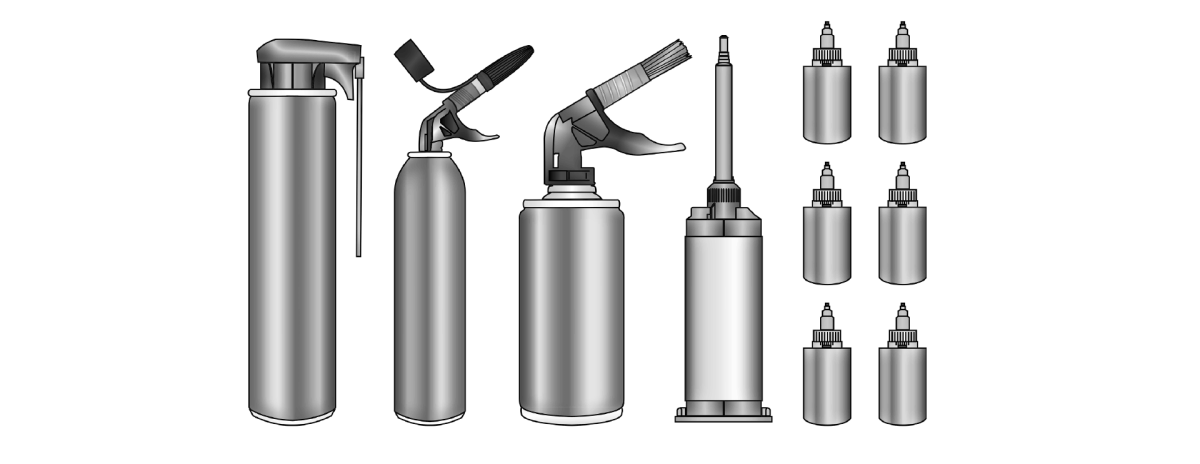
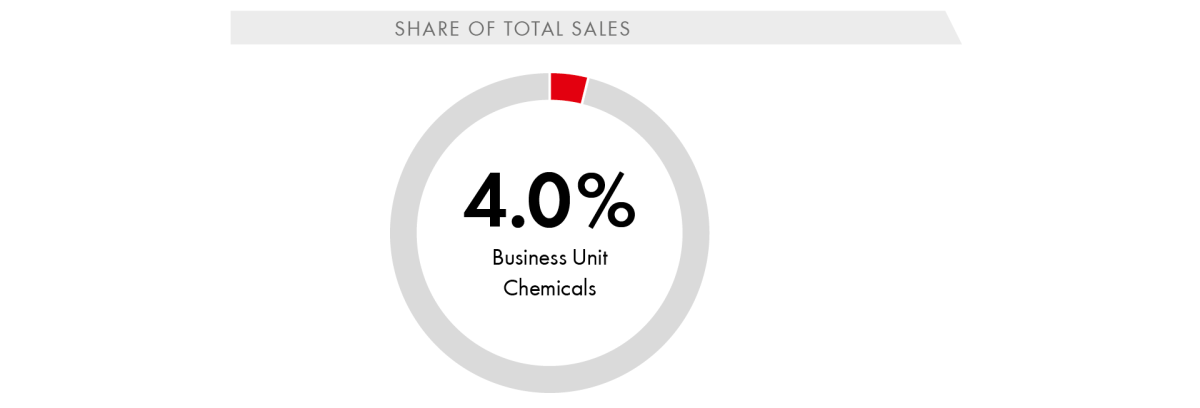
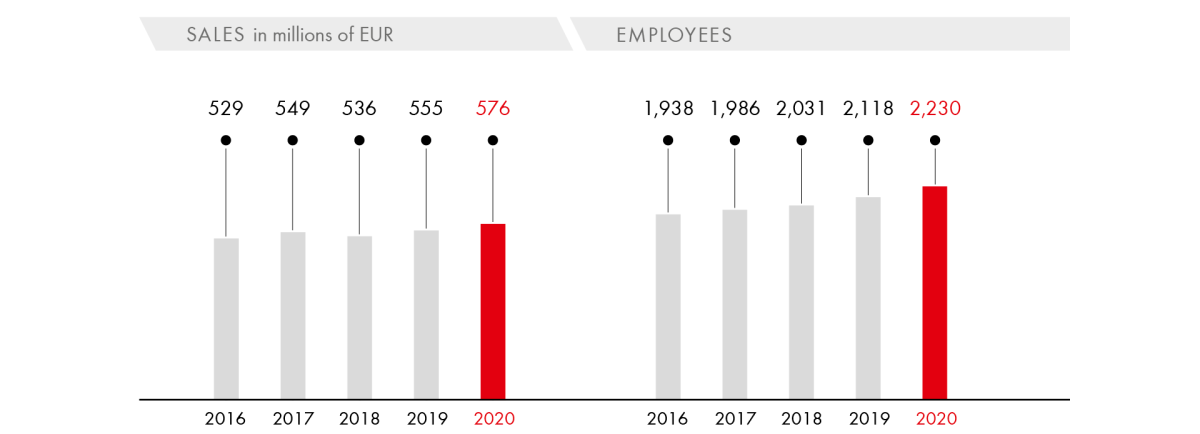
Tools
The tools companies supply customers in the metalworking and metal processing industries, particularly in the mechanical and plant engineering sector, and in the automotive manufacturing and automotive supplier industry. They sell products from the areas of drilling, milling, turning, clamping, grinding, testing and measurement equipment, hand tools, operating equipment, machinery, and personal protective equipment.
- COVID-19 crisis sparked further deterioration of economic situation for customers in mechanical and plant engineering sector and automotive industry
- Restructuring measures prompted by sharp drop in sales of 11.7 percent in 2020
- Expansion of e-business by forging ahead with web shop, EDI connection, and electronic catalogs
- Continued roll-out of SAP and online shop systems at national companies from 2021 onwards
- Expansion of data structure for 2D and 3D tool data to support digitalization of customer production processes
- Focus on customer acquisition in medical, food, transport and logistics, energy and environment, construction, and recreational vehicle sectors
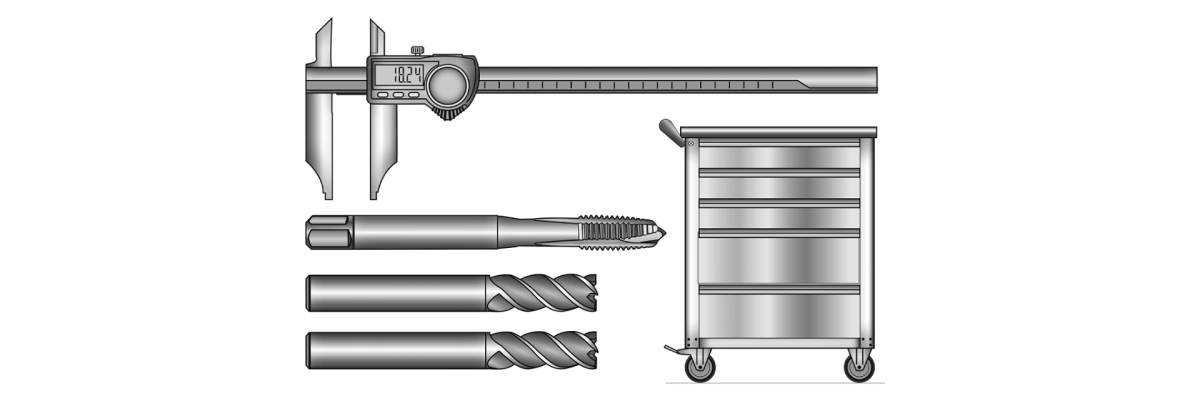
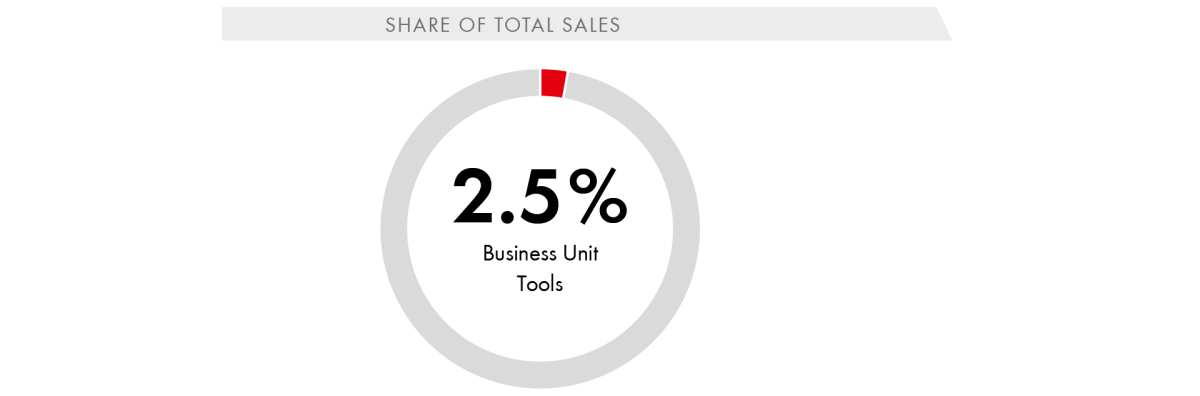
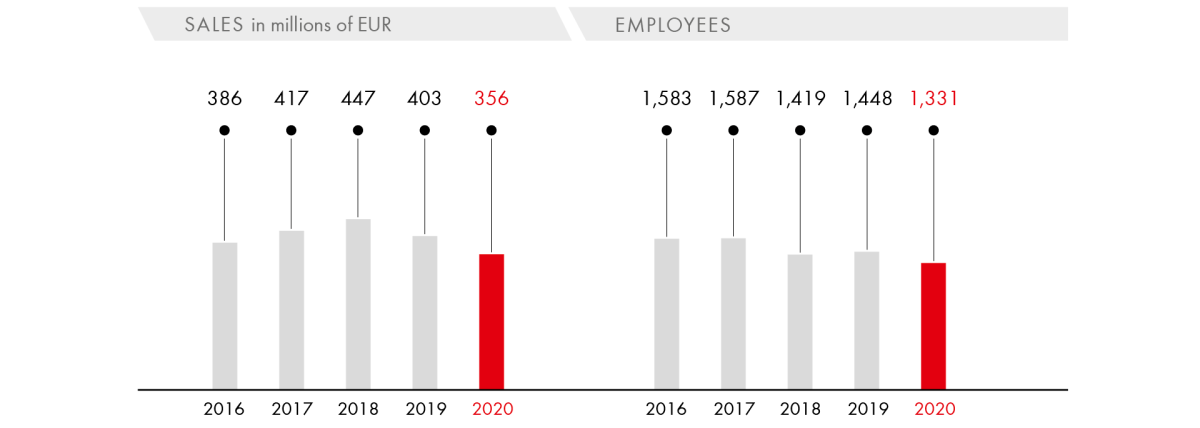
Screws and Standard Parts
The stainless steel companies are product specialists with supply concepts for industry and trade. The unit’s main business activity is the sale of stainless connecting elements, in particular DIN and standard parts. The hydraulic companies specialize in trading in hydraulic connection technology and providing the associated services.
