The Würth Group is the global market leader in its core business: the production and sale of fastening and assembly materials. Headquartered in Künzelsau, Germany, the Group operates worldwide and includes over 400 companies with 2,497 pick-up shops in more than 80 countries—from the US, Greenland, Europe, and South Africa to India, China, and New Zealand.
The Würth Group is divided into two operational units: The Würth Line focuses on the production and sale of assembly and fastening materials for customers in trade and industry. Other trading and production companies, known as the Allied Companies, operate in related business areas, ranging from electrical wholesale and electronics to financial services. The Group generated sales of EUR 17.1 billion in the 2021 fiscal year.
The screw wholesaler Adolf Würth, established in 1945 with just two employees, has evolved into a Group with over 83,000 employees, more than 33,000 of whom work as members of the sales force. More than four million customers place their trust in the high-quality products and the comprehensive service that extends far beyond the actual product.
In order to continue placing highly competitive products on the market, Adolf Würth GmbH & Co. KG, the nucleus of the Group, is investing in an innovation center at its headquarters. Developers, product managers, scientists, and users from industry and trade will work together on product and system innovations from the third quarter of 2022 onwards. To this end, Würth is also involving employees from its own production companies in the development processes on site.
Assuming social responsibility is a firmly established component of the Würth Group’s corporate culture—be it in economic, social, cultural, or ecological terms.
The Würth Group and the Würth Foundation contribute to a vibrant cultural landscape and social welfare. The Group runs, for instance, five museums in the German Hohenlohe region and another ten associated galleries across Europe that display international works of art, mainly from the Würth Collection, with no admission charges. In 2017, the Würth Philharmoniker orchestra was founded as the musical ensemble of Reinhold Würth Musikstiftung gGmbH. In addition, the Würth Group and the Würth Foundation are committed to helping people with disabilities. Examples of this commitment include Hotel-Restaurant Anne-Sophie and our support of the Special Olympics, as well as the Markus Würth Endowed Professorship for Pediatric Neuro-Orthopedics and Cerebral Palsy at the Technical University of Munich. Another focus is on education and research, be that at Freie Schule Anne-Sophie schools in Künzelsau or Berlin, funded by the Würth Foundation, or Reinhold-Würth-Hochschule on the Künzelsau campus. Soccer and winter sports are the focal points of the company’s sports sponsorship.
In order to also live up to its ecological commitment, the company is devoting greater attention to exploiting its potential in the areas of climate neutrality and the circular economy. Adolf Würth GmbH & Co. KG has set itself the goal of becoming climate-neutral (Scope 1 and 2) at its locations in Germany by 2024. In addition to energy efficiency, the company is focusing on producing its own electricity using photovoltaic systems and on switching its vehicle fleet over to alternative drives. The sustainability report planned for fall 2022 will provide information on the related activities at the Group level.
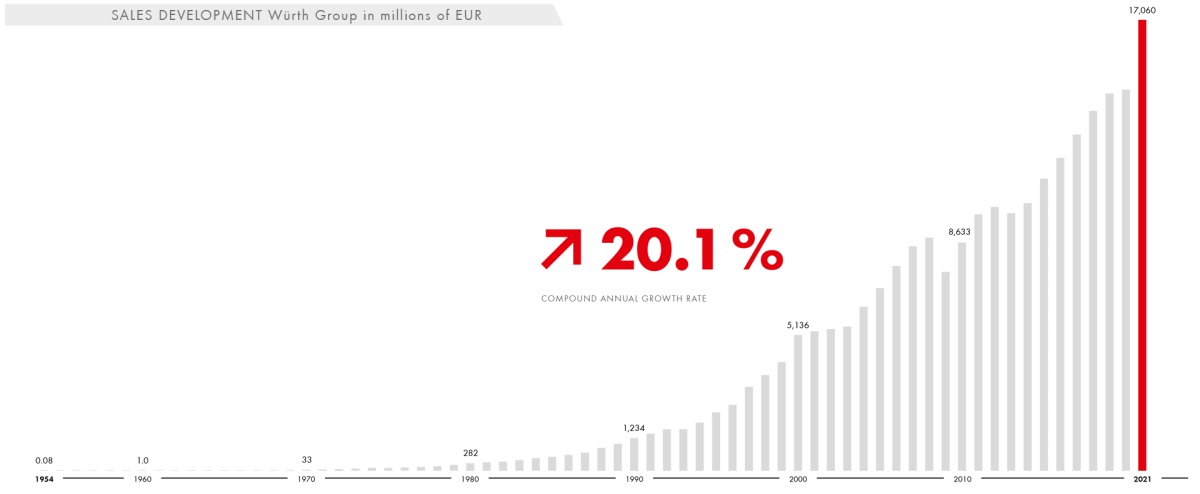
The COVID-19 pandemic continued to keep the global economy on edge in 2021. While the economy was able to bounce back from the biggest growth slump in recent decades (3.1 percent in 2020), 2021 as a whole still lagged behind expectations with a global increase in gross domestic product of 5.9 percent. The situation varied considerably from economy to economy. Deutsche Bundesbank has provided various explanations for this: Different measures of varying duration, as well as the expansionary monetary and fiscal policies pursued by the world’s industrialized nations, but also differences in the pace of vaccination and the immunization of the population had a decisive impact on the variance in economic trajectories. All in all, the advanced economies suffered rather minor longer-term damage. Gross domestic product increased in the world’s largest economies: The US economy grew at a rate of 5.7 percent, the fastest pace witnessed since 1984 (2020: –3.5 percent), while China saw a stronger increase than expected at 8.1 percent (2020: +2.3 percent).
- German economy back on growth track after COVID-19 crash, but weaker than neighboring countries to the south
- Ongoing supply and material bottlenecks put a damper on sentiment, but exports rise nevertheless to record level
- Overall, the trade sector came through the crisis better than the economy as a whole
The economy in Germany, the Würth Group’s largest single market, mounted a recovery in 2021 with gross domestic product up by 2.7 percent following the slump triggered by the COVID-19 pandemic in the previous year (2020: –5.0 percent), albeit a less significant increase than originally expected. Whereas private consumption slowed noticeably, exports, a key pillar of the German economy, reported strong growth of 14.0 percent year-on-year (2020: –9.1 percent), even outstripping pre-crisis levels.
According to Eurostat, the eurozone economy grew by 5.2 percent overall in 2021, recovering from its slump at the start of the COVID-19 crisis (2020: –6.4 percent). The economic situation started to cloud over, however, towards the end of 2021. Persistent supply problems, rising prices and the emergence of the Omicron variant of the coronavirus hit the economy hard. Growth in 2021 was, however, very uneven. While the German economy was slow to catch up, Southern Europe embarked on a more pronounced recovery path.
The Würth Group’s core markets, trade, the automotive industry, the electrical industry, and mechanical engineering, were hit by supply bottlenecks, shortages of raw materials, and rising prices in 2021. Bottlenecks slammed the brakes on industrial output. All in all, total manufacturing output increased nevertheless by 3.0 percent in 2021 (2020: –8.5 percent).
A lack of components, especially semiconductors, also left its mark on the automotive sector. This meant that the downward trend witnessed in the previous year continued, albeit at a somewhat slower pace. The German market contracted by 10.0 percent (2020: –19.1 percent).
According to RWI, the Leibniz Institute for Economic Research, the skilled trades, the most important single market for the Würth Group, made it through the COVID-19 crisis better, all in all, than the economy as a whole. Despite nominal sales growth in 2020 and 2021, however, marked price increases in raw material procurement led to real sales losses in craft businesses.
After fueling an increase in sales in the trades in 2020, the construction industry was no longer a growth driver in 2021. Despite increased orders, growth was hampered significantly by the increasing shortage of building materials: In the mainstream construction sector, sales rose by 6.0 percent in 2021 in real terms (2020: +4.3 percent).
- Sales growth of 18.4 percent to EUR 17.1 billion
- Operating result exceeds EUR 1 billion mark for the first time
- Multi-channel strategy bears fruit—increased number of pick-up shops and share of sales attributable to e-business
The Würth Group achieved record sales and a record operating result in the 2021 fiscal year: In 2020 the consolidated statement generated sales of EUR 17.1 billion, up significantly on the previous year (2020: EUR 14.4 billion). The growth rate of 18.4 percent increases to 19.0 percent after adjusting for foreign exchange effects. Germany once again proved to be resilient in the face of the COVID-19 pandemic. In this market, the Würth Group achieved growth of 14.3 percent to EUR 6.9 billion (2020: EUR 6.1 billion). The companies outside of Germany performed even better, with sales up by 21.4 percent to EUR 10.1 billion (2020: EUR 8.3 billion).
In the second year of the COVID-19 pandemic, the Group once again clearly demonstrated its performance thanks to the diversification of risk based on its international positioning, diversification across various business areas, and its multi-channel strategy. The Group companies in Southern and Western Europe, for example, reported above-average growth rates, due among other things to the very pronounced slumps in sales in 2020 in countries such as Spain, Italy, and France as a result of the pandemic. In terms of individual markets and sectors, the Electrical Wholesale (+28.9 percent) and Electronics (+32.5 percent) business units, and especially the Würth Elektronik eiSos unit (+36.5 percent), were particularly successful. It is encouraging to see that the Industry division was able to more than compensate for its slump in sales in 2020, achieving the highest growth among the Würth Line divisions at 18.4 percent.
The number of pick-up shops worldwide has more than doubled in the past ten years to reach 2,497. Our customers’ procurement of materials via these shops represents an important component of our multi-channel strategy. In addition, the digital possibilities offered by online shops, e-procurement, and the Würth App offer the right solutions for contactless shopping. In the 2021 fiscal year, e-business generated sales of EUR 3.4 billion, which corresponds to a new record with 19.9 percent of the Group’s total sales.
The Group’s own production plants in Germany and Europe ensure a certain degree of independence from global supply chains. Around 70 percent of goods originate in Europe. Nevertheless, supply bottlenecks also made themselves felt in individual areas of the Würth Group in 2021, albeit to a minor extent. The chip shortage, for example, had an impact on the companies in the Group that depend on the automotive industry.
At EUR 1,270 million, the operating result was up significantly year-on-year (2020: EUR 775 million) and marks a new record in the history of the Würth Group. Strong sales growth and higher productivity contributed significantly to the positive result. Due to the pandemic, the usual costs for travel, trade fairs, and conferences were not incurred in 2021. The return on sales increased considerably year-on-year to 7.4 percent (2020: 5.4 percent). In the past fiscal year, the Würth Group once again made sustained investments in its various business units and markets in order to implement its planned strategies. Capital expenditure on intangible assets and property, plant and equipment, excluding acquisitions, came to EUR 553 million in 2021.
The number of employees in the Würth Group increased by 4,044 to 83,183 in the 2021 fiscal year. In Germany, the Group has 25,438 employees. Around the world, the Würth Group employs more than 33,000 sales representatives. Including sales-related areas, more than 50,000 employees have direct contact with customers.
- Germany remains biggest individual market
- Southern and Western Europe emerge stronger from the pandemic-ridden year of 2021
- Eastern Europe benefits from company acquisition
Germany remains the most important individual market for the Würth Group, accounting for 40.7 percent of sales. The Würth Group achieved a clear double-digit increase of 14.3 percent in this market, a very positive result. At 21.4 percent, growth outside of Germany was significantly more dynamic than in Germany. As a result, the share of sales attributable to the German companies fell by 1.4 percentage points compared to 2020. The above-average growth rates seen outside of Germany can mainly be attributed to the Group companies in Southern, Western, and Eastern Europe, which were hit by dramatic slumps in sales in countries such as Spain, Italy, and France in 2020 due to the COVID-19 pandemic and have since recovered.
The decisions made at the start of the pandemic in 2020 not to reduce capacities within the Würth Group and to stick to the multi-channel strategy paid off again in 2021. The interplay between the various sales channels allowed the Group to make up for lost sales, maintain its proximity to customers, and ensure material supplies. The decentralized structure of the Würth Group, with over 400 companies in more than 80 countries, and the associated geographical diversification were key pillars in this respect. We supplied more than 4 million customers last year, with over 50 million orders leaving our warehouses.
In the 2021 fiscal year, sales of EUR 6,939 million were generated in Germany, up by 14.3 percent (2020: EUR 6,073 million). The German companies continued to reap the benefits of their robust performance in 2020, a year dominated by the pandemic. Although the economic data for Germany was corrected downward toward the end of the year, the stability of the individual business models allowed for successful development. The last time the German companies in the Würth Group achieved double-digit growth was in 2011. The Electrical Wholesale companies, the Würth Elektronik Group, specifically Würth Elektronik eiSos in Waldenburg, the production companies, and Würth Industrie showed particularly successful development in Germany. The German companies that act as direct suppliers for the automotive and mechanical engineering sectors and that were hit hard by the ailing economy in 2020, such as Arnold Umformtechnik or the tool distributor Hahn+Kolb, were able to recover and grow in 2021. The only exception to the positive development relates to the German companies in the Trade business unit, which cover sales to DIY stores. They were impacted by the lockdown imposed at the beginning of 2021 throughout the entire fiscal year and suffered a 4.5 percent drop in sales.
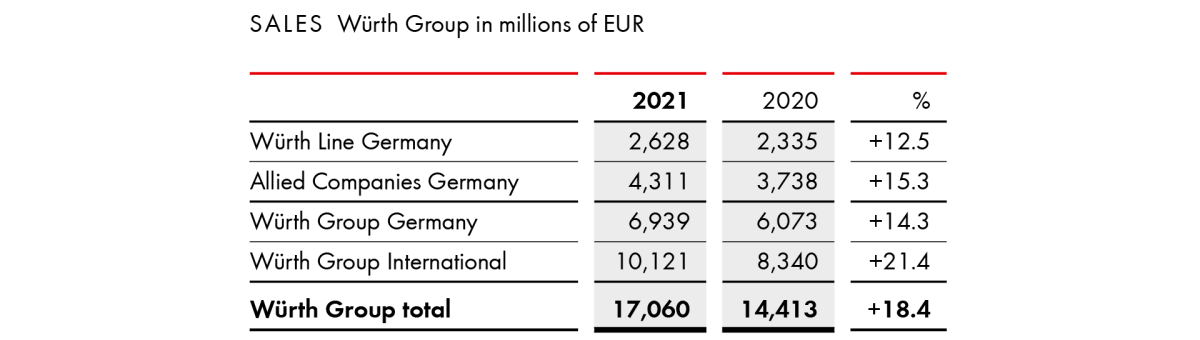
Adolf Würth GmbH & Co. KG, the parent company and at the same time largest individual company in the Group, generated sales of EUR 2,511 million including intra-Group sales (2020: EUR 2,215 million). This corresponds to an increase of 13.4 percent and marks the strongest growth achieved by the company in the last 10 years. On 16 July 1945, one of the success stories of post-war Germany began with the establishment of the company. It plays a pioneering role within the Group and successfully introduced the multi-channel strategy back in 2014. Alongside the sales force and in-house sales staff, the 574 pick-up shops (2020: 552) are key to the company’s positive development. Even during the lockdown phases in Germany, these shops were open continuously due to their systemic importance, and our customers were able to cover their immediate needs at all times. This puts our Group’s flagship closer to our customers than any of our competitors. The response to physical distancing requirements was the successful further expansion of e-business, whose sales increased by 19.8 percent to account for a 19.0 percent share of sales in 2021.
Professionalism, both internally and externally, coupled with dynamic sales growth explain the high level of profitability of Adolf Würth GmbH & Co. KG. It was able to follow in the footsteps of 2020 and again achieve a record operating result in excess of EUR 250 million in the 2021 fiscal year. This earnings power is also a prerequisite for investments in forward-looking sales, logistics, and product solutions: for instance, the construction of the new innovation center that is being built on the campus in Künzelsau and is set to open in the third quarter of 2022.
All in all, Germany accounts for an operating result totaling EUR 639 million (2020: EUR 376 million), making it the most profitable region.
In 2021, the Würth Group companies in Southern Europe were able to keep up the momentum from the fourth quarter of 2020 and achieve significant double-digit growth of 24.9 percent to EUR 2,438 million under their own steam. This means that Southern Europe increased its share of sales within the Würth Group in 2021 and is now the second-largest region within the Group after Germany, with a share of 14.3 percent. In terms of the absolute share of sales, Italy is the dominant country in the Southern European region, followed by Spain and, with a wide margin, Portugal.
While the region did not escape the COVID-19 pandemic unscathed in 2021 either, the companies were able to achieve very positive sales development by responding quickly and consistently to what were repeated exceptional situations. This was supported by many years of cooperation with customers and suppliers built on trust. Both the Italian and the Spanish companies in the Würth Group were able to increase their sales by more than 20 percent. In order to continue driving growth dynamically in the region in the future, the number of employees was increased by 2.2 percent. Out of the 13,054 employees, more than 7,700 work in the sales force. No other region has such a substantial sales force.
The Americas, which include both the US and Brazil, remained the continent that was hit the hardest by the COVID-19 pandemic in 2021. In addition, many countries in the Americas were hit by natural disasters such as wildfires, droughts, hurricanes, and tornadoes. Both effects hindered economic development. Nevertheless, the US economy bounced back from the effects of the pandemic last year and recorded the strongest growth witnessed since 1984. This trend was driven by increased consumer spending, capital investments, exports, and investments in inventories. The election of the 46th president of the United States, Joe Biden, and the associated realignment of the US also provided a positive boost to economic development in North America, but also worldwide, and trade conflicts were contained further in 2021. The Würth Group benefited from this trend and was able to grow its sales in the Americas region to EUR 2,370 million (+19.5 percent). In local currency terms, growth actually exceeded 20 percent.
The majority of companies in the US, the region’s largest individual market, achieved double-digit growth. This growth extended beyond pandemic catch-up effects. In line with the strategy of the Würth Group, the companies in the US were also strengthened by acquisitions in a quest to complement the range of products and services they offer where worthwhile opportunities present themselves. By way of example, 100 percent of the shares in ORR Safety Corporation (ORR) were acquired on 15 March 2021. The buyer was the US company Northern Safety Co., Inc. In 2021, ORR generated sales of EUR 80 million and employed a workforce of 170 people. The company operates as a B2B distributor of personal protective equipment and is headquartered in Louisville, Kentucky.
The companies in South America, which account for around one percent of Group sales, also showed very encouraging performance in 2021, led by Würth Brazil, the largest company in the region. Sales growth in euro of 37.2 percent and an increase of 50.1 percent in local currency terms constitute above-average growth rates within the Würth Group, even though they are distorted positively by pandemic-related catch-up effects.
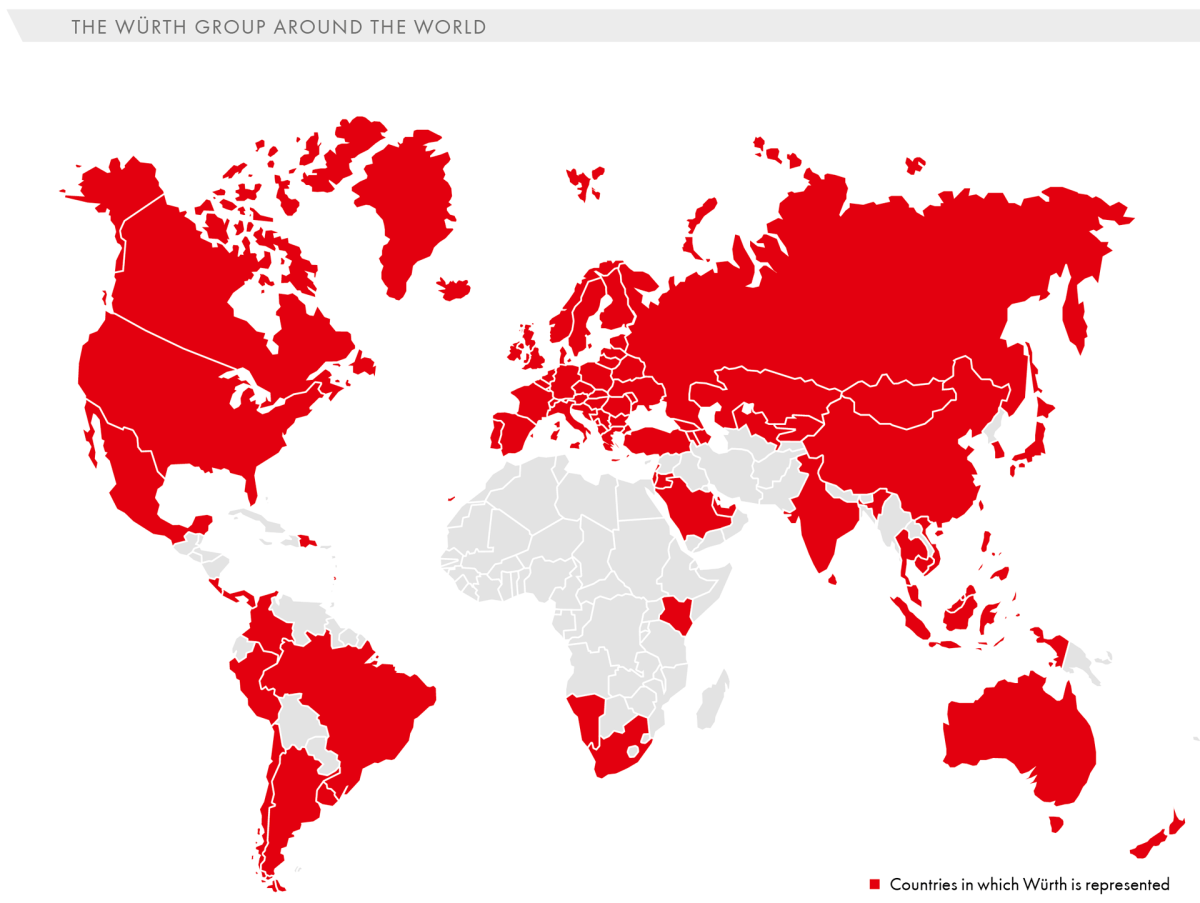
Western Europe is home to many of the Group’s more established companies as it was there that the internationalization of the Würth Group began: one of the Group’s major success factors. Sales increased by 18.6 percent to a new record level of EUR 2,365 million. All of the countries in this region recorded double-digit growth in 2021, with the exception of the companies in Switzerland (+6.1 percent). This is due primarily to the rather subdued sales performance achieved by the Swiss direct selling companies compared with the Würth Group as a whole.
The two countries with the highest sales, France and Austria, achieved particularly successful development, with growth of 18.9 percent and 20.9 percent respectively. Both countries achieved very promising, sustainable success in the area of e-business. The two countries account for 67.9 percent of the region’s sales. Sales growth in the United Kingdom, adjusted for currency effects, came in at 32.5 percent, well above the growth rate for the region as a whole. It is impossible to find any conclusive answer as to the extent to which this includes catch-up effects relating to the pandemic or whether the situation is already showing signs of returning to normal after Brexit.