- Compensation for drop in sales in April and May triggered by COVID-19 pandemic almost possible year progressed
- Focus on telemarketing at stainless steel companies for closer customer contact
- Service sales reported by hydraulics companies prove resilient in difficult year 2020, declining only slightly in year-on-year comparison, growing again in the last quarter
- Wholesale business sees drop in sales running into high single digits due to economic situation and pandemic
- System update to support further digitalization of processes such as EDI connections
- Preparations under way to integrate e-shop into CRM module in sales to enable optimal customer care

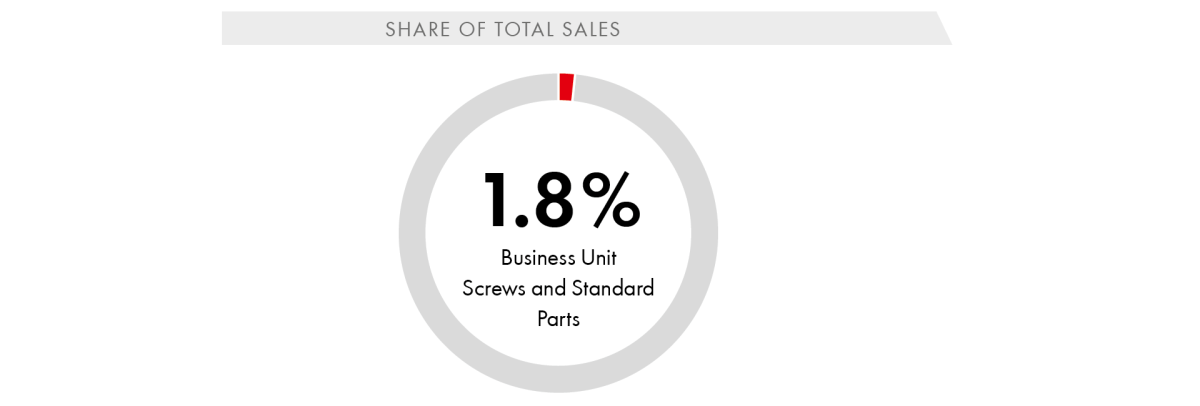
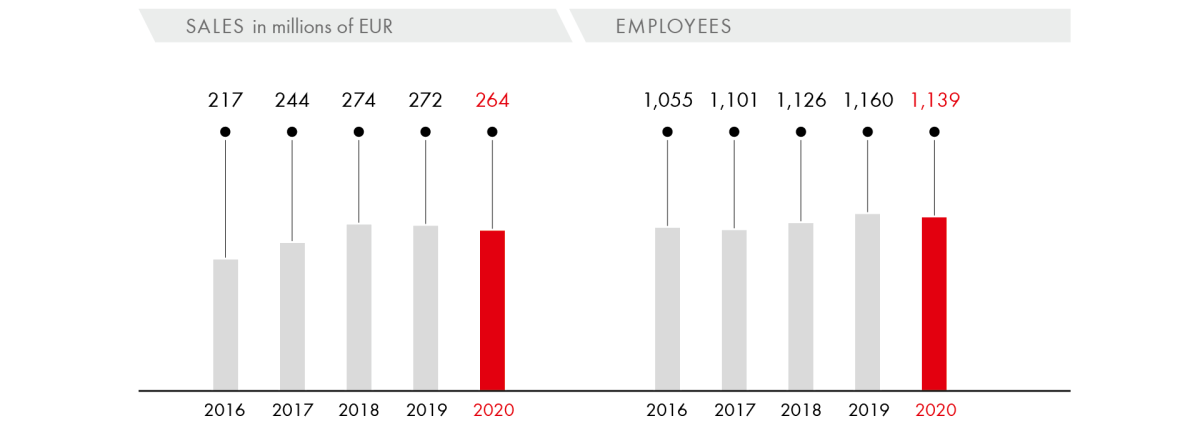
Financial Services
In addition to its conventional screw-based business, the Würth Group has also specialized in financial services for business and retail customers alike. Financing, leasing, retirement plans, property and personal insurance as well as asset management are among the services offered.
- IBB Internationales Bankhaus Bodensee AG: positive earnings development again
- Leasing companies report mixed performance due to COVID-19 pandemic: hardly any noticeable impact on new business volume in Switzerland and Denmark, Germany hit hard by developments in key mechanical engineering and automotive sectors
- Waldenburger Versicherung: earnings improve again thanks to combination of premium growth above market average and good loss ratio
- Further investments in digitalization, sales, and staff ensure future viability
- Würth Financial Services: sales record despite COVID-19 pandemic
- Successful integration of Optima Versicherungsbroker AG to strengthen market position in Switzerland
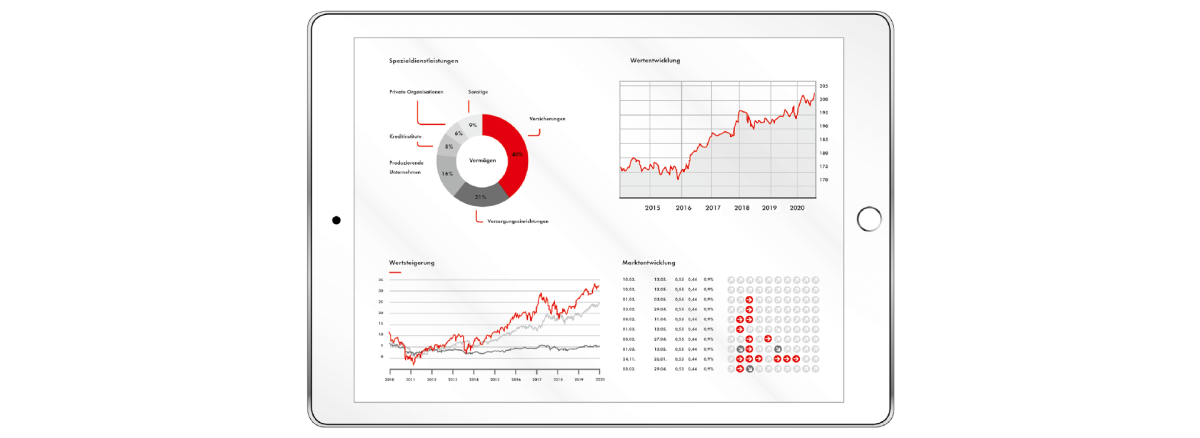
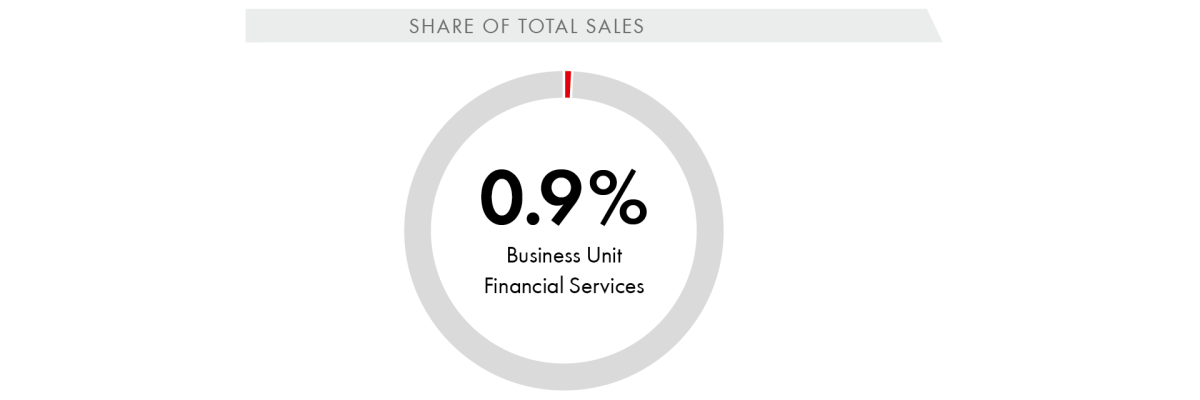

- Operating result slightly up on previous year
- Cash flow increases significantly
- Equity ratio of 43.8 percent
At EUR 775 million, the Würth Group’s operating result is slightly above the prior-year level. Due to the proportionate increase compared to sales, the rate of return remained constant at 5.4 percent (2019: 5.4 percent). We have calculated the operating result as earnings before taxes, before amortization of goodwill and financial assets, before the collection of negative differences recognized in profit or loss, before the adjustment of purchase price liabilities from acquisitions through profit or loss, and before changes recognized in profit or loss from non-controlling interests disclosed as liabilities.
The heavy reliance on the automotive industry and the mechanical engineering sector in Germany also had a negative impact in the 2020 fiscal year. The operating result in this market fell by 3.3 percent to EUR 376 million (2019: EUR 389 million). The negative trend in the industries mentioned put pressure on earnings at companies trading in tools, within the Würth Elektronik Group, and at individual manufacturing companies. The share of the Group’s overall result attributable to the German companies fell to 48.5 percent as a result, with the return on sales amounting to 6.2 percent (2019: 6.6 percent). With an operating result in excess of EUR 200 million for the first time, Adolf Würth GmbH & Co. KG made what was by far the biggest contribution to earnings of any other single company in the Group. Other top performers within Germany include: Würth Elektronik eiSos, Reca Norm, and Fega & Schmitt Elektrogroßhandel.
Restructuring measures taken in the past at established companies, such as companies specializing in fittings or the Würth Line, had a positive impact in the 2020 fiscal year. This, combined with a rapid and efficient response to the new challenges brought about by COVID-19, resulted in the companies outside Germany posting a total operating result of EUR 399 million (2019: EUR 381 million). This equates to an increase of 4.7 percent. Taking account of the fact that significantly more companies outside of Germany were affected by closures due to COVID-19 lockdowns, this is a very encouraging development. Unsatisfactory business developments at individual industrial companies in the US prevented an even more significant increase in the operating result. The situation in the United Kingdom also remains challenging due to the uncertainty surrounding Brexit. We do not, however, expect Brexit to have had any significant impact on the net assets, financial position, and results of operations of the Würth Group in 2020, nor do we expect it to have an impact on 2021.
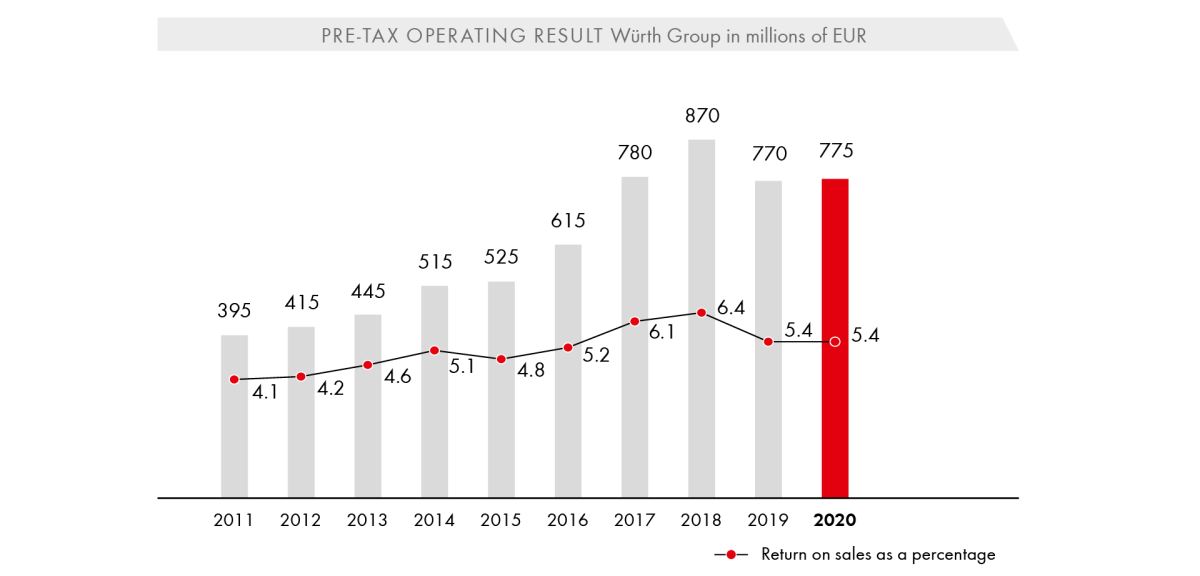
The ratio of cost of materials to sales was up slightly on the previous year at 50.4 percent (2019: 50.1 percent). A change in the sales mix is the main reason behind this increase. At EUR 110 million, other operating income is on a par with the previous year (2019: EUR 108 million).
At the end of December 2020, the Würth Group had a total of 79,139 employees. Person-to-person contact is the strength of our direct selling approach also, and particularly, in times of the COVID-19 pandemic. The sales force works closely with our efficient in-house departments. Due to temporary restrictions on face-to-face meetings, telephone-based consultancy sessions moved into the spotlight. In order to always be available to our customers and, in particular, to be able to return to the market at full capacity after the lockdowns, the Würth Group made a deliberate decision not to make any structural staff adjustments. The decrease of 193 employees in the sales force is minor and can be attributed exclusively to normal staff turnover.
The number of employees in our in-house departments rose by 1.4 percent, an increase of 646 employees. The ratio of cost of materials to sales was up slightly on the previous year at 26.7 percent (2019: 27.0 percent). This is attributable to the fact that government support measures were available in various countries during the COVID-19 pandemic, leading to a partial reduction in personnel expenses.
Amortization, depreciation, and impairment losses increased in the year-on-year comparison to EUR 779 million in 2020 (2019: EUR 721 million). This figure includes impairment losses on goodwill, customer bases, and property, plant and equipment amounting to EUR 84.3 million, which were mainly incurred in the US industrial companies and in the Würth Elektronik Group. Amortization and depreciation were up by 6.6 percent on the previous year.