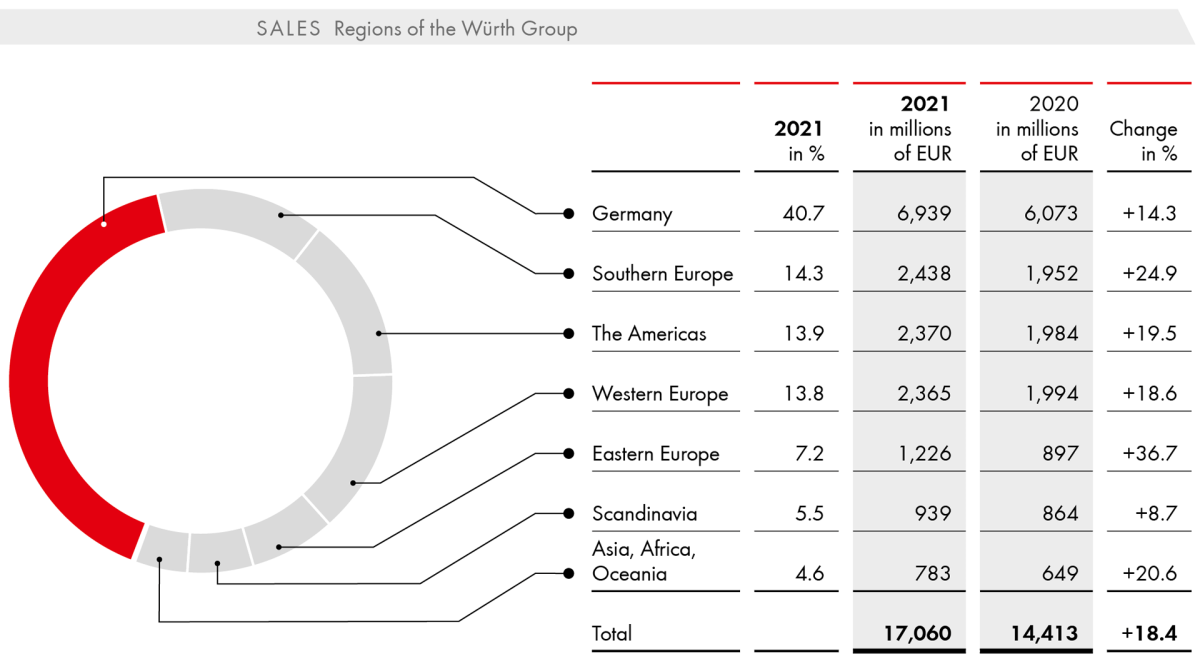
The Eastern Europe region achieved the strongest sales growth among the seven regions. The 36.7 percent increase was, however, boosted by the acquisition of Kaczmarek Electric S.A., which has its headquarters in Wolsztyn, Poland, in early 2021. The company is active in the electrical wholesale business. It has always been part of the Group’s growth strategy to add targeted acquisitions to successful business areas where it makes sense to do so. After adjustments to reflect this acquisition, the Eastern European companies closed the 2021 fiscal year with a 22.3 percent increase in sales, which is still above-average. The Würth Group employs 9,200 people in the region.
The structure of companies in the Scandinavian region has been relatively stable in recent years, which also reflects the maturity of the market. In the 2021 fiscal year, this region was the only one that fell well below the average for the Würth Group, with sales growth of 8.7 percent. After adjustments to reflect the sale of Arvid Nilsson Sverige AB in October 2020, the companies increased their sales by 11.1 percent. This region is home to another Würth Group flagship company: Würth Finland. For more than four decades now, the company has delivered impressive performance marked by a combination of sustained excellent market penetration and high levels of profitability. Würth Finland also spearheaded the spread of the successful “pick-up shops” sales concept within the Würth Line. The company now has 194 pick-up shops, five of which were added over the last 12 months.
Asia, Africa, and Oceania still only play a minor role for the Würth Group at present. The share of sales attributable to this region has been stable at a level of under five percent for years now (2021: 4.6 percent).
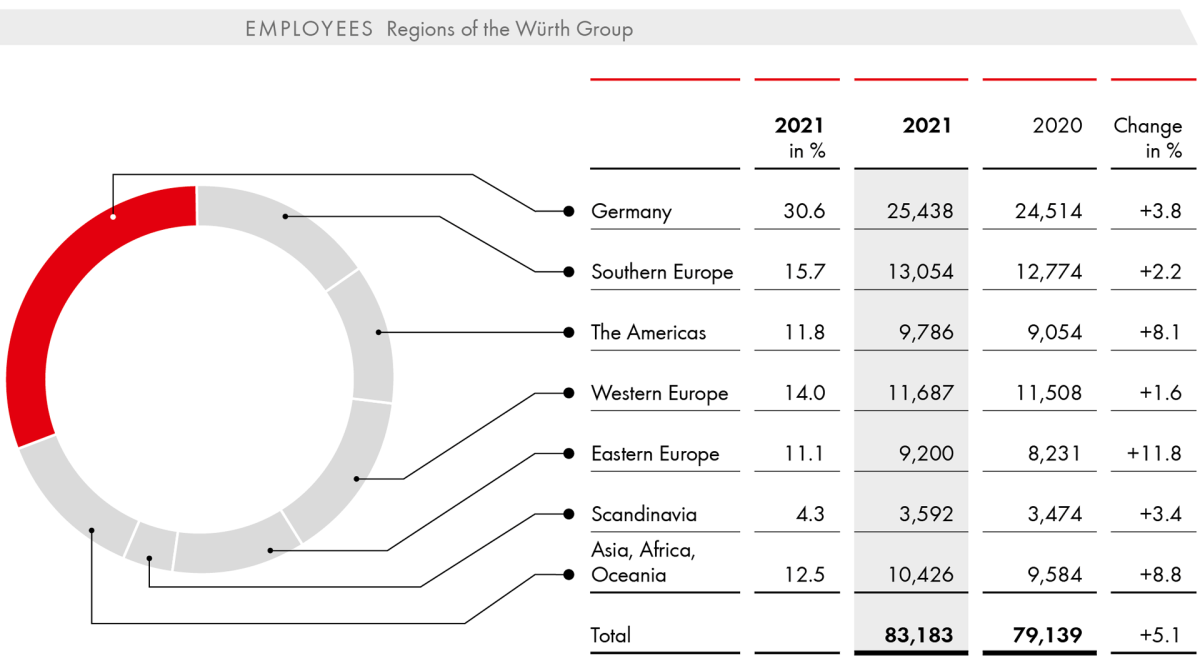
The divisions of the Würth Line
The business activities of the Würth Line focus on the production and sale of assembly and fastening materials for customers in trade and industry. Within the Würth Line, the operating business units are split into Metal, Industry, Auto, Wood, and Construction divisions.
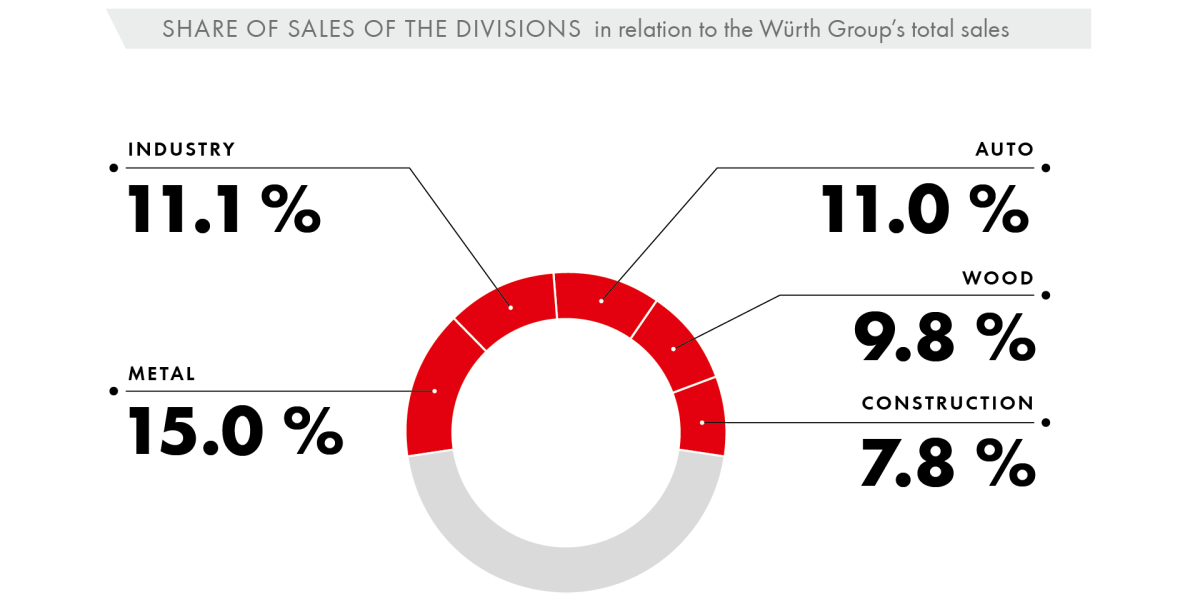
Metal division
The Metal division offers its customers innovative solutions to support them in their daily work today and in the future. Our core competency, direct selling, coupled with our pick-up shops and the various options for placing orders online, allows us to offer our customers top-quality advice and options for the procurement and provision of suitable products for everyone.
Metal subdivision
This subdivision directly serves customers in the metalworking and metal processing industries, and its main customers include metal and steel fabricators, fitters, and machine and vehicle manufacturers.
Installations subdivision
This subdivision concentrates on electricians, gas, heating and water installation firms, and air-conditioning and ventilation system engineers.
Maintenance subdivision
This subdivision addresses customers with in-house repair shops from a whole range of sectors, such as industrial enterprises, hotels, shopping centers, airports, and hospitals.
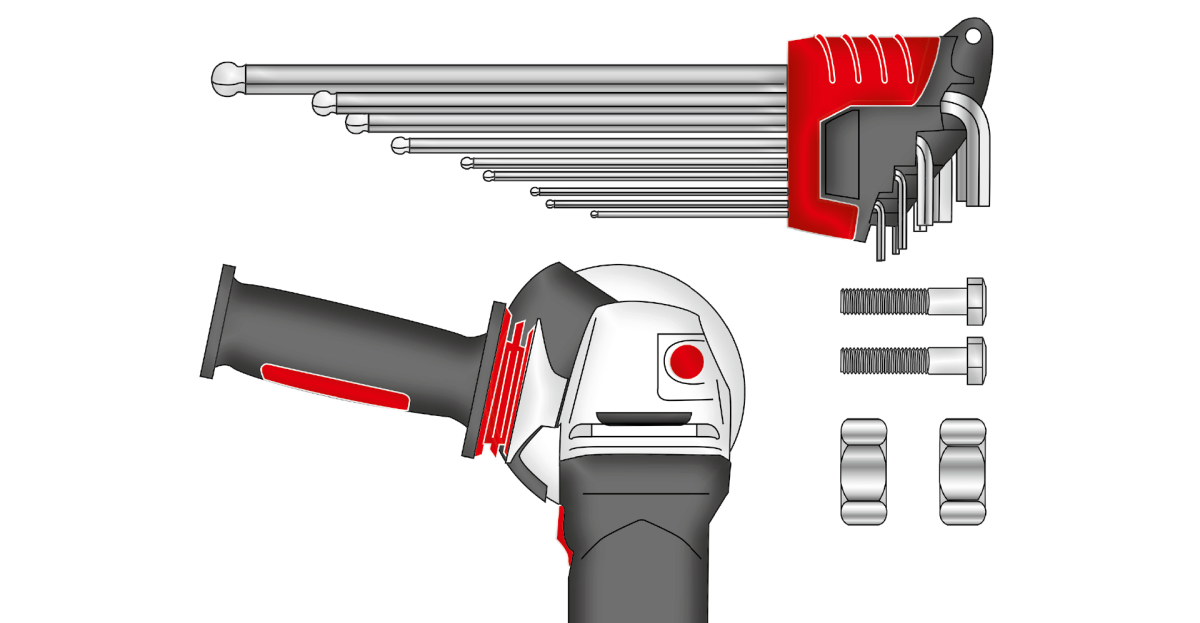
Industry division
The entities of the Industry division are specialized companies with a complete range of assembly and connecting materials for industrial production, maintenance, and repair. In addition to this comprehensive standard range, the division’s strength lies in customized logistics concepts for supply and service, along with the provision of technical consulting.