Other operating expenses fell by 4.2 percent compared to the previous year. The ratio was down on the previous year at 12.4 percent (2019: 13.1 percent). This decrease was mainly due to savings in conferencing, travel, and other mobility expenses of around EUR 100 million. Travel restrictions imposed due to the COVID-19 pandemic led to a significant reduction in global mobility.
The tax rate increased in the 2020 fiscal year to 19.9 percent (2019: 18.8 percent). One of the main reasons behind this trend is that in the 2020 fiscal year, profits were increasingly generated in countries with higher tax rates, resulting in an increase in both the theoretical and the actual tax rate. For a detailed analysis, please refer to Section G. Notes on the consolidated income statement, [10] “Income taxes”, in the consolidated financial statements.
The Würth Group achieved a new sales record of EUR 14.4 billion in the last fiscal year in spite of the global pandemic. The operating result increased slightly thanks to stringent cost management. The Würth Group closed the fiscal year with an operating result of EUR 775 million. Net income for the year increased to EUR 604 million. Our gross profit, that is to say, sales minus the cost of goods sold, came under pressure due to developments on the global procurement markets. By contrast, staff turnover and sales per employee improved at an above-average rate compared with previous years. 2020 was an exceptional year. The outbreak of the first wave of COVID-19 in the Western world in March 2020 triggered a historic drop in sales of more than 20 percent for the Würth Group in April. The scenarios developed in response to this for 2020 as a whole envisaged a double-digit drop in sales. Against this background, the Central Managing Board is very satisfied with the sales growth of 1.0 percent. The operating result also outstripped expectations, taking into account the situation created by the pandemic last year.
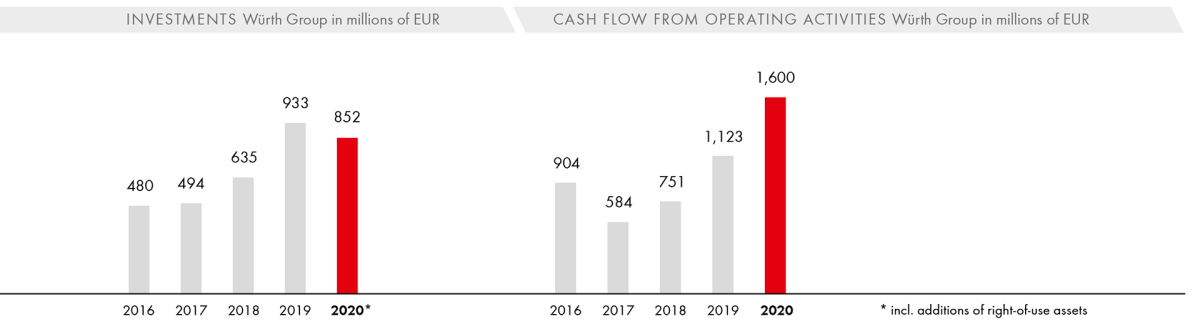
Capital expenditures and cash flow
Growth is inextricably linked to the self-image of the Würth Group. Growth by tapping into new markets and growth in existing markets require optimal overall conditions. One of the ways in which the Würth Group achieves such conditions is through sustainable investment. Over the past ten years, the Group has invested more than EUR 5.0 billion in intangible assets and in property, plant, and equipment. In 2020, global economic forecasts were revised downwards significantly from March onwards with the emergence of the COVID-19 pandemic, and economic development proved difficult to forecast for the Würth Group, too. Nevertheless, the Group continued to pursue planned investment projects, some of which had already been launched, and made investments (excluding right-of-use assets under IFRS 16) totaling EUR 473 million in the fiscal year under review (2019: EUR 705 million), corresponding to a decrease of 32.9 percent. The lower figure can be traced back to the fact that planned investment projects that were not directly related to an expansion of sales capacities or that were designed to optimize and expand services rendered by manufacturing companies were canceled, curtailed, or postponed to the following year.
All in all, investments in 2020 focused on the expansion of IT infrastructure and warehouse capacities for our distribution companies, as well as on production buildings and technical equipment and machinery for our manufacturing companies.
Kellner & Kunz AG, Austria, made the biggest investment in its history, expanding the central logistics facility in Wels. The trading company is an expert in the distribution of screws, tools, DIN and standard parts, as well as service systems in C-parts management, and has a product range encompassing around 120,000 top-quality products. The planning phase for the logistics expansion project began back in 2016, and the commissioning of the facility was finalized successfully at the end of 2020. This logistics expansion consists of an automated small parts warehouse comprising 200,000 bin bays, a high-bay warehouse with 15,400 pallet bays, and a functional logistics building consisting of a total of four levels, also featuring a shuttle system with 16,000 bays. The expansion project has added a total of 18,000 square meters of logistics space across all floors. The total amount invested came to around EUR 48.8 million.
Logistics capacities were also expanded at IVT GmbH & Co. KG in Rohr near Nuremberg. The first phase of construction was completed in the fall of 2020. A total of 25,000 square meters of land is available for construction, on which 500 additional storage bays were initially created in the form of a high-bay warehouse and a block-type warehouse spanning an area of 1,200 square meters. Thanks to the expanded logistics wing, it is now possible to deliver the new IVT stainless steel pipe system to customers nationwide within 24 hours. The second construction phase will involve the expansion of the total usable space for production and logistics to 7,000 square meters and is scheduled for completion by the end of 2024. The total amount invested in both construction phases comes to around EUR 15 million.
In addition to the Allied Companies, the Würth Line companies also made substantial investments in stepping up their sales activities. Würth Finland, for example, continued its successful pick-up shop strategy by building four new pick-up shops. The share of sales generated by pick-up shops in Finland is now almost 50 percent. The company now has a total of 189 locations where customers can cover their immediate needs. The total investment volume for expanding the pick-up shop network amounted to EUR 5.7 million at Würth Finland in 2020.
Despite the crisis, the Group is stepping up its innovation strategy as planned: In March 2019, the groundbreaking ceremony was held at the Künzelsau site for the construction of the Innovation Center, which is scheduled to open in 2022. The total amount invested comes to around EUR 70 million. Modern laboratories and workshops are being built on an area spanning 15,000 square meters. A climate chamber, the latest 3D printers, and seismic test stations for anchor technology offer a wide range of opportunities to strengthen and advance Würth’s in-house research in the long term.
In addition to investments in production and storage space, we have also, as in previous years, invested in our ORSY® storage management system, which offers our customers storage and provision options for various consumables and supplies in line with their needs.
In total, EUR 245 million, or 51.8 percent of the investment volume, was attributable to Germany, reflecting the continued paramount significance of the home market for the Würth Group.
Thanks to our efficient investment controlling processes using sophisticated recording and analysis tools, the Central Managing Board is always in a position to react quickly to changes in the overall environment. In 2020, for example, one crisis management measure was to set more stringent limits on the approval of capital expenditure amounts. The focus here was on maintaining the Würth Group’s stability and liquidity. There were no across-the-board investment cuts so as to ensure that necessary investments, for example, in the expansion of additional sales capacities, could continue to be made.
Thanks to all of the measures taken, we once again achieved our objective in 2020 of financing investments in intangible assets and property, plant, and equipment entirely from our operating cash flow, which amounted to EUR 1,600 million (2019: EUR 1,123 million), up by 42.5 percent on the previous year. The main reasons behind the strong growth, achieved based on unchanged earnings, were higher depreciation, amortization and impairment losses, increased risk provisions for inventories and receivables, moderate growth at financial service providers compared with the previous year, and salary components that had not yet been paid out.
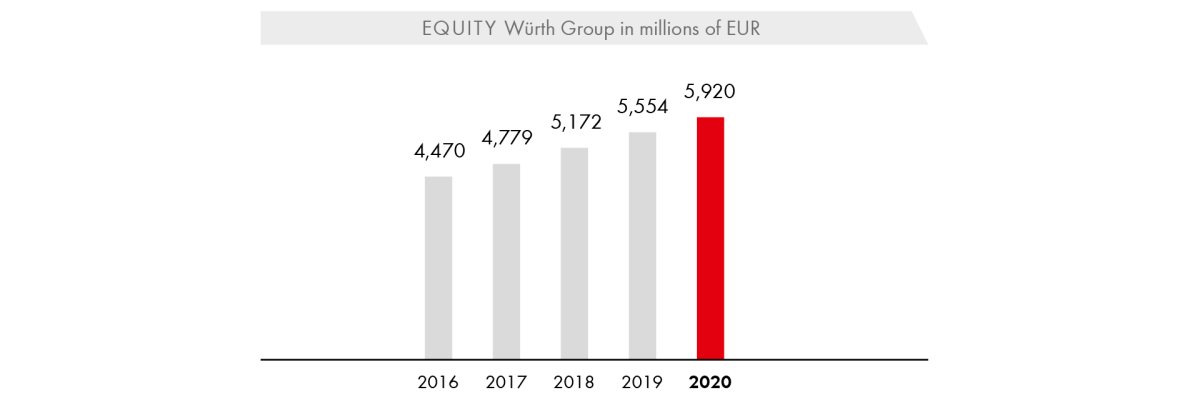
Purchasing
The COVID-19 pandemic had a significant impact on the procurement markets in 2020. This is confirmed if we take a look at the purchasing managers’ indices for the world’s three leading economic areas (eurozone, US, China), which serve as leading indicators of developments in these regions. Each of these indicators showed a significant drop between February and May 2020 before bouncing back in the months that followed. As a result, the purchasing managers’ index for the eurozone again exceeded the important 50-point expansion threshold from July 2020 onwards and stood at 55.2 points at the close of the year. This suggests that leading buyers in this economic area expect to see positive market developments in 2021. The purchasing managers’ index in the US was even more volatile. It bottomed out at 41.5 points in April and rose to 60.7 points by December 2020. The index for the People’s Republic of China was much more stable. After touching on a low of 40.3 points in February, the index recovered to 53.0 points by December.
The situation for the Würth Group’s buyers in 2020 was a very challenging one: On the one hand, production capacities were repeatedly unavailable in the course of the year due to regional measures to combat the pandemic. On the other, customer demand for a large number of products slumped significantly, especially at the peak of the COVID-19 pandemic in the first half of 2020. By contrast, demand for personal protective equipment products, such as face masks and disposable gloves, rose sharply. The production capacities available worldwide were far from sufficient. This development is ongoing in some cases and will also have a marked impact on the procurement markets in 2021.
Two effects came to light on the procurement markets in the second half of 2020. On the one hand, a special economic situation with above-average customer demand was observed following the lockdowns in the global sales markets in the first half of the year, inevitably resulting in longer delivery times and high levels of capacity utilization among suppliers. On the other, it was particularly noticeable in the second half of the year that regional decisions to step up the pandemic measures prompted a drop in production capacities worldwide. Accordingly, buyers were forced to juggle the conflicting priorities of a significant increase in customer demand and lower available production capacities on the supplier side.
The euro/dollar exchange rate was also heavily influenced by the pandemic in 2020. In addition, the US presidential elections in November 2020 failed to translate into any sustained increase in the value of the US dollar. While the dollar was trading at USD 1.123 per EUR at the beginning of 2020, it had climbed to as high as USD 1.224 by the end of the year. This exchange rate trend had a positive effect on the results of the importing purchasing companies.
By contrast, cargo rates for container handling at shipping ports in Asia rose significantly over the course of 2020. In the wake of the COVID-19 pandemic and the strict lockdowns imposed in Asia, shipping companies tightened up their freight capacities, meaning that the capacities available were completely booked up from the summer onwards. At the same time, demand for air freight from Asia increased enormously, which also meant longer delivery times for finished products.
The value management function launched in 2019 was established and expanded further in 2020. The aim is still to use value analysis approaches to strengthen product price transparency within the Purchasing function of the Würth Group so as to provide additional support to buyers in their negotiations with suppliers. This is designed to help counteract the price development expected for 2021. Further analysis projects were defined in the purchasing companies as a result.
Inventories and receivables
As a company with international operations, the Würth Group’s inventories and receivables are key balance sheet items that the company’s management is continually seeking to manage and optimize. Both balance sheet items allow for short-term controlling and optimization of liquidity and tied-up capital in the Group, something that proved crucial in the fiscal year under review.
The Würth Group’s inventories increased significantly during the first COVID-19 wave between March and May 2020. Due to the drastic drop in sales in April and May and the fact that orders placed earlier continued to arrive in the warehouses, inventories peaked at a value of EUR 2,385 million in May.