The innovative further development of procurement and logistics systems within the Industry division emphasizes the role of full automation and systems in stocking and replenishing Würth products for manufacturing customers. One key focus remains the maximum availability of C-part supplies directly at the place of consumption, in the warehouse and at the workstation. All solutions are made available as part of a holistic approach to the supply of production and operating resources. As in the past, the focus is on expanding digital processes and sales channels.
The strategic focus remains on personal on-site customer service thanks to a global network of companies and, as a result, the same high standards for quality, products, and processes across the globe.
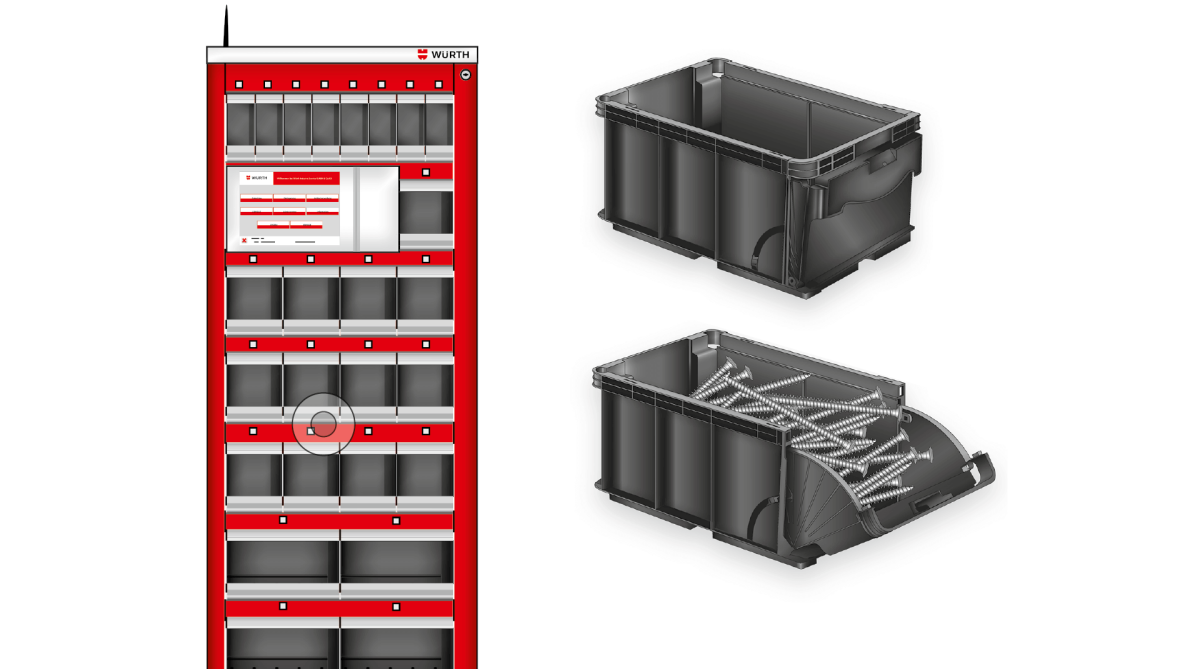
Auto division
The Auto division sees itself as a competent partner for car workshops—today and in the future. In addition to a comprehensive product range meeting the highest quality standards, we offer our customers innovative services and systems to optimize their internal processes. In complementary areas of expertise such as diagnostics, air-conditioning services, and special tools, we support workshops in the automotive and commercial vehicle markets. We also offer solutions for alternative drive systems and the increasing digitalization in the automotive aftersales segment.
Car subdivision
The customers in the car subdivision include vehicle manufacturers, brand-specific and independent car dealers, customers with large vehicle fleets, bodywork specialists, vehicle restorers, tire changing businesses, and businesses in the bike segment.
Cargo/Commercial Vehicles subdivision
The customers of this subdivision are authorized commercial vehicle repair shops, independent commercial vehicle repair shops, repair businesses focusing on construction and agricultural machinery, transportation and logistics companies, bus companies, businesses specializing in repairing and renting working platforms and forklifts, public-sector municipal utilities and waste disposal companies, as well as companies from the agricultural and forestry sector.
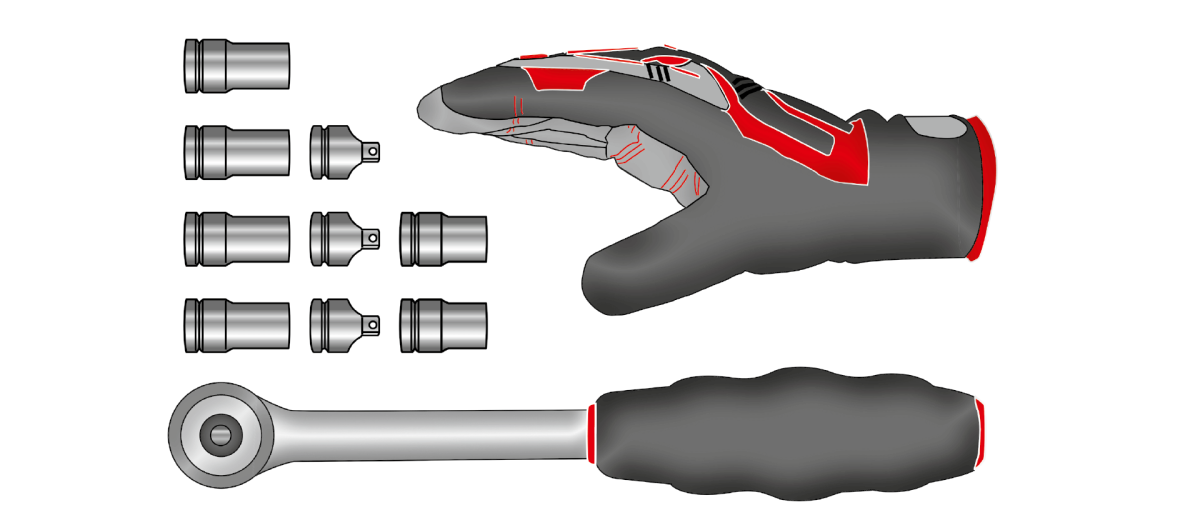
Wood division
The Wood division supports its customers in the entire woodworking and wood processing trade with a tailored product portfolio and specific application solutions. The product range includes wood screws, fittings, chemical-technical products, as well as material treatment and structural connection products.
Thanks to a high level of expertise and holistic sales solutions, we not only offer our customers products that are perfectly tailored to suit their needs, we also see ourselves as a personal advisor, assisting our clients from the preparation of their initial plans to the completion stage.
In these endeavors, the Wood division is responding to the latest trends in the industry: The WÜDESTO online configurator already allows customers to create customized furniture elements and order semi-finished parts with exact dimensions in Germany, Austria, and Italy. In order to sustainably develop the e-business area internationally and to meet demands in the skilled trades, there are already plans to integrate further companies into WÜDESTO.
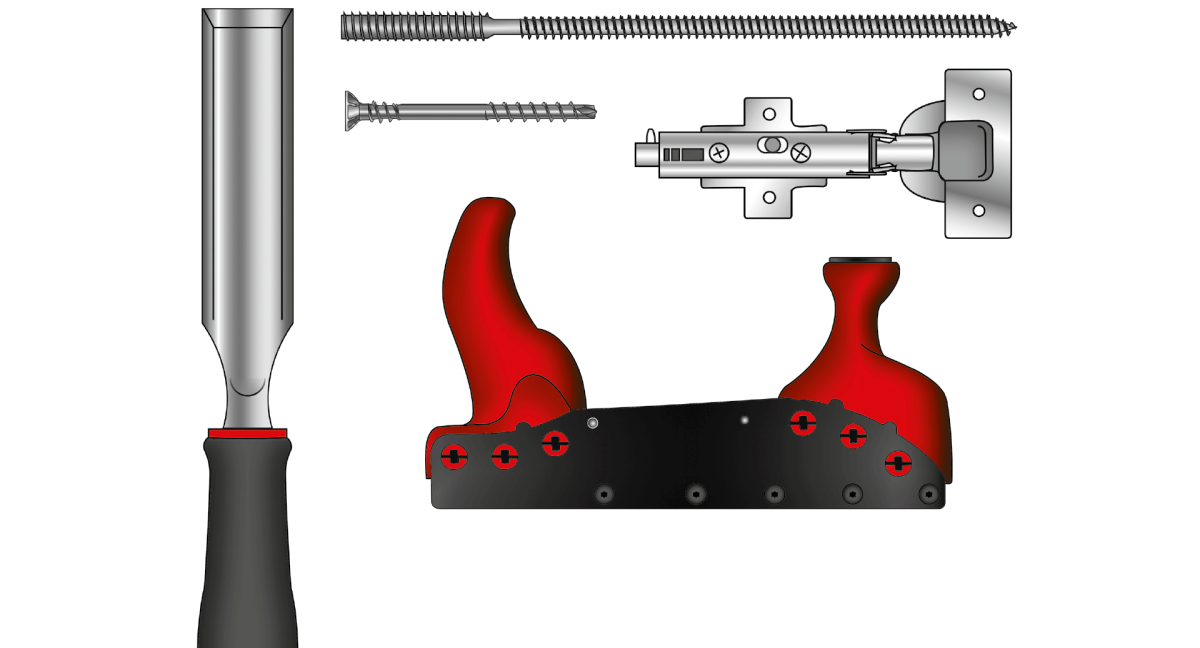
Construction division
The Construction division aims to supply construction companies across the globe at the regional, national, and international level with standardized high-end products and services. The pick-up shops are the ideal port of call for customers looking to cover their immediate needs. The sales force acts as a permanent point of contact at the construction site. They are responsible for optimizing the processes associated with the main trades involved in the shell construction phase and in the various technical building installations as part of the project business.
The Construction division encompasses all sales units responsible for serving customers in the building and civil engineering industry and the finishing trades. The focus is on construction companies, technical building equipment, roof and wood construction customers, finishing and facade specialists, and direct supplies to construction sites. Customized service and logistics solutions are also provided, such as equipped material stores directly at the construction site. There is an increasing focus on strategic target groups such as builders, planners, architects, and project managers.
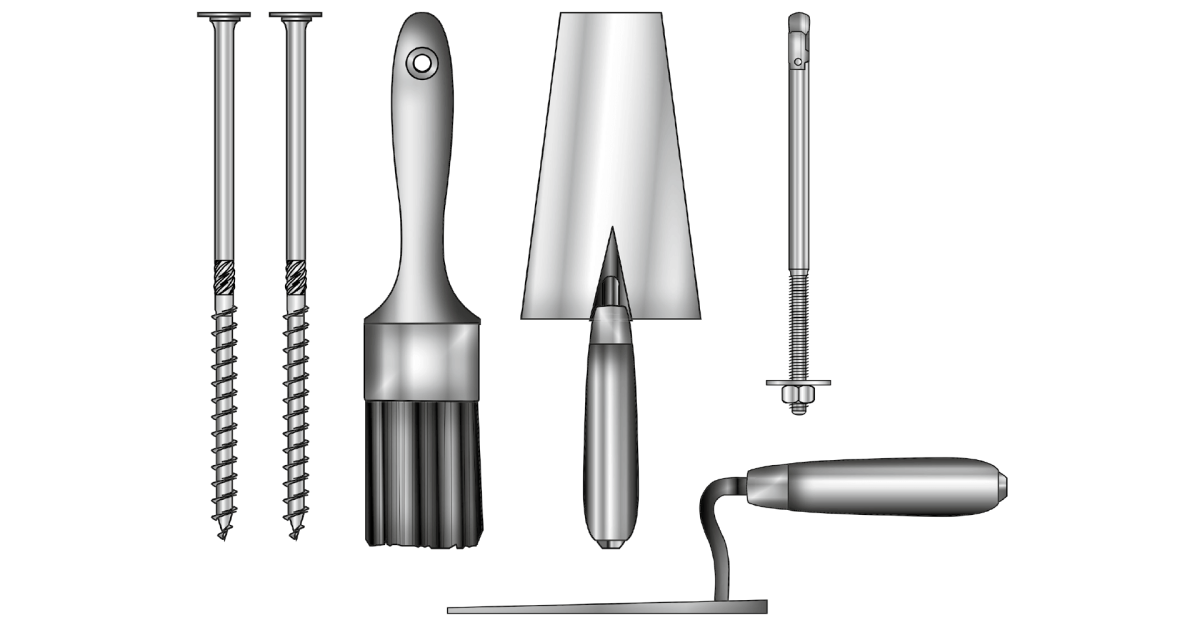
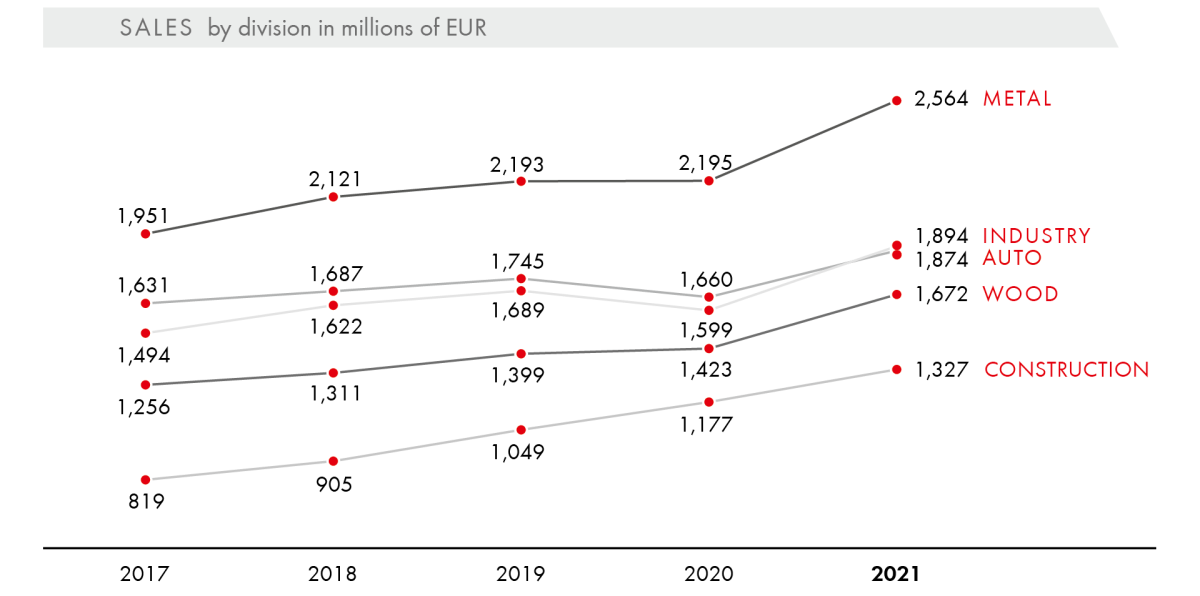
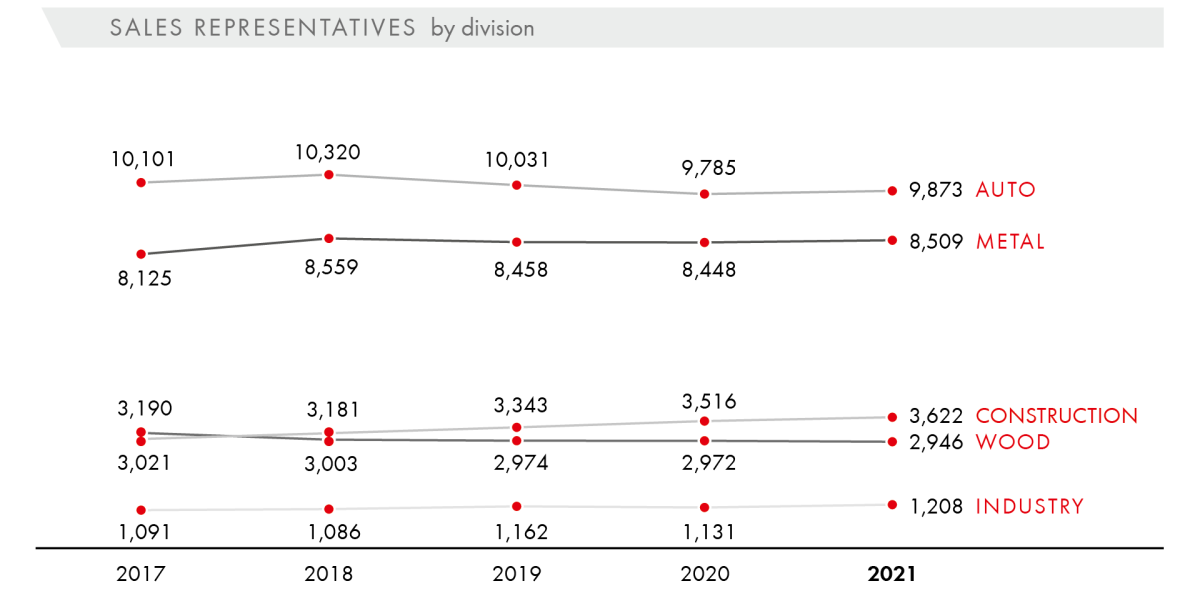
The business units of the Allied Companies
The Allied Companies operate either in business areas related to the Group’s core business or in diversified business areas, rounding off the Würth Group’s portfolio. They are divided into nine strategic business units. With the exception of a small number of manufacturing companies, the majority are sales companies operating in related areas.
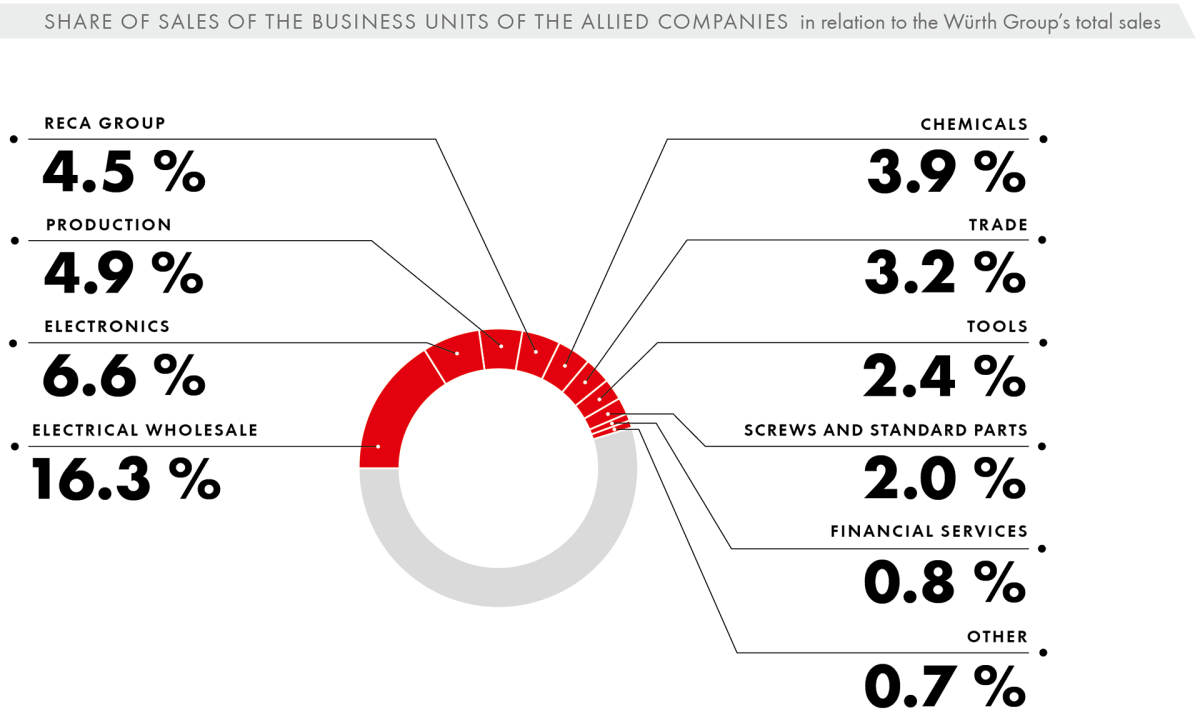
Electrical Wholesale
The business activities of these companies include products and systems covering the areas of electrical installation, industrial automation, cables and lines, tools, data and network technology, lighting and illumination, household appliances and multimedia, electrical domestic heating technology, and regenerative power generation. Trading activities are supplemented by extensive consultancy and service ranges and are aimed at professional customers from the trade, industry, and retail/wholesale sector.