From the very start of the pandemic, inventory control measures were stepped up in close coordination with the established companies, the aim being to bring inventory development in line with the sales situation as quickly as possible. At the same time, the Würth Line’s Central Purchasing department pushed ahead with projects to streamline the range of products on offer in cooperation with Product Management in order to eliminate products with very low demand.
These activities resulted in an ongoing reduction in the Würth Group’s inventories in the months that followed. At the end of the year, the Group’s inventories came to EUR 2,222 million, EUR 163 million lower than the peak reached in May and as much as EUR 66 million lower than one year earlier (2019: EUR 2,288 million). Stock turnover, calculated on a 12-month basis, fell slightly from 4.7 times at the end of 2019 to 4.6 times at the end of 2020.
Alongside sales, logistics is a central element within the Würth Group. The rapid implementation of precautionary measures in logistics processes ensured that supply capability remained consistently high throughout the year. The service level in 2020 was 96.7 percent, meaning that 96 out of 100 items ordered were delivered to the customer the next day. This service allowed us to be a reliable partner for our customers even in an environment dominated by the pandemic.
COVID-19-related lockdowns lasting weeks in many sectors, worldwide border closures, and the associated disruption to supply chains, coupled with the shutdown of entire production plants in the spring and early summer of 2020, fueled fears of large-scale company insolvencies and associated massive losses caused by bad debt, or at least delayed incoming payments. The top priority was therefore to safeguard liquidity in the Würth Group. One of the ways in which we did this was by keeping a close eye on the development of receivables. In this situation, too, the Würth Group was able to rely on its established, sophisticated controlling systems, which allow the Group to take fast action in response to any undesirable developments that may emerge. Thanks to extremely efficient interaction between sales and receivables management, and despite slightly rising sales, the Group actually succeeded in reducing its trade receivables by 1.7 percent to EUR 1,942 million (2019: EUR 1,975 million). This very encouraging development is also reflected in the level of receivables in relation to sales. At 53.0 days, the corresponding key figure, collection days (based on a 12-month calculation), was significantly lower than the figure for 2019 (54.8 days). An excellent result was achieved in Germany, in particular, with 40.0 days (2019: 42.2 days).
We will continue to optimize accounts receivable by means of effective cooperation between sales and accounts receivable management, as well as by refining our analyses. We see the payment patterns of debtors as critical in Southern Europe, China, the Middle East, and India, as they can slow growth.
The percentage of bad debts and the expenses from additions to value adjustments related to sales increased slightly to 0.6 percent (2019: 0.4 percent).
Financing
The equity of the Würth Group climbed by 6.6 percent to EUR 5,920 million in the past year, an increase of EUR 366 million. This increase allowed the company to keep its equity ratio more or less stable at a level of 43.8 percent, which is high for a trading company (2019: 44.0 percent). For years, a good level of equity capitalization has been the basis for consistently high levels of financial stability and the solid financing of our group of companies, strengthening customers’ and suppliers’ trust in the Würth Group. This is due to the typical family business approach of reinvesting a large portion of profits in the company. The high level of equity financing allows the company to be relatively independent of external capital providers, which is a must particularly in times of crisis.
Total assets rose by EUR 851 million to EUR 13,478 million (2019: EUR 12,627 million). The increase of 6.7 percent is due primarily to the increase in cash and cash equivalents. This is thanks to the issue of a new bond and a stringent spending policy. As a result, net debt fell significantly to EUR 601 million as against EUR 1,356 million in 2019.
Financial service activities also contributed to the growth in total assets, albeit not to the same extent as in the previous year. Refinancing in the banking sector was mainly achieved through financial intermediaries and refinancing programs launched by the European Central Bank, while refinancing in the leasing segment was achieved mainly through the ABCP (Asset Backed Commercial Paper) program created especially for this purpose, a global loan program launched by the German state-owned development bank KfW, as well as through non-recourse financing and internal funds.
The Würth Group has undergone an annual rating process for 25 years now. The leading rating agency Standard & Poor’s once again confirmed the Würth Group’s “A /outlook stable” rating in 2020. This rating reflects the confidence that business and the financial KPIs will continue to develop successfully, even in the environment created by the pandemic. The opportunities and outlook for the Würth Group are viewed in a positive light. Our long history of good ratings not only documents the positive credit rating; at the same time, it is proof of the continuous and successful development of our corporate group and the stability of our business model.
Last spring, the Würth Group took advantage of the attractive conditions on the capital markets to raise long-term funds and successfully placed a EUR 750 million bond on the market via its finance company Würth Finance International B.V. on 11 May 2020. This issue, the largest to date, is an important component of the Würth Group’s capital market-oriented financing strategy. The bond, which has a term of 7.5 years, has a coupon of 0.75 percent p.a. and is secured by an unconditional, irrevocable guarantee provided by Adolf Würth GmbH & Co. KG. It was used, among other things, to repay a EUR 500 million bond that matured in May 2020. At the end of the 2020 fiscal year, the Würth Group had three bonds issued on the capital market and one US private placement. All covenants in this context have been observed. In 2022, 2025, and 2027, bonds worth EUR 500 million and EUR 750 million will reach maturity, while the US private placement of USD 200 million is set to reach maturity in 2021. This means that the maturities are well spread out. For further details on the maturity profile and interest structure, please refer to [27] “Financial liabilities” in Section H. Notes on the consolidated statement of financial position, in the consolidated financial statements.
The Würth Group has sufficient liquidity reserves. As of 31 December 2020, cash and cash equivalents came to EUR 1,386 million (2019: EUR 477 million). In addition, the Group has a fixed undrawn credit line of EUR 400 million provided by a syndicate of banks until July 2023.
In addition to successful sales and outstanding logistics, new products and innovations as a service to our customers are crucial when it comes to securing the competitive standing of the Würth Group.
In the 2020 fiscal year, for example, Adolf Würth GmbH & Co. KG generated one-fifth of its sales from products that are less than three years old. Given the breadth and size of the range that Würth offers its customers, this number is very high. The issue is also a priority throughout the Group: At present, the Group has 781 active patents, 8 utility models, 934 registered designs, and 7,749 active brands.
Developments within the Würth Line
Adolf Würth GmbH & Co. KG
ASSY®4: enhanced special screw for top performance in structural timber engineering
With the ASSY®4 innovation screw, Würth has introduced a new generation of the tried-and-tested wood construction screw that is widely used in timber construction. In cooperation with the development department of Adolf Würth GmbH & Co. KG, the production team at SWG Schraubenwerk Gaisbach was able to make its contribution to the successful series production of the product with its manufacturing expertise. The 1,400 different dimensions for the core range alone are testimony to the scale of this project. The most important further developments include a gently expanding screw tip with a linear rise in the counter thread to reduce splitting, a newly developed thread that pulls boards together much better, optimized milling pockets for fast and clean driving in of the screw, and the completely new RW screw drive. The main feature of the new RW drive is the extended, reinforced, and beveled bit wings, which allow the bit to penetrate particularly deeply into the screw head of the ASSY®4. This allows for a better transmission of forces. The RW drive also creates a clamping effect between the screw and the bit. This means that the screws stay reliably attached to the bit even without magnetic force. The improved transmission of forces also allows the required bit sizes to be reduced to a total of four, meaning fewer bit changes when working with different screw dimensions. Compared to the predecessor model, the screw features an increased number of milling pockets for smaller diameter screws. Especially in cases involving timber materials with a brittle melamine coating, this prevents unwanted fraying and, as a result, visible surface flaws around the countersunk screw head. In screws with metal fittings, the milling pockets have a braking effect that improves the friction-fit with the fittings.
HSCo Multi Performance combination screw tap:
pre-drilling, thread cutting, and deburring—all without changing tools
The new HSCo Multi Performance combination screw tap combines all steps involved in making through-holes with internal threads in just one operation without having to change tools. The drilling depth has been increased to twice the drill diameter, twice that of conventional combination screw taps. In addition, it is suitable for almost all common materials—from conventional structural steels and casting materials to stainless steels and non-ferrous metals. This allows for more versatile and efficient applications. The tool can be used on cordless drills as well as on hand-held, pillar, and upright drills. A polygon shaft ensures safe power transmission from the machine to the combination tool.
WIT concrete screw anchor system:
install anchors quickly and securely in concrete like never before
The combination of the W-BS concrete screw and the two-component WIT-BS concrete screw mortar creates the WIT concrete screw anchor system, which allows for unprecedented tensile loads in concrete. The anchor system, which has been approved by building regulatory authorities, is particularly suitable for the fast and secure fastening of heavy load-bearing elements such as steel and timber structures, facades, railings, or even pipe and cable shafts. Unlike conventional chemical anchors, the WIT concrete screw anchor system offers a major advantage in that it can bear a partial load immediately after being screwed in, without having to wait for the mortar to dry completely. Once the mortar is dry, the load-bearing capacity of the system increases significantly. This can be illustrated using the example of a size-10 concrete screw and an effective anchorage depth of 110 millimeters, for which the load-bearing capacity in cracked concrete increases from 9.6 kN to 19.8 kN. In addition, variable anchoring depths and options to select load-bearing capacities also allow particularly cost-effective anchoring solutions to be implemented.
Driverless transport systems in the new central logistics hub
The central logistics hub in the Gewerbepark Hohenlohe industrial park has a surface area of around 50,000 square meters. In the wide-aisle warehouse, nine automated guided vehicles (AGVs) are used to cover the long transportation routes. They support employees in their processes and take work off their hands so that they can focus on picking and packaging. The AGVs automatically transport the picking trolleys, loaded with goods, from one picking station to the next. Employees place the finished picked orders on the picking trolleys and the AGVs transport them from the picking area to the packaging area. Operating on a two-shift schedule, the AGVs currently make around 700 journeys from the pick-up station to the destination station, covering a distance of approximately 64 km. The AGVs first have to be integrated into the logistics processes so that they can navigate independently through the warehouse. The system and the capacity of the AGVs are optimized on an ongoing basis in order to achieve continual increases in productivity.
Cradle to Cradle Certified™ certification for packaging made from 100 percent recycled plastic waste
Würth and packaging manufacturer rose plastic have launched a pilot project for recyclable packaging solutions. They developed packaging made from 100 percent post-consumer recyclate (PCR), that is, plastic waste from the dual system that is collected throughout Germany. It is separated from other materials, split into size categories, sorted by type of plastic, ground, washed, melted, filtered, and re-granulated to be turned into new resources. The labels are also made of 100 percent recycled plastic and are affixed using ecologically friendly adhesives. This allowed the new packaging to secure Cradle to Cradle™ certification. The first step will involve using the recycled packaging for products in the cutting tools sector. The move to the new packaging will save around 45 metric tons of new plastic a year and will reduce CO2 emissions by 77 percent.
Würth Italy
HoloMaintenance Link
The HoloMaintenance Link platform allows tradespeople to manage consultation, support, and maintenance requests interactively and respond to them remotely by leveraging the potential of augmented and mixed reality. The customer clicks on a link received via SMS, e-mail, or chat and starts a video call from a mobile device. The tradesperson can then give the customer step-by-step instructions remotely to guide them through the necessary activities using augmented and mixed reality models, 3D animations, and technical documentation. At the end of the support call, HoloMaintenance Link automatically generates a ticket documenting the call history. By allowing for quick, solution-focused assignments, the platform streamlines the workflow and reduces the tradesperson’s costs. HoloMaintenance Link is a joint project launched by Würth Italy, Microsoft Italia, and Hevolus Innovation, Microsoft’s international mixed reality partner and Würth Italy’s technology partner for open innovation initiatives.
Würth Automatic Store
The Würth Automatic Store allows customers in Italy to buy products using a self-service function—24 hours a day, seven days a week. The fully automated store contains more than 2,000 items that can be selected via touchscreen and are always in stock. Likewise, orders placed via the Würth App or on the website can be collected in a contactless process at any time. The store is flexible and can be transported from one location to another by truck as required. The store does not have to be staffed by employees and no costs are incurred for rent, electricity, and heating. The first prototype is located in Sommacampagna near Verona. More Automatic Stores across the country will follow.
Developments within the Allied Companies
The Allied Companies of the Würth Group also continued to invest in the development of products and services to offer their customers the best possible solutions in 2020.
Würth Elektronik eiSos: Horticulture LEDs
“Horticulture lighting” describes the use of light to optimize plant growth. Würth Elektronik eiSos performed research in this area and developed special LED lamps that it is making available to the greenhouse laboratory center at the Technical University of Munich for joint research so that they can contribute to our nutrition in the future. The Horticulture LEDs make it possible to produce food all year round irrespective of the weather conditions (vertical farming). The wavelengths selected for plant cultivation promote photosynthesis and optimize plant development. In trials, tomatoes exposed to Horticulture LEDs produced up to 14 percent more flowers in winter than those exposed to other plant cultivation lamps. At the same time, energy consumption was reduced by up to 70 percent. As each plant requires different lighting conditions to grow and thrive, individual light recipes are developed. To allow every developer to replicate the experiments themselves, the Lighting Development Kit was developed as part of the project. Among other things, it features the Magl³C Multi Color LED Driver power module and the Horticulture LEDs, while it is also being used for basic research into new horticulture lamps and is accelerating their development considerably. In addition, developers have the option of using the WEilluminate app, developed by Würth itself, to control the individual LED strands. This underscores eiSos’ commitment to green electronics—the use and application of highly efficient energy-saving components and solutions to conserve resources and make innovative solutions available to the market for reducing CO2 emissions and waste.
Würth Elektronik CBT: Project CHARM—robust electronics for harsh industrial environments
Digitalization is the most important prerequisite for strengthening the competitive standing of Europe’s manufacturing industries. The options for the implementation and use of digitalization are, however, limited by the harsh environmental conditions associated with manufacturing processes, for example. High temperatures and humidity, as are common in paper production, dust formation, and strong vibrations during mining operations often lead to the premature failure of the electronics involved. The objective of the CHARM (Challenging Environments Tolerant Smart Systems for IoT and AI) research project is to develop technologies that are capable of tolerating harsh industrial environments. As part of the project, Würth Elektronik CBT is developing assembly and interconnection technology for robust assemblies at the PCB level. These assemblies are equipped with integrated sensors and flexible film and sensor systems. All components have to be designed to withstand the combination of severe thermal, mechanical, and chemical stresses. To ensure this, special protective housings for electronic components are being used that go beyond the current state of technological progress.
WTN: pioneering 3D metal printing technology
With the help of 3D metal printing, also known as “additive manufacturing,” complex components—which stand out due to their lower weight and greater functional scope—can be produced within a very short period of time. Taking the example of a mounting fixture manufactured by WTN from stainless steel (1.4404) and plastic, it was possible to save around 2.5 kg of weight per fixture by optimizing the topologies (support structures). Since the fixture is folded open and closed about 700 times a day, around 1.75 tons less weight has to be moved per day.
TUNAP: airco well sensor
Germs and bacteria: TUNAP has responded to what is currently an increasingly topical issue and now offers sustainable improvements for vehicle interiors. The airco well air conditioning cleaning system removes germs, bacteria, and mold at the source—on the evaporator and in the pollen filter box. Thanks to the cleaning system, germs are flushed out by a high-pressure jet and all the affected components are thoroughly cleaned. Now, a sensor is being launched to allow for the rapid measurement of bacteria and pollutant levels in vehicle air conditioning systems. The airco well sensor checks the air from the air conditioning system for pollutants and bacteria and lets you know when the air conditioner needs to be cleaned. The improved air quality is then analyzed and documented.
Arnold Umformtechnik: Flowform® Plus
Working in cooperation with various vehicle manufacturers, Arnold Umformtechnik was able to successfully enhance its flowhole-forming screw and make it ready for series production. Thanks to innovative heat treatment in conjunction with adapted material, the potential areas of application for the new Flowform® Plus have been extended significantly. One significant advantage is the product’s use in joining sheet steels without pre-drilled holes up to 1,000 MPa. At the same time, the fastener is now smaller, thus saving weight and installation space. The Flowform® Plus screw is being used at Audi for the production of the company’s high-voltage battery, among other things.
Kisling Group: UV/anaerobic dual-curing joining compound ergo. 2453 for electromobility
One of Kisling’s latest developments is the UV/anaerobic-curing adhesive ergo. 2453. It enables hand-fixed bonds in seconds, without the addition of heat or activators to speed up the process. The advantage is that the components can be processed further during production. For this purpose, the adhesive gap is irradiated with UV light for about five seconds and the adhesive is cured to a depth of ∼ 2 mm. The UV/anaerobic-curing adhesive ergo. 2453 remains temperature-resistant at temperatures as high as 180 degrees Celsius. This makes it perfect for adhering permanent magnets in motor housings or pocket magnets in stator or rotor packages as used in high-performance electric engines for electromobility.
FELO: Series 450 hammer cap screwdriver product innovation
Hammer cap screwdrivers are used when you need to apply particular force, for example, when loosening stuck screws in automotive repair work, machinery, or in construction. Most current models, however, return the vibrations and significant forces of the impact directly to the screwdriver users. The ergonomics experts at the Hesse-based manufacturer FELO have developed a solution. The patented ERGONIC® handle makes it possible to transmit considerable forces while protecting the joints at the same time. It is already a component of a large number of FELO products.
As a globally active company, the Würth Group is constantly exposed to risks, but also makes systematic use of opportunities that present themselves. Opportunities and risks can arise both as a result of our own actions or failure to act, and as a result of external factors. The risk and opportunities policy of the Würth Group is aimed at meeting the company’s medium-term financial objectives and at ensuring the sustainable, long-term growth of the Group. In order to ensure this, the Würth Group has a system that identifies entrepreneurial opportunities and risks, assesses them using a standardized system, weighs them against each other, and communicates them. Our conscious and systematic approach to addressing opportunities and risks is inextricably linked to our entrepreneurial activities.
How the risk management system works
The Würth Group has a three-tier risk management system (RMS), comprising the cyclical monitoring system of the Auditing Department, the Group Controlling Department, and the early warning system. The Central Managing Board of the Würth Group holds overall responsibility for the Group-wide risk management process and defines the principles of our risk policy and strategy. The management of each company within the Group is responsible for installing a functioning and efficient RMS for themselves. They are supported by the risk manager, who reports directly to the Central Managing Board of the Würth Group and coordinates the risk management process at the Group level. The risk manager remains in close contact with the risk controller of the Advisory Board, who reports directly to the Chairwoman of the Advisory Board.
How the internal control system for financial reporting works
The aim of the internal control system for financial reporting is to ensure that all business transactions are completely recorded and correctly evaluated in line with the financial reporting requirements.
The Würth Information System is an integral component of the internal control and risk management system of the Würth Group. With the help of this reporting system, all key performance indicators required to steer the Würth Group are presented in a timely manner and are available for further evaluation by the Central Managing Board and Executive Board, based on standardized monthly reporting.
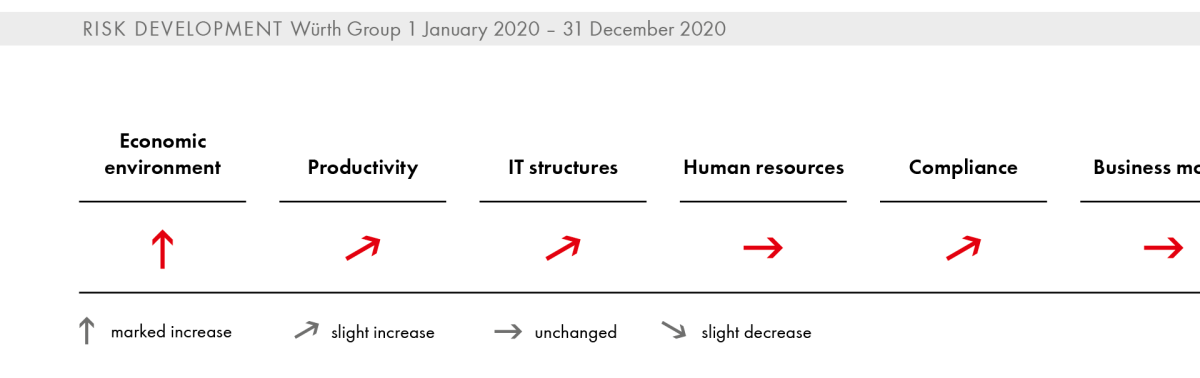
System-based control mechanisms such as validation and cross-checks optimize the quality of the information as a basis for decision-making. A Group-wide online record of the financial statements of the Group entities is not only efficient, it also avoids carry-over errors, safeguards the uniform provision of information, and includes numerous plausibility checks, without which the information cannot be forwarded. This platform also ensures that financial reporting changes are implemented in a uniform manner across the Group. Data is protected from changes by using check digits and a system of IT access rights. Standard software is used for consolidation. Changes in the system settings are logged centrally. The monthly and annual financial statements of Group companies are subject to regular automated assessment mechanisms, as are the consolidated financial statements. Moreover, Würth’s Policy and Procedure (PAP) Manual contains internal procedural instructions. Internal publications and training include detailed rules on financial reporting. Compliance with these rules is regularly reviewed by the Auditing Department. External specialists are consulted to clarify the implications of legal and tax issues on accounting. External actuaries calculate pension obligations and similar obligations. Regular training courses for those in charge of finance departments, which were offered online in the year under review, also ensure that all employees involved in the financial reporting process are up to date on the latest legislation and information of relevance to them.
The opportunity and risk management process is updated within the Würth Group on an ongoing basis and adapted to changes in the Group or in its economic and legal environment. In the 2020 fiscal year, the establishment of the IT-based risk reporting system was continued at further Group companies and the Executive Board and heads of the Group’s administrative departments were actively involved in the risk management process.
Risks
The Central Managing Board identifies, analyzes, and assesses the Group’s risks at a dedicated annual workshop. This workshop determines focus risks that could pose a threat to the net assets, financial position, and results of operations of individual entities or the Würth Group as a whole in the short, medium, or long term. Furthermore, with the support of the risk manager, all major Group entities carried out a risk inventory and recorded and assessed focus risks and other risks in the reporting system. The processes already in place were enhanced in 2020, undergoing improvements and adjustments in line with changing internal and external requirements.
Major risks that can be insured on an economically reasonable scale are covered by Group insurance programs for all Group entities whenever possible. In the area of credit insurance, further local insurance policies taken out by individual Würth companies were incorporated into existing master agreements with various credit insurers. This allowed us to expand and standardize our insurance coverage and achieve economies of scale. In addition, receivables from customers are monitored by an extensive receivable management system, also at the Group level. Individual financial service providers are associated with a heightened risk of default due to the nature of the business model. We counter this risk through a strict credit verification procedure and appropriate insurance for our investments. Collection days decreased further in 2020 and are at a low level. This highlights that our risk in this area is currently relatively low and that the existing processes and systems are effective. We believe that other risks in Germany lie in the applicable insolvency challenge rights, which grant insolvency administrators extensive opportunities for reimbursement if we have supported our customers with generous payment terms in the past. This risk has not been reduced to any considerable degree even after the reform of the insolvency challenge rights. Nevertheless, we have an insurance policy in place to cover such reimbursement claims so as to protect all German companies against unforeseeable risks in this area. Overall insurance coverage is managed centrally.
The Central Managing Board has identified potential risks that could have a negative impact on the net assets, financial position, and results of operations of the company in the following risk areas, sorted by descending order of relevance:
Economic environment
Through our global purchasing and sales activities, we have a high natural diversification of risk and, as a result, a reduced dependency on negative economic developments in individual countries, even though more than 80 percent of our sales are generated in Europe. In addition, the diversity in our business units makes us independent of specific industries and markets, which was confirmed in particular during the various phases of the COVID-19 pandemic in 2020. Due to the large proportion of sales generated in Europe, we are affected to a particular degree by economic fluctuations in the eurozone. In addition to the risks associated with the ongoing COVID-19 pandemic, we believe that risks lie in political developments in Eastern European markets and in Turkey, as well as in the trade barriers between China, the US, and Europe. We believe that immigration to Europe not only poses economic and social challenges, but also still presents opportunities for the labor market and on the demand side for our customers and, as a result, for the Würth Group. We believe that the rise of right-wing populism and isolated plans to reverse globalization trends within individual countries give cause for concern, although we have not identified any immediate threat to our business objectives for 2021 as of yet.
Most of the financial risks of the Würth Group are measured, monitored, and controlled centrally by Würth Finance International B.V. With liquid assets of EUR 1,386 million and a committed, unused credit line of EUR 400 million running until July 2023, the Würth Group has sufficient liquidity reserves to meet its payment obligations at all times. Thanks to its “A” rating from Standard & Poor’s, the Würth Group has very good access to the public and private capital markets to procure further financial resources. Any risks arising from derivative financial instruments are accounted for. At the time this management report was prepared, there was no indication of any specific counterparty risks, which are automatically monitored on a daily basis. A CSA (Credit Support Annex) is in place with the main counterparties to derivatives, thus further reducing counterparty risk. Cluster risks are avoided by means of internal deposit limits for individual banks. For a description of derivatives and associated risks, please refer to the notes on the consolidated financial statements under I. Other notes, [4] “Financial instruments.”