- Growth outstrips market trend: Electrical Wholesale achieved new record sales of EUR 2,781 million in 2021
- More than 6,400 employees
- Share of total sales up to 16.3 percent
- Close partnerships with suppliers enabled this successful trend in the face of existing supply chain problems
- Renewed increase in total number of customers
- The acquisition of Kaczmarek in Poland made the unit one of the leading suppliers in the Polish electrical wholesale segment
- Continued heavy investment in digitalization
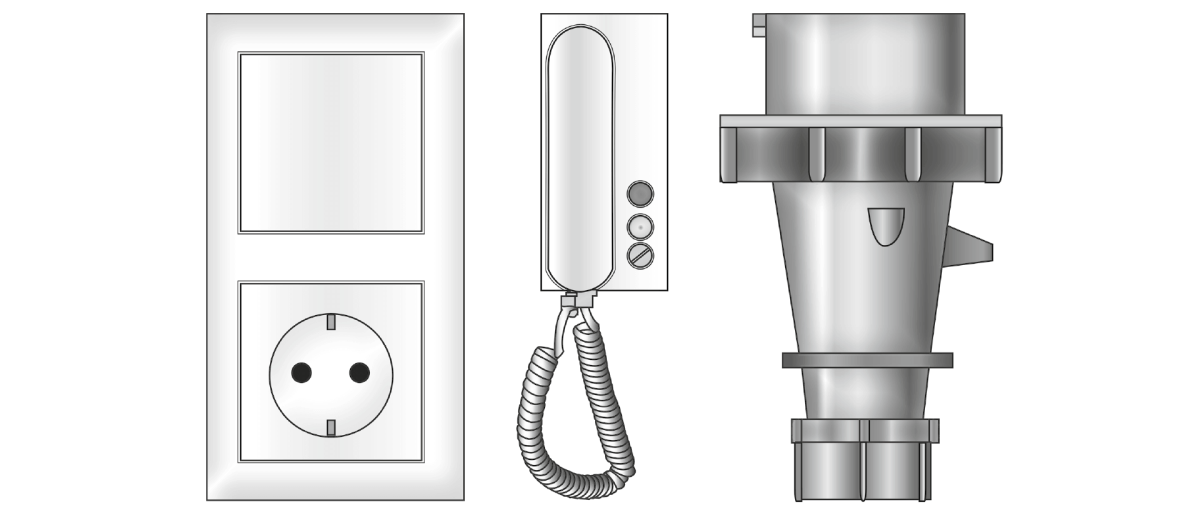
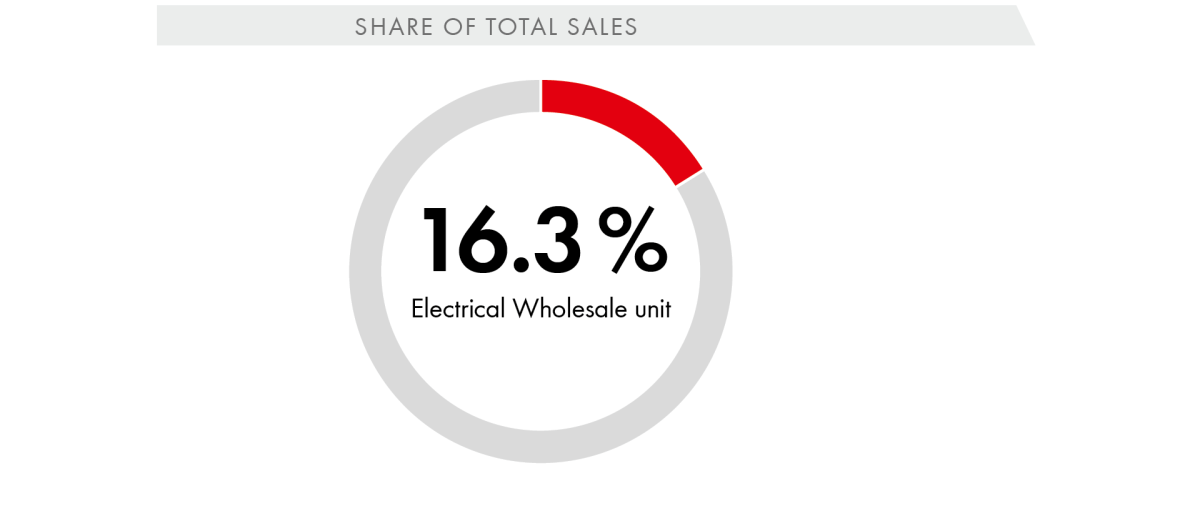
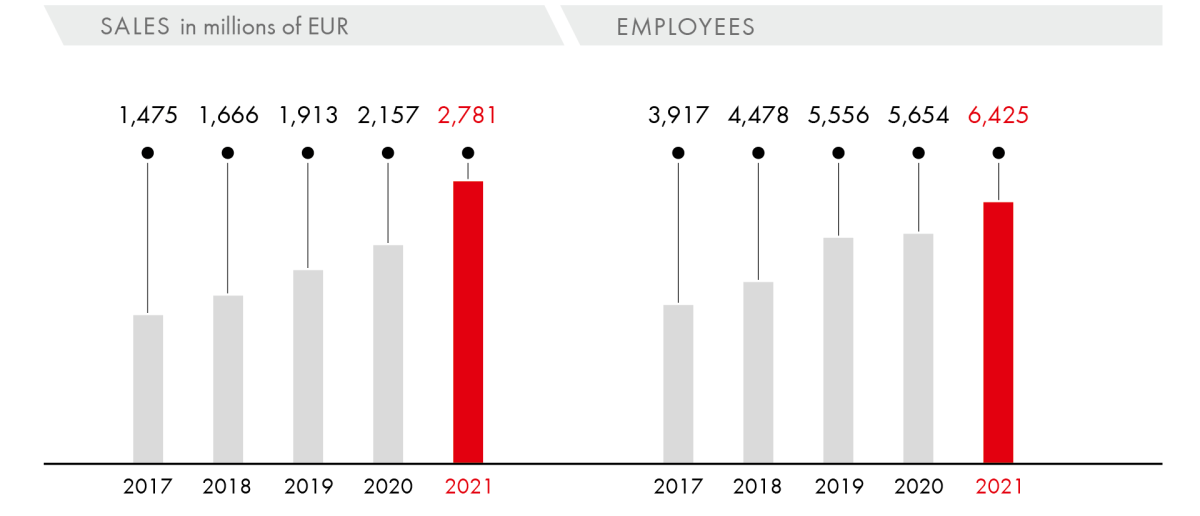
Electronics
The Electronics unit produces and sells electronic components such as printed circuit boards, electronic and electro-mechanical elements, and full system components from smart power and control systems.
- Würth Elektronik Group: sales in excess of EUR 1 billion for the first time—all business units reported new record sales
- Würth Elektronik CBT (printed circuit boards): Use of the new ultra-thin SLIM.flex printed circuit boards in the LHC particle accelerator at the European Organization for Nuclear Research CERN near Geneva
- Würth Elektronik eiSos (passive electronic components): Construction work started on high-tech innovation center in Munich-Freiham
- Online platform REDEXPERT® ranked first in the readers’ choice of the industry magazine ELEKTRONIK in the software category
- Würth Elektronik ICS (electronic and electromechanical solutions): Acquisition of enfas GmbH strengthens expertise in the field of intelligent controls
- Expansion of production capacities with new fully automated pressfit center for electromechanical assemblies
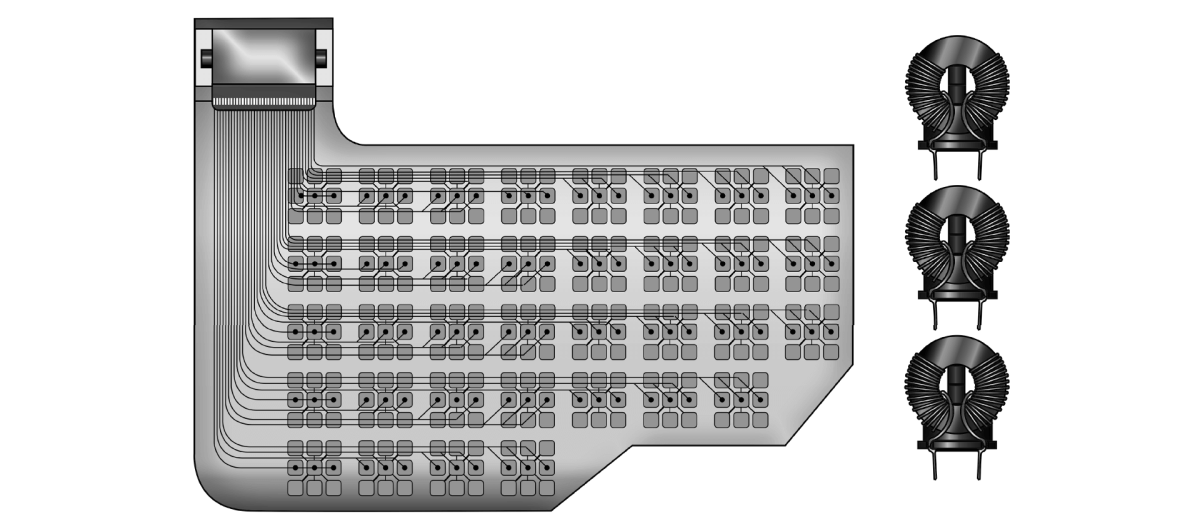
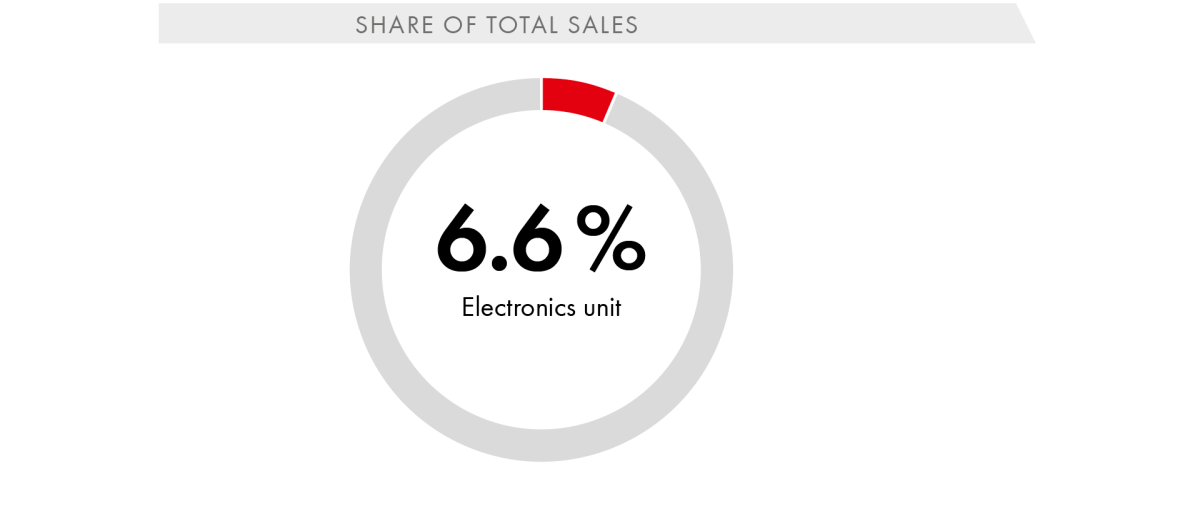
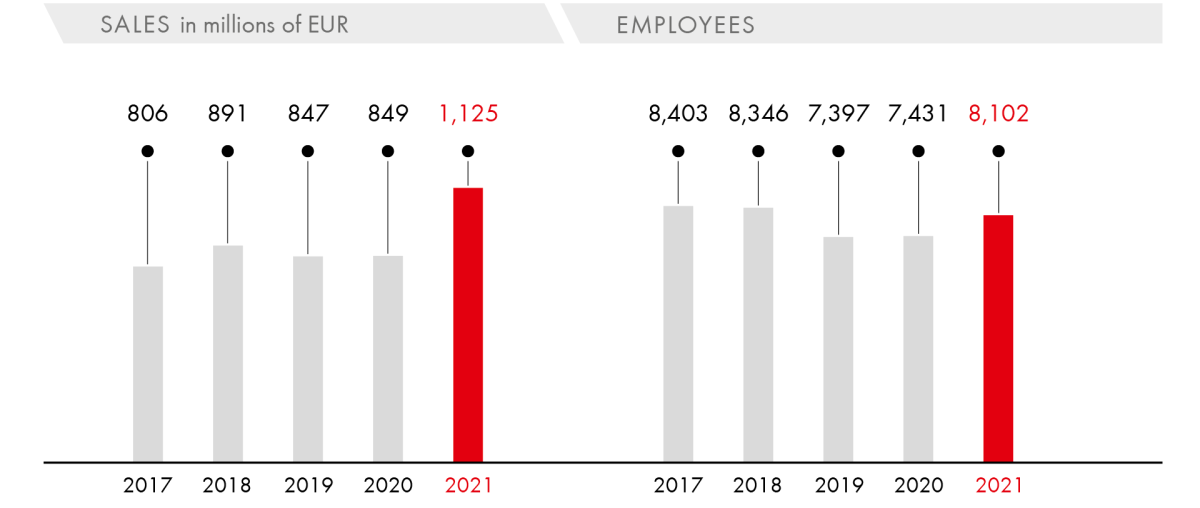
Production
The range in this business unit includes the production of cold-formed parts, forming and punching tools, a variety of fasteners and fastening systems, furniture fittings, plastic assortment and storage boxes, as well as factory and vehicle equipment. The business unit supplies a range of customers, including customers from the construction sector, the automotive industry, manufacturers of kitchens and household appliances, and wholesalers.