Productivity
Every year, the Würth Group invests an amount running into the mid triple-digit million range to secure its planned sales growth and further expand its market shares in individual regions and market areas. As a result, any deviations from the planned route require a timely response, with targeted measures to counteract such developments. These measures include management using key productivity figures, the in-depth analysis of loss-making companies, a detailed, multi-stage investment controlling process, scenario calculations, and a firm focus on achieving the targeted operating results. As a general rule, we take care to ensure that sales and gross profit grow faster than personnel expenses—in line with one of the Würth Group’s fundamental principles: “Growth without profit is fatal.”
IT structures
As a company with a very decentralized structure, the Würth Group had previously used various different IT systems, software components, platforms, and process control systems. This structure, which allows for a high degree of flexibility at the local level, increasingly emerged as a disadvantage in light of changing business models, digitalization, disruption, and the ever growing requirements as far as cyber security is concerned. In line with our corporate philosophy, which allows for a significantly higher degree of centralization in IT, the Würth Group’s IT organization, which is represented by the IT companies, has established a global ecosystem that can offer platform-based IT solutions to suit the business models of companies in the Würth Group.
IT standardization
The central management of the IT companies with what is now a standardized product portfolio in the form of the IT ecosystem allows us to reflect the international multiplication strategy in our IT systems, too. Further standardization is achieved in line with a roll-out plan that sets out the launch dates at the individual companies, with numerous roll-out teams working on the introduction of the relevant components in parallel to provide a broad multiplication platform for the individual applications, processes, and functions.
The roll-outs will make existing processes more uniform, more efficient, more transparent, and faster. This will allow the individual companies to respond to the rising demand for individual ordering and delivery services among our customers. Efficiency gains can still be achieved, as the standardization of the IT structures through central development will result in economies of scale and better protection against attackers.
The Würth Group’s IT service has proven its ability to perform in line with high standards. The uniform system platforms will allow further developments to be made available to all companies working on the platform in question within a very short period of time.
IT security
Risks arising from global integration are minimized by applying high security standards to make sure that the company is well equipped to deal with the constant threat of cyber attacks. IT system standards are reviewed by means of IT checks at the Group entities in accordance with a plan coordinated with the Group Auditing Department. This allows us to analyze and monitor the potential threat that cyber risks pose on a regular basis. We combat the resulting risks by taking organizational and technical measures and also by transferring risks that can be insured to external risk carriers, such as insurers. All measures relating to data security and IT risks are supported and implemented by our IT security officers in the national companies. In addition, Würth has introduced an IT Compliance Code of Conduct and appointed an IT Compliance Officer. The network of IT security officers in the companies is used to take measures to ward off security risks quickly at the level of the Group companies and establish those measures in an effort to continuously improve IT security. Where IT systems have been centralized, far-reaching and multi-level security procedures can also be implemented, both at the physical level, for example, in the data centers, and at the logistical level, for example, in the various system and program components.
Raising employee awareness for information security risks is a top priority. Various media such as e-learning sessions, poster campaigns, information letters, and specialist presentations are used to show employees the behaviors and habits they need to adopt in order to reduce the risk of security incidents. Targeted measures taken at individual companies, for example, using password phishing, are used to check the success of the measures and, if necessary, to take subsequent action.
Human resources
Staff turnover, particularly among our sales force employees, remains a key focus. This is documented and analyzed across all hierarchy levels for every entity within the Würth Group. Regular employee surveys conducted by independent institutions and the monthly monitoring of staff turnover are key tools that allow us to identify unfavorable developments, analyze their impact on recruitment processes, customer loyalty, and training programs, and combat these effects using targeted measures. The overall staff turnover rate of the Würth Group remains at a very encouraging low level at well below the 15-percent mark. The lack of specialist employees to work as members of the in-house staff or the sales force is another challenge for HR management. For many companies, it is becoming increasingly difficult to find skilled trainees. This prompted us to further expand the activities of Würth Business Academy for the in-house staff and the sales force when it comes to training management employees and new management talent. Up-and-coming management talents partake in development courses to prepare them for various levels of management within the Würth Group via the Würth Potential, High Potential, and Top Potential training programs. These programs give employees targeted training that is tailored to suit their own individual ambitions and skills in order to prepare them for further management duties within the Group. In addition to management seminars, international specialist seminars on issues such as product management, procurement, logistics, and financial topics are organized and coordinated by Würth Business Academy in order to support the specialist functions with relevant further training. In order to make further training available across the globe, the company had already set up its Learning Campus back in 2017 to enable digital learning. All employees can complete e-learning courses via the Learning Campus. Together with the specialist departments, targeted activities were launched to digitize knowledge about global standards so as to make it available across the globe.
In order to ensure that the process involved in providing all central functions of the Würth Group with up-and-coming management talent is structured and targeted, two processes are in place at larger companies: The Management Assessment Process (MAP) is the qualitative tool used for the objective and standardized evaluation of executives. The talent management system is used to identify whether there is a sufficient number of qualified successors for functions that are relevant to the success of the Würth Group companies and, if not, by when these successors need to be available. Up-and-coming management talent is included in this system as well in order to ensure a structured and transparent development process. There is also a succession and contingency plan in place for managing directors, which ensures that succession arrangements that can be planned are made in good time.
Würth Business Academy North America (in Chicago) was established in October 2017 in order to provide the decentralized local companies with even better support with regard to HR development and talent management. Since January 2020, Würth Business Academy Asia-Pacific (in Shanghai) has been supporting talent development in the Asia-Pacific region.
Compliance risks
National and international transactions involving goods, services, payments, capital, technology, software, and other types of intellectual property are subject to numerous regulations and limitations that also have to be observed by the companies in the Würth Group. There is no question that we aim to comply with all regulations and administrative requirements for our business, both nationally and internationally. This applies when dealing with our customers and suppliers, employees, competitors, other business partners, and public authorities. Due to increasing legal complexity, we have in-house experts and consult renowned external consultants on a case-by-case basis. Particularly in China and emerging markets such as Brazil, complex, inconsistent, and constantly changing legal principles pose a challenge and also create risks that are difficult to assess and will persist in the long term due to the possibility of retroactive effects.
Value-oriented corporate culture
Mutual trust, predictability, honesty, and straightforwardness both internally and externally are fundamental principles that are deeply ingrained in Würth’s corporate culture. Our commitment to these values can be found as far back as the corporate philosophy penned by Reinhold Würth back in the 1970s. This does not just entail adhering to all applicable laws and in-house regulations, but also means ensuring that employees maintain the proper mindset, which forms a key component of the sustainable corporate success of the Würth Group. Extensive internal guidelines known as the “PAP” (Policy and Procedure Manual) operationalize these fundamental principles in the form of descriptions of the structure and process organization, in addition to setting out specific rules and codes of conduct.
Compliance organization
With regard to the mounting requirements that compliance organizations have to meet at both the national and international level, the Central Managing Board made the decision in 2015, with the consent of the Advisory Board and the Supervisory Board of the Würth Group’s Family Trusts, to combine and restructure the existing compliance components to form a Group-wide compliance management system and considerably strengthen the compliance organization. In addition to the role of Chief Compliance Officer and Group Compliance Officer, compliance officers were appointed at the level of the units, and additional compliance officers were appointed within the largest individual companies in the Würth Group during the 2016 fiscal year. The responsibilities and structures for product, tax, and IT compliance that are already in place across the Group will remain in force, but the individuals responsible also report to the Chief Compliance Officer of the Würth Group. The Compliance Board provides advice on compliance incidents as and when required and makes recommendations regarding any measures that need to be taken. The Compliance Board is also responsible for the further development of the compliance organization and reports to the Central Managing Board and the Advisory Board of the Würth Group in all compliance matters. One particular focus in the 2020 fiscal year was the further training of compliance officers at the company level.
Compliance regulations revised and supplemented
In addition to these structural changes, the internal guidelines on matters relating to compliance were also revised and supplemented. The fundamental features of the corporate philosophy were summarized once again in a Code of Compliance and supplemented with regard to compliance with international standards. In order to anchor the compliance organization within the Group in the long term, Group-wide training sessions on the compliance organization and on compliance issues have been conducted since the 2016 fiscal year. Training sessions initially focus on “Dealing with gifts and invitations,” “Antitrust law and price fixing,” “Company secrets,” “Data protection,” “European General Data Protection Regulation,” and “Export control.” Due to increasing information security risks, further training measures were established in the 2020 fiscal year.
Group-wide reporting system
The Group-wide reporting system means that not only employees but also customers, suppliers, and other individuals will be able to report any suspected compliance breaches directly to the Würth Group’s Compliance Office. The use of a technical system made available by an external service provider means that reports can be submitted completely anonymously.
Prerequisite for sustainable corporate success
The compliance organization is supported by the firm conviction of the Central Managing Board, the Würth family, the Supervisory Board of the Würth Group’s Family Trusts, and the Advisory Board that a living and breathing compliance culture will play a key role in ensuring the further sustainable success of the Würth Group. At the same time, the management teams of the Group companies can proactively live up to their responsibilities with regard to the mounting national and international demands that compliance organizations have to meet.
Business model
The business model of direct selling still offers considerable opportunities for the Würth Group in that it places us very close to the market and ensures customer loyalty. Nevertheless, customer ordering behavior has changed considerably in recent years. Digitalization offers a whole host of opportunities for working directly with suppliers. The relative ease with which businesses can establish Internet-based business models is resulting in growing competitive pressure. Our business model has to adapt to reflect this development. We want direct sales to continue to play a key role but also want issues such as logistics, services, and a broad product range to open up market opportunities. The sales representatives of today are no longer just salespeople, but rather managers of the various customer contact points: the sales force, the pick-up shops, and the Internet. We refer to this as a multi-channel sales model in which e-business serves as a practical complement to the traditional sales methods in a manner that is tailored to suit our customers’ procurement organization. In 2020, the COVID-19 crisis and the resulting change in our customers’ purchasing behavior led to an above-average increase in e-business sales, as our systemic importance gave us the green light to deliver and our delivery capacity was unrestricted. This development shows that we are on the right track with the services that we are offering with our customers’ needs in mind, and that our strategy of multi-channel sales is bearing fruit.
Opportunities
The opportunities set out below could have a positive impact on our net assets, financial position, and operating result. The opportunities are also listed in decreasing order of relevance.
Decentralized structure
Würth’s decentralized structure is a great advantage for the Group, especially in light of the fact that the individual countries in which we operate display such variation in their economic development. We believe that this structure presents an opportunity for further sustainable growth. It allows for a quick local response to circumstances and changes in any given market environment, meaning that we can implement efficient measures. We will continue to push the development of the Würth Group while maintaining our decentralized structure. The term “decentralized” within this context not only refers to regional aspects, but also covers our large array of different business models. However, the fact that we pursue the principle of decentralization does not mean that we cannot standardize processes further where it makes sense to do so in order to make more efficient use of our resources.
Market penetration
Our share of the market is estimated at just five percent due to a low share of the market in most countries, with a few exceptions. What would appear to be a disadvantage actually signals major growth potential that we can tap into by further expanding our customer base and intensifying our customer relationships, for example, by continually enhancing intelligent distribution systems that offer real benefits to our customers.
Customer relations
Our 3.9 million customers form the basis for our business success. As a result, expanding and maintaining our customer relations are key components of our day-to-day work. We will continue to focus on comprehensive customer management at all Group companies. Around 300,000 customer contacts a day and a large number of long-standing relationships between our customers and our more than 33,000 sales representatives help us to exploit the existing customer potential to the greatest extent possible. Grouping our customers based on their individual needs is a key control mechanism for strategic management. Being close to our customers is our declared objective. The correlation between additional customers and sales growth, together with the service level, are important indicators of business success for us. Customer insolvencies are a manageable risk for the Würth Group. Due to our very extensive core range of over 125,000 products, the comparatively low average order values, and our broad customer base, we are well positioned to keep these risks at a minimum.
Quality
It is the express aim of the Würth Group to meet, or where possible exceed, the highest quality standards. For this reason, the guiding principle “Würth is quality—everywhere, every time” was anchored in the Würth Group’s quality management back in 2010 and consistently developed further in the years that followed. The brand promise made by this principle applies to all of our markets, and its implementation opens up important additional market opportunities. This is true both of customers in the professional trades and those in industry. For us, ensuring reliable compliance with standards, in addition to fulfilling product requirements and approval criteria, is a fundamental quality management task to enable us to be a dependable partner for our customers. This is important, but we do not consider it enough in and of itself: We strive to surpass customer expectations wherever possible with our services and inspire our customers in the process.
In the 2020 fiscal year, the Würth Group’s central quality team continued its activities. Despite restrictions due to the COVID-19 pandemic, training courses were held on management systems and product and process quality during the year under review and 156 participants received further training on a total of 282 training days. One specific area of training was how to conduct remote supplier audits.
Key components of the Würth quality promise include, first of all, the validation of new products by the quality department, for example, at Adolf Würth GmbH & Co. KG and Würth International AG, and, secondly, measures to safeguard the quality of delivery by conducting supplier training and systematic checks along the supply chain. The Würth Group now has over 28 active “Supplier Quality Engineers” (SQEs) as well as its own test laboratories/goods checkpoints spread across Europe, Asia, and the US with a total of over 160 employees. By the end of the reporting period, six test laboratories had been awarded ISO 17025 accreditation. Further investments were made in the expansion of the SAP-supported system WS1, to be used as a mandatory requirement throughout the Group, focusing on the advanced quality planning function and the verification of tests, and measures aimed at the further integration of Group laboratories and suppliers were stepped up.
Overall assessment
The risks for the Würth Group are limited by the established and functioning risk management system, even in the current COVID-19 pandemic. Existing risks are consistently monitored and assigned measures to ensure that they do not jeopardize the Würth Group’s continued prosperity. With the exception of the risks arising from the COVID-19 pandemic, which are still impossible to assess specifically—we refer to the information set out in the forecast report—we are currently not aware of any other such risks. The existing opportunities will enable us to continue growing profitably in 2021 and the years to come.
- Number of employees rises to 79,139
- Broad-based in-house employee development program
Workforce development
The number of employees in the Würth Group rose by 0.6 percent to 79,139 as of 31 December 2020 (2019: 78,686). In Germany, the Würth Group had 24,514 employees on its payroll (2019: 24,344), while Würth companies abroad reported 54,625 employees (2019: 54,342). There were 33,176 employees working as permanent sales representatives worldwide in the 2020 fiscal year (2019: 33,369).
HR strategy
The shortage of specialists and managers is having an impact in many countries and qualified employees are increasingly becoming a limiting factor for growth. It is therefore important to retain employees at the company and to offer a positive working environment with interesting development opportunities. The Würth Group, with its diverse business models and international orientation, has many possibilities in this respect. Various activities were launched to present these prospects in a transparent manner. A binding and structured process was launched for the large companies to identify potential risks when filling key positions, but also to identify where new career prospects are opening up. This information is condensed and analyzed with the top management team of the Würth Group at regular intervals, with agreements being made on the measures to be taken and talent pools being defined.
The location for training, HR, and talent development activities in North America has also brought us closer to our target groups, thus encouraging the internationalization of our operations with regard to HR. Since January 2020, an additional HR development site has been up and running in China for the entire Asia-Pacific region. This decentralized approach allows the programs to be adapted to better suit local requirements and allows for talent management on location to be focused and managed based on the specific needs.
Digitalization will lead to major changes and associated challenges with regard to human resources. As a result, working groups have been set up to look at individual HR processes and their digitalization. In the area of digital learning, the Learning Campus is a platform that has been open to all employees of the Würth Group since 2017.
Under the leadership of Würth Business Academy, international cooperation within the Group is being strengthened by a Group-wide HR network and a platform for best practice sharing. In addition, topics relevant to human resources are discussed, developed, and established in this network.
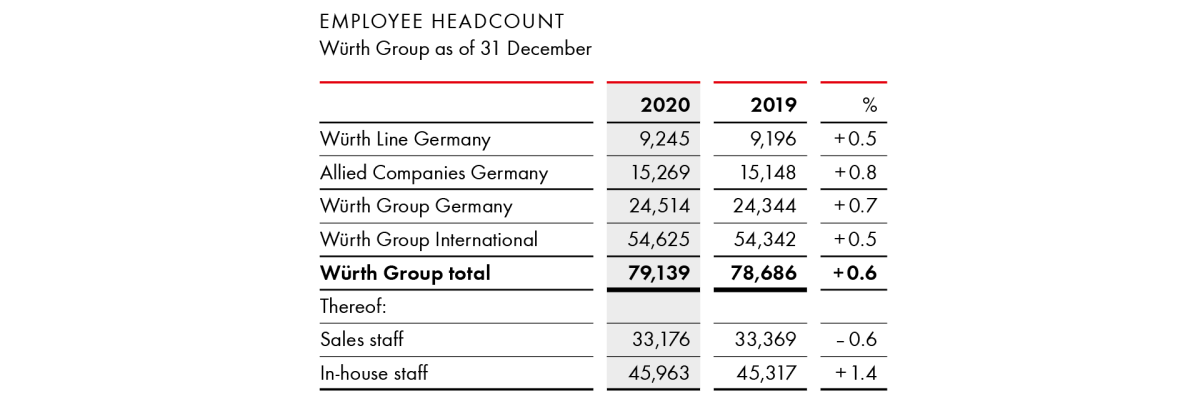
Employee training
The skills, competences, and qualifications of all employees, together with their motivation and enthusiasm, form the basis for a successful future. For this reason, personal development and further professional qualification are of particular relevance in order to meet the demands of the market. There are various phases in each employee’s working life: There are times at which personal issues such as self-worth or self-confidence play a key role and there are also times in which focus is placed on career advancement—be it in an employee’s career as a manager or in the various specialist departments. The programs available at Würth aim to offer everyone training that suits their individual skills and professional objectives.
As a family business, Würth is committed to long-term corporate development. This also applies when it comes to promoting the talents of the future. In Germany, where there is a long tradition of dual training concepts, Würth has been committed to providing people with extensive initial training for more than 60 years now. At the end of 2020, the Würth Group in Germany had 1,279 trainees for more than 50 different occupations. Young professionals can also study for bachelor’s degrees at the Baden-Württemberg Cooperative State University. The main focus in the German companies is on commercial, technical, and catering apprenticeships.
Akademie Würth offers a holistic further training concept for employees of the Würth Group as well as for customers and interested parties outside the Würth Group.
Akademie Würth offers a practice-oriented range of further training courses specifically for craft businesses in the form of technically oriented training courses. The targeted courses focus on specific topics such as fire safety, metalworking, fasteners, sealants and adhesives, motor vehicles, and occupational safety. This allows Würth to support its customers as a service provider, driver of innovation and mentor as well.
The concept is rounded off by consultancy services on all matters relating to quality and process management, organizational development, and business excellence. Companies within and outside the Würth Group alike are given support to help them meet the requirements that apply to them. This includes the implementation of overall statutory conditions, such as the creation and implementation of integrated management systems, or support with certification processes, as well as compliance with customer requirements. We also provide companies with support in areas such as strategy development and the implementation of change processes. Lean Management and Six Sigma have already been launched successfully at companies in various sectors. In order to ensure sustainability, the approach chosen tends to involve providing support with projects that will have an impact on the organization’s profit or loss.
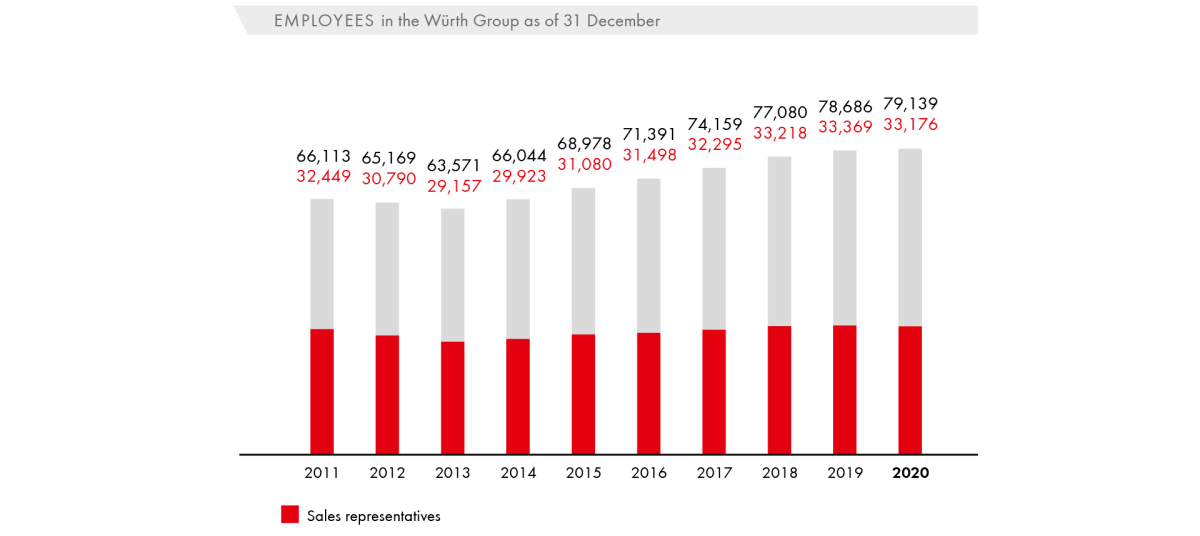
Degree programs for working professionals at Akademie Würth Business School, which are open both to employees of the Group and to interested individuals from outside the Group, allow people to study for academic degrees. The Bachelor of Business Administration in cooperation with the Distance Learning University Hamburg is a seven-semester program leading to a Bachelor of Arts (B.A.) degree. The bachelor's program in Industrial Engineering and Technical Sales in cooperation with SRH Distance Learning University takes six semesters, finishing with a Bachelor of Science (B.Sc.). In collaboration with the University of Louisville in Kentucky (USA), Würth also offers the internationally recognized master’s degree in Global Business. This one-year program, which is conducted in English, awards graduates a Master of Business Administration (MBA). As of this year, a Master of Science with a focus on Family Business can be obtained after completing the MBA course. The courses last six months and are offered in cooperation with Heilbronn University of Applied Sciences. The master’s program in Digital Management & Transformation confers a Master of Science (M.Sc.) in four semesters, also in cooperation with SRH Distance Learning University. Würth also offers a Doctor of Business Administration (DBA) as a three-year program in conjunction with Northumbria University, Newcastle. The DBA is a professional doctorate in business administration, equivalent to a PhD but with a clear focus on developing and improving professional practice.
Würth Business Academy (WBA) ensures holistic management training and the systematic development of up-and-coming talent. The aim is for management positions to be filled primarily from the company’s own ranks. WBA supports this process by offering suitable training programs for different stages in an employee’s development. Offering international technical and management qualifications, WBA ensures that quality standards are met in this area, too. WBA also supports management teams worldwide in succession planning as part of a structured process and makes its information available to the Central Managing Board and the executive bodies of the Würth Group as part of the risk assessment process.
Health management
In these times dominated by the COVID-19 pandemic, the in-house health management program “Fit mit Würth” continued to raise awareness among employees of Adolf Würth GmbH & Co. KG and a large number of other companies in the German Würth Group of healthy living and working and the creation of an overall environment that is conducive to employee health. This was achieved primarily using new digital options: Online health courses, active breaks, and lectures helped employees and their families to stay healthy. The main beneficiaries of these digital offerings were employees working from home, members of the sales force, and pick-up shop employees. A holistic approach to health management is crucial, spanning areas such as exercise, nutrition, physical regeneration, safety, social affairs, and prevention. Every two years, “Fit mit Würth” takes part in an audit to obtain the Corporate Health Award. A large number of subsidiaries are now also developing health programs of their own.
Employee survey
Employee satisfaction has always been a top priority for the Würth Group. A standardized and uniform employee survey has been carried out since 2005 in order to obtain regular information on how satisfied employees are with the Würth Group company they work for and how these satisfaction levels are developing. The results also provide structured information on the soft factors of corporate and leadership culture. The focus is on boosting employee satisfaction with the aim of improving company performance. The survey provides a benchmark both within and between individual companies in the Würth Group. Brief “pulse check” surveys on current topics are now also being used alongside the standardized regular survey. The surveys are carried out together with the Mannheim-based WO Institute (Institute for Economic and Organizational Psychology).
Thanks to our employees
The Central Managing Board of the Würth Group would like to thank all employees and employee representatives for the considerable commitment they have shown. In the current situation, everyone showed a particularly high level of flexibility and a willingness to explore new avenues. We are as grateful for this as we are for the trust they have placed in the company and their loyalty to their employer.