- Arnold Umformtechnik: Planning and acquisition of land to house the new site of the “Functional Components” business unit at Rauhbusch industrial estate in Forchtenberg finalized
- CO2 emissions cut by around 50 percent with the “Conform Next” product range thanks to new technology for complex formed parts
- Güldner: Installation of a photovoltaic system that covers 40 percent of electricity requirements
- FELO: Installation of the first fully automated injection molding cell for the production of screwdrivers using four components
- Europe-wide supply of OBI DIY stores: on-schedule execution of one of the biggest orders in the company’s history
- Grass Austria: Investments in the Höchst and Götzis production sites allow for process standardization
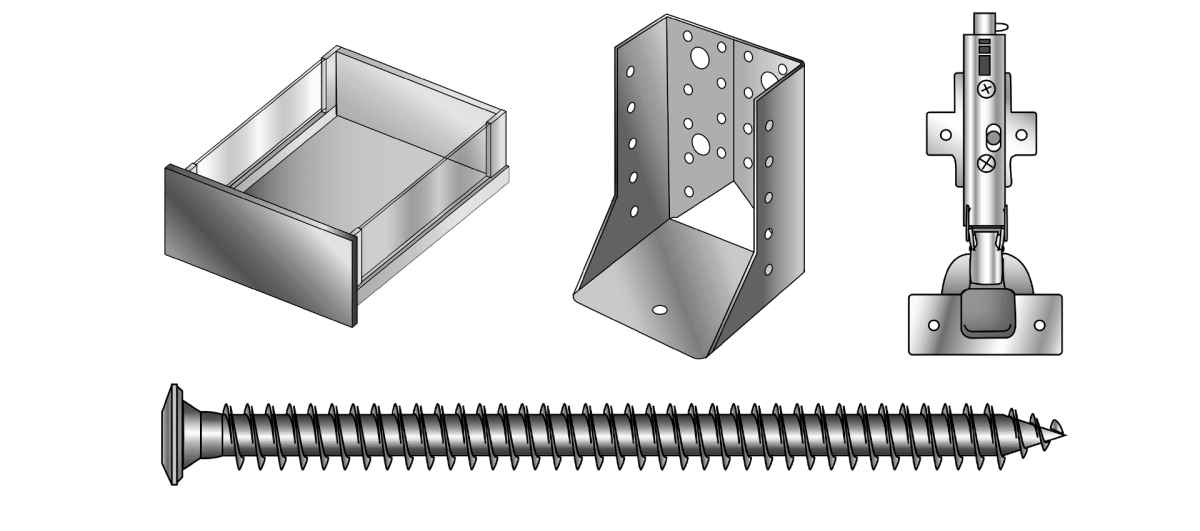
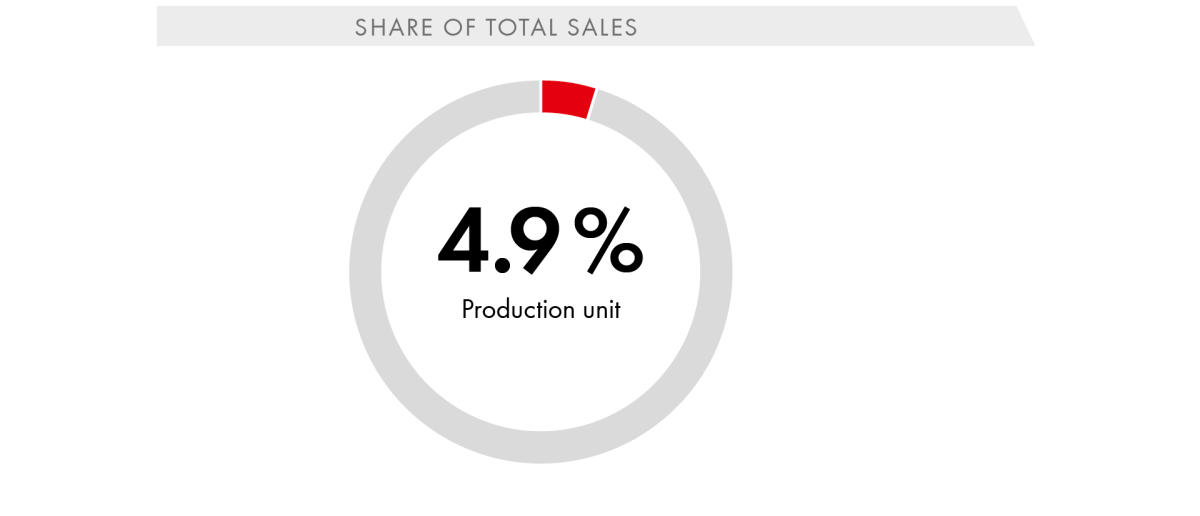

RECA Group
The RECA Group companies supply industry and, through direct selling, construction, wood, metal, and car business customers, as well as customers in the cargo sector, in 19 European countries. The company’s portfolio includes tools, assembly and fastening materials, C-parts, workwear, advertising materials, and vehicle equipment.
- Significant sales record of EUR 762 million
- Industrial business returns to double-digit sales growth after declining sales in 2020
- Services that help customers reduce procurement costs for small parts proved to be growth drivers during the COVID-19 pandemic, such as KANBAN and RFID-supported storage systems, the SECO® shelf management system (service concept) for trade customers, shelf and vending solutions for the direct retrieval of goods, and automated reordering systems.
- RECA companies are investing in digitalization and the expansion of e-shops, with e-business sales growing by 31.8 percent.
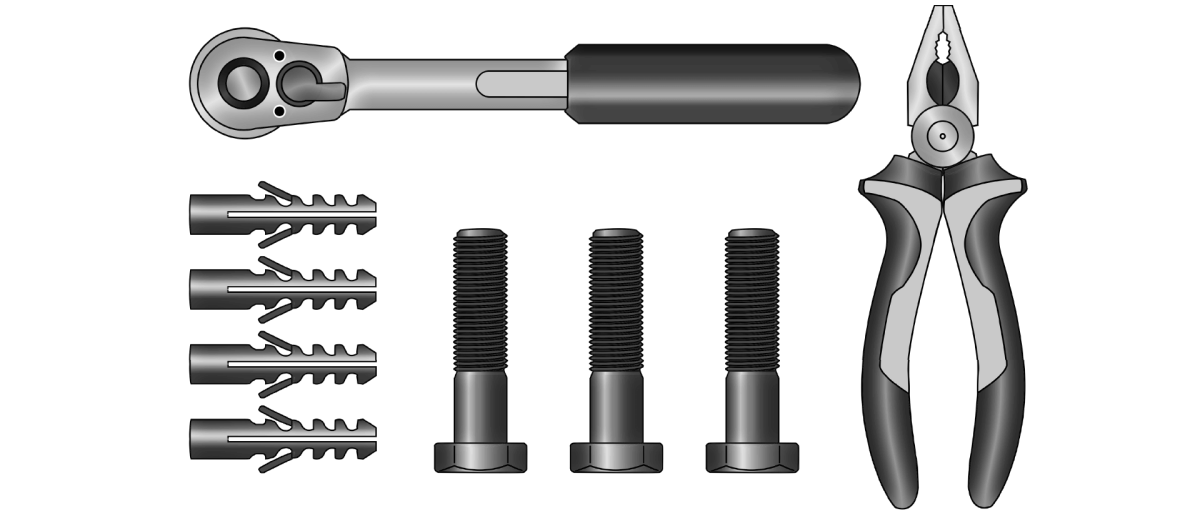
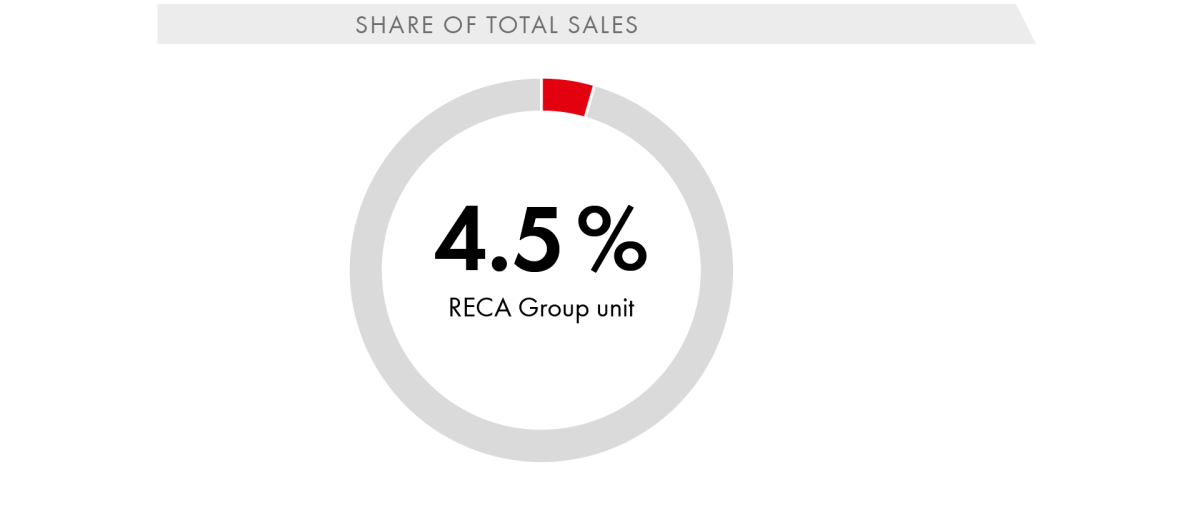
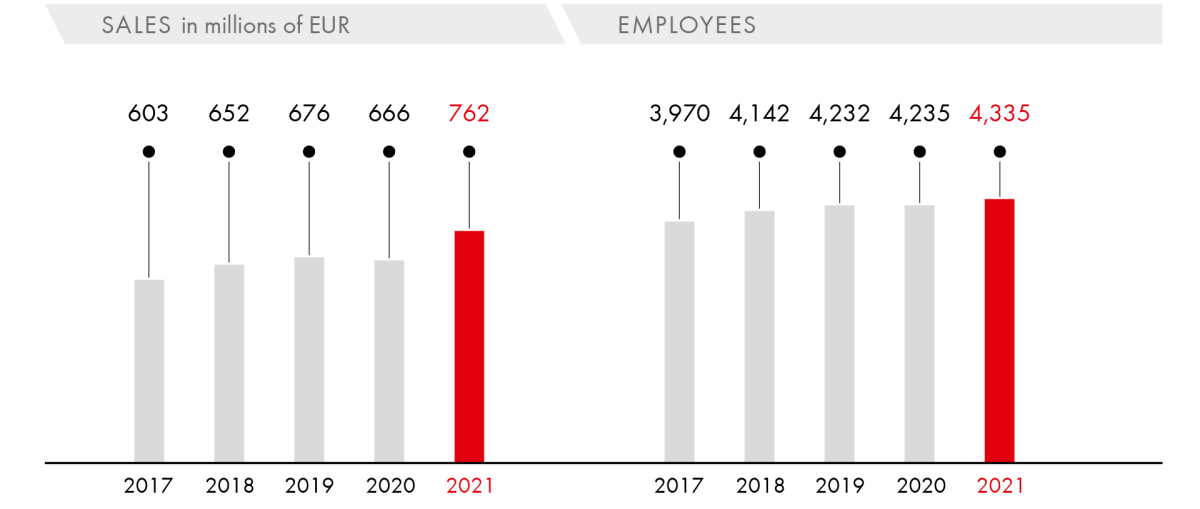
Chemicals
The companies in the Chemicals unit are responsible for the development, manufacturing, and distribution of chemical products for the automotive, industrial, and cosmetics sectors. They distribute both their own brands and private-label products and are renowned as innovation specialists and experts in their niche areas.
- Procurement market created challenges in 2021 due to major supply bottlenecks for solvents, aluminum cans, and specialty chemicals and petrol
- Increased raw material prices dominated the market
- Kisling, Dinol, Tunap: changing focus from direct to project sales
- Kisling: focus on the electronics market—development of potting compounds (casting resin) for electronics applications
- AP Winner China: Production permit valid until 2024 ensures further stabilization of the company
- Very positive outlook for 2022
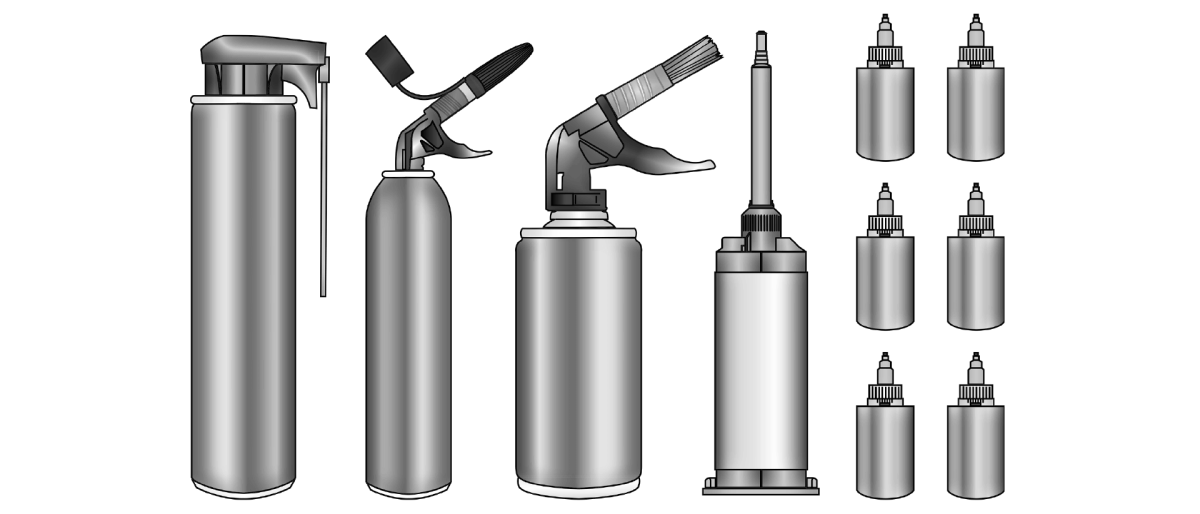
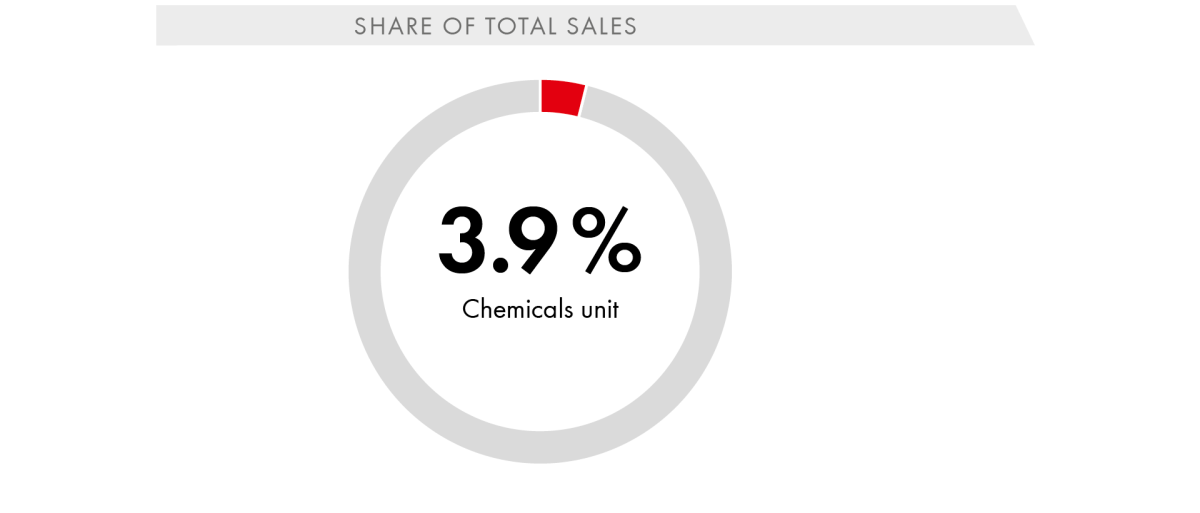
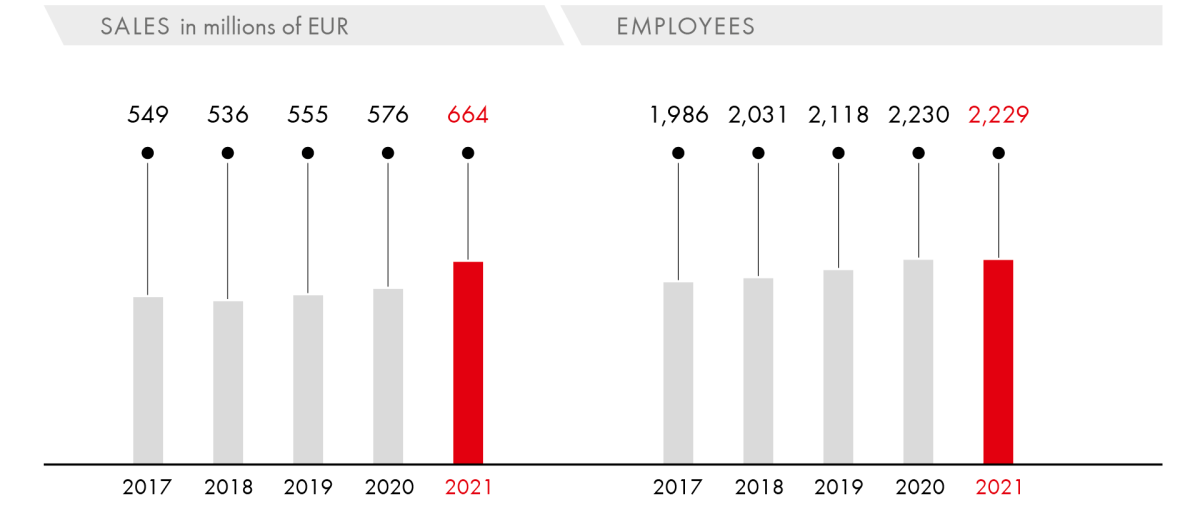
Trade
Companies in this business unit sell installation, sanitary, fastening and assembly materials, garden products, power tools, and hand tools. The range also includes furniture fittings for specialist stores and retailers, as well as products for DIY stores and discount stores.
- Pandemic-induced sales slump due to lockdown in early 2021
- After adjustments to reflect the sale of Arvid Nilsson Sverige AB, Sweden, in October 2020, the drop in sales came to 1.5 percent
- Commissioning of a new automated storage and picking system near Masidef in Italy
- Firstever customer placement of the newly developed “Find-it” all-in-one solution shelf: Procurement made easier thanks to option for finding products as part of an electronically controlled process
- Reduced packaging options in the interest of sustainability and stringent compliance with high environmental and safety standards based on customer specifications
- Further investments in IT infrastructure, forward-looking technologies, and electronic shelf labels
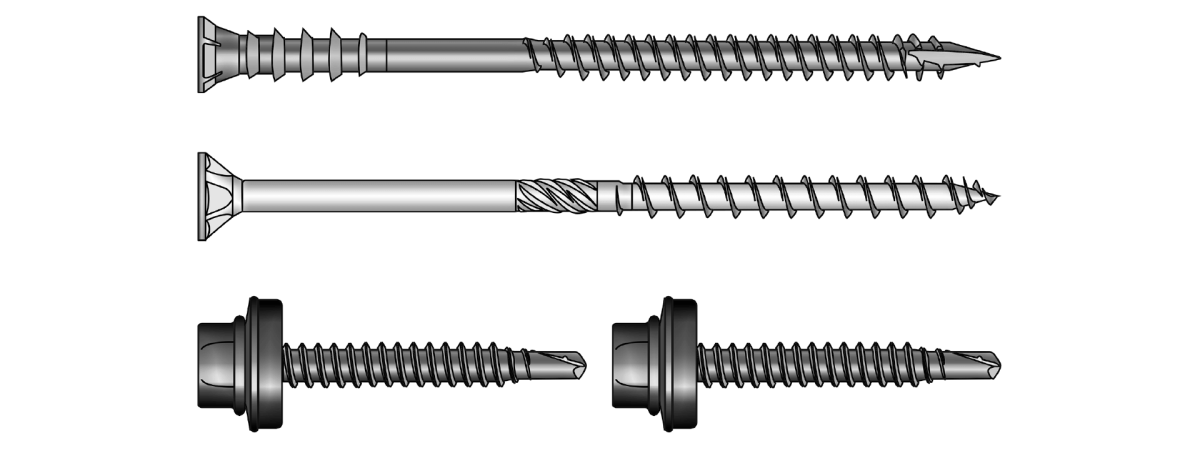
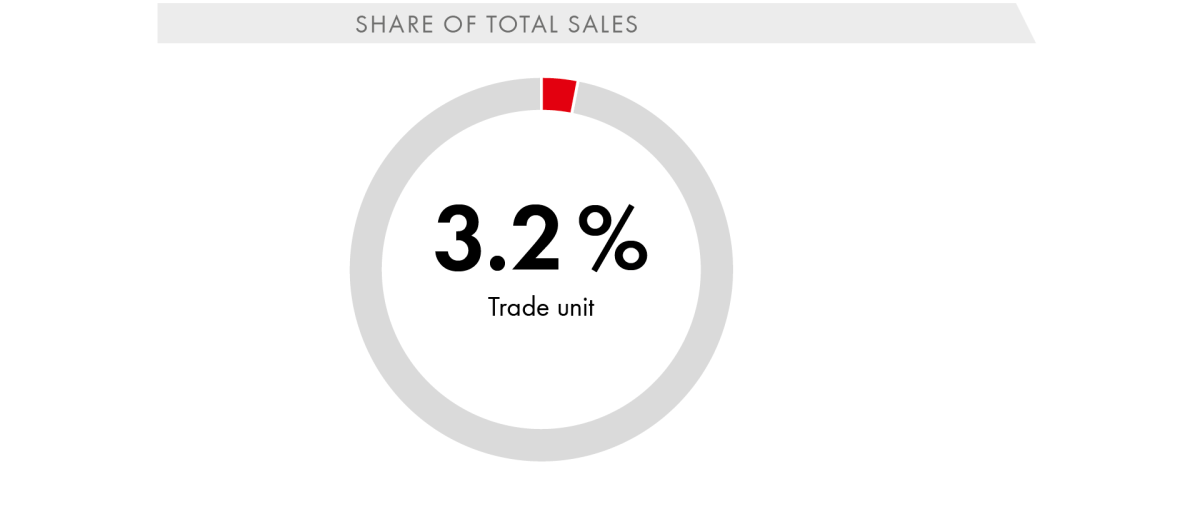