Macroeconomic environment
Sustained high numbers of cases and the spread of new virus variants mean that measures to contain the pandemic are being prolonged worldwide, making it difficult to come up with any reliable forecasts. Nevertheless, declining infection rates and incidence rates, the widespread roll-out of vaccines, and the continued expansionary monetary policy stance taken by the world’s major central banks are cause for optimism.
In Germany, the automotive industry in particular is expected to benefit from the global economic recovery. Prognos expects new vehicle registrations to increase by around 14 percent in 2021 (2020: – 19.1 percent), although this will not be enough to make up for the losses reported in the crisis year. Industrial sectors such as mechanical engineering (2020: – 14.0 percent) or the metal and electronics industry (2020: – 14.1 percent) also rank among the winners, with strong growth rates of six to seven percent on the books, as demand from abroad is providing a boost for export-oriented sectors of the economy. At the same time, Prognos expects the demand for capital goods from these sectors to rise again in Germany, too. The prospects for the construction industry are looking similarly positive, albeit with moderate growth of only 0.9 percent (2020: + 2.8 percent). This means that, overall, the forecasts for Germany, the Würth Group’s largest sales market, are cautiously optimistic.
The year 2021 as a whole will bring a variety of challenges for buyers due to rising customer demand coupled with limited production capacities for a large number of products. Initially, purchase prices are expected to rise significantly again. At the same time, some procurement markets will become sellers’ markets due to surplus demand. This will have the effect of increasing delivery times. Furthermore, we cannot expect any easing of the situation with regard to shipping container freight capacities for the time being. The overall situation is exacerbated by the threat that local measures to contain COVID-19 will be stepped up, although progress in vaccine production is expected to ease the situation slightly in the second half of 2021.
Despite the expected upswing in the second half of the year, it will take several more years for the economy to bounce back to pre-crisis levels. Germany suffered a 5.0 percent slump in economic output last year. The forecasts for this year vary considerably: They range from a conservative 2.8 percent predicted by the OECD, to a good 4.2 percent according to the Ifo Institute, and to a very optimistic 4.9 percent according to the RWI – Leibniz Institute for Economic Research. These forecasts are, however, now in the minority, as a large number of economists have revised their economic expectations downward again in response to the hard lockdown: In mid-February (the last valid estimate), the European Commission forecast growth of 3.2 percent for 2021. At the beginning of December, the German Institute for Economic Research (DIW) was still predicting an increase of 5.3 percent.
For the eurozone, the Würth Group’s main sales market, the European Commission currently expects growth of 3.8 percent (2020: – 6.8 percent). Employment, and as a result global productivity, fell sharply in 2020. Consumption levels also declined, although we can expect to see catch-up effects here. The IMF is forecasting global growth of 5.5 percent in 2021 (2020: – 4.3 percent). State aid will also contribute to the economic upswing. The EU’s EUR 750 billion recovery fund, for example, is designed to specifically strengthen the long-term growth prospects of economically weaker regions of the EU in the form of grants (EUR 312.5 billion) and concessional loans. The main beneficiaries will be Greece, Portugal, Spain, and southern Italy.
After France’s GDP slipped by 8.3 percent last year, experts expect to see a recovery of 5.5 percent this year. The French plan to revive the economy will play a key role in this development. Among other things, it focuses on tax cuts for the manufacturing industry.
Experts expect GDP in Italy to recover by 3.4 percent, after contracting by 8.8 percent last year. Given the limited financial room for maneuver, the EU’s recovery plan is of key importance to Italy’s future.
In Spain, the slump in growth was even more pronounced: GDP contracted by 11.0 percent in 2020. Experts expect to see a recovery of 5.6 percent in 2021. In relation to economic output, the direct grants from the EU recovery fund should have the most pronounced positive effect on Spanish economic growth at around 4.8 percent of GDP.
China (2020: + 2.0 percent) is one of the few economies that reported growth in 2020. The forecasts for 2021 are also extremely positive, with growth of 8.1 percent in the cards. The People’s Republic also completed a trailblazing change of course last year and is aiming to become a climate-neutral economy by 2060. This translates into additional opportunities for German companies in a large number of sectors (industry, power generation, transportation, construction).
India can also look ahead to a positive future, with the IMF expecting growth of 11.5 percent (2020: – 9.6 percent).
With the election and inauguration of Joe Biden in the US, all of the world’s major industrialized nations are pinning their hopes on a global economic recovery, not least thanks to expectations of less tense international relations. In addition, climate protection has secured another prominent supporter. The 46th President of the United States signed an executive order to rejoin the Paris climate agreement on his very first day in office, a development that is also expected to have a positive impact on economic development worldwide. In addition, US President Biden signed a USD 1.9 trillion COVID-19 economic rescue package on 11 March 2021. Accordingly, economic experts are predicting growth of 3.7 percent this year (2020: – 4.6 percent). This rapid recovery is due most notably to public spending.
Great Britain is also still faced by uncertainty surrounding Brexit. The IMF nevertheless expects to see economic output increase by 3.3 percent after the pandemic hit the country hard last year (2020: – 9.9 percent).
Latin America will also pick up speed again after an economic slump of 7.6 percent in 2020: Although anti-government protests are continuing this year, exports of raw materials have been hit hard, and the pandemic is not yet under control, the Kiel Institute for the World Economy (IfW) is forecasting an upturn of 4.4 percent.
Following the government shake-up at the start of last year, there were signs that Russia was on the brink of a turnaround that would see it move toward a big-spending economic policy. The virus, however, took hold of the Russian economy, too, with a contraction of 4.0 percent. Looking ahead to 2021, the IfW expects to see growth of 3.0 percent.
All in all, the global economy will remain in a very volatile state in 2021. This report takes account of the experts’ predictions up until the cut-off date of 15 March 2021.
Development of the Würth Group
- Multi-channel strategy as key success factor
- Focus on availability during pandemic
- Würth sticks to innovation strategy
With sales of EUR 14.4 billion and an operating result of EUR 775 million, the Würth Group set a new sales record in 2020. The figures prove that Würth was a reliable partner for craft and industrial businesses even during the COVID-19 pandemic and highlight the positive customer response to our services and products.
The Würth Group achieved 2.9 percent growth in Germany. Adolf Würth GmbH & Co. KG, the largest company in the Group, stood out with sales up by 7.4 percent. The foreign Group companies saw their sales slide by 0.4 percent. This development reflects the varying impact that the global pandemic has had on individual sectors. Both the Construction division (+ 12.2 percent) and Electrical Wholesale Germany (+ 10.8 percent) recorded double-digit sales increases. By contrast, those areas that supply the automotive and mechanical engineering sectors directly reported weaker performance.
Würth’s corporate strategy is navigating the Group safely through the crisis. The Würth Group has a large number of footholds in a wide range of industries. This means that it is not reliant on a single industry, a single customer, or a single market. Thanks to this broadly diversified corporate activity, the Würth Group is able to compensate for economic fluctuations in individual submarkets.
The focus in 2020, a year dominated by the pandemic, was on our capacity to deliver and remain available to our customers. This is an area in which our multi-channel strategy paid off. As the trades are considered to be systemically important, our pick-up shops were allowed to remain open. This meant that customers were able to obtain the goods they needed around the clock in some cases. The Würth24 shop concept allows us to offer our customers even greater flexibility in covering their immediate needs. In the fall, the 550th pick-up shop in Germany opened in Schwäbisch Hall. The options for ordering goods via app and e-shop, as well as for contactless pickup at parcel stations located in front of the pick-up shop, make shopping even more hassle-free and safe in these times of COVID-19. The same applies to our Click & Collect service. Our sales representatives, as central points of contact, remain a key success factor and the backbone of the company.
The year 2020 was not just marked by the crisis. The Würth Group celebrated special anniversaries: Adolf Würth GmbH & Co. KG turned 75 years old, and Reinhold Würth celebrated his 85th birthday. He has been shaping the company for more than 70 years now, in part thanks to his cultural and social commitment. In June 2020, Museum Würth 2 opened as an extension of Carmen Würth Forum at the company’s Künzelsau-Gaisbach site. The museum showcases centerpieces of modern and contemporary art from the Würth Collection.
ASSY®, a screw steeped in tradition, is testimony to just how much manufacturing and development expertise the Würth Group has at its disposal. The company has now launched the fourth generation of the screw on the market: the ASSY®4. The 1,400 different dimensions for the core range alone are testimony to the scale of this product. Only two bits are required for 80 percent of all ASSY® screw fittings. Würth is also focusing on innovation in other areas and has launched a pilot project for recyclable packaging solutions with the packaging manufacturer rose plastic. Packaging made from 100 percent post-consumer recyclate (PCR), that is to say, plastic waste from the dual system that is collected throughout Germany, has been developed. The project marks a first step toward more sustainable packaging solutions.
Construction of the Innovation Center
Despite the crisis, the Group is sticking to its innovation strategy. The Innovation Center in Künzelsau is scheduled to open in 2022. Modern laboratories and workshops are being built on an area spanning around 15,000 square meters. Around 250 people will develop and implement ideas in the Innovation Center, carrying them into the future: employees from the Research and Development Department of Adolf Würth GmbH & Co. KG and from the Group subsidiaries working in production, as well as external researchers. The cooperation with the Karlsruhe Institute of Technology KIT and the universities of Innsbruck and Stuttgart is creating a cluster of knowledge and expertise. The total amount invested amounts to around EUR 70 million.
E-business activities
E-business in the Würth Group has shown strong development over the last few years, particularly since the beginning of 2020, and has become more relevant for Würth’s customers. The ability to order goods using digital channels allows customers to make contactless purchases and meet their needs even during the COVID-19 pandemic. The central online shop, app, and e-procurement solutions are now used by more than 60 companies and are being multiplied further to create a uniform technical basis and also to allow the company to scale innovations and enhancements quickly at an international level.
Regional competence centers are being set up, for example, in South-East Asia in 2019, to support local companies with e-business expertise and further promote global multiplication. In addition to the further development of central IT solutions, the competence centers are helping the companies to establish and expand cooperations with local platforms.
In-house e-procurement solutions and cooperation with other platforms have become an integral component of the Würth Group’s e-business strategy in a quest to optimize and automate customers’ procurement processes across the board. To this end, additional specialists are being hired and trained worldwide to analyze the ordering and warehouse management processes of major customers so that they can provide proactive advice to them and implement customized solutions.
Big Data remains an important topic, allowing digital marketing activities in particular to be automated based on data and used for specific target groups. In addition to a specialized team in Berlin, a group of data scientists and analysts has been put in place at several individual companies in order to develop personalized, relevant communication and sales activities based on our customers’ purchasing and information behavior.
Overall statement on the future development of the Würth Group
Even in an environment dominated by the pandemic, economic forecasts are cautiously optimistic with the German economy proving solid in the face of the second lockdown. Although the global infection situation does not allow for any valid plans to be made, we expect to see sales growth in the mid-single digits and a proportionate increase in the operating result, as we also anticipate a certain base effect in the current fiscal year. The global changes are a source of hope, both in terms of the pandemic because of the vaccination drive, and in terms of economic development thanks to the new president of the United States. Nevertheless, it remains difficult to predict an overall effect for all of our companies. Acquisitions will remain part of our growth strategy and we will seize any opportunities that arise because of, or after, the crisis in line with our previous acquisition behavior. Even in difficult phases like the present, it is important for us to be able to generate additional growth under our own steam by being there for our customers, maintaining a high level of market activity, further expanding our sales capacities, bringing innovations onto the market, and expanding our market share through our performance and financial stability.
Our suppliers are likely to experience bottlenecks in 2021 as their capacities are fully utilized in some cases. It goes without saying that we are aiming to maintain our delivery capacity and offer our customers alternatives, using service levels, which we have been monitoring on a monthly basis across the Group for decades now, as a measure of customer satisfaction. We expect to see drastic price increases for freight costs, and a “super cycle” on the procurement side will also lead to sharp increases in commodity prices. We will rise to these challenges successfully with our 75 years of corporate experience.
One of the Group’s strengths is the ability to continually explore new avenues. In this quest, our family business is aware of its social responsibility and is focused on sustainable growth in the long term. In addition to its commitment to the social and economic aspects of sustainability, the Würth Group is also involved in a wide array of environmental activities that are to be bundled within the Group in the future, laying the foundation for Group-wide reporting. The first sustainability report at the Group level is to be published in 2022.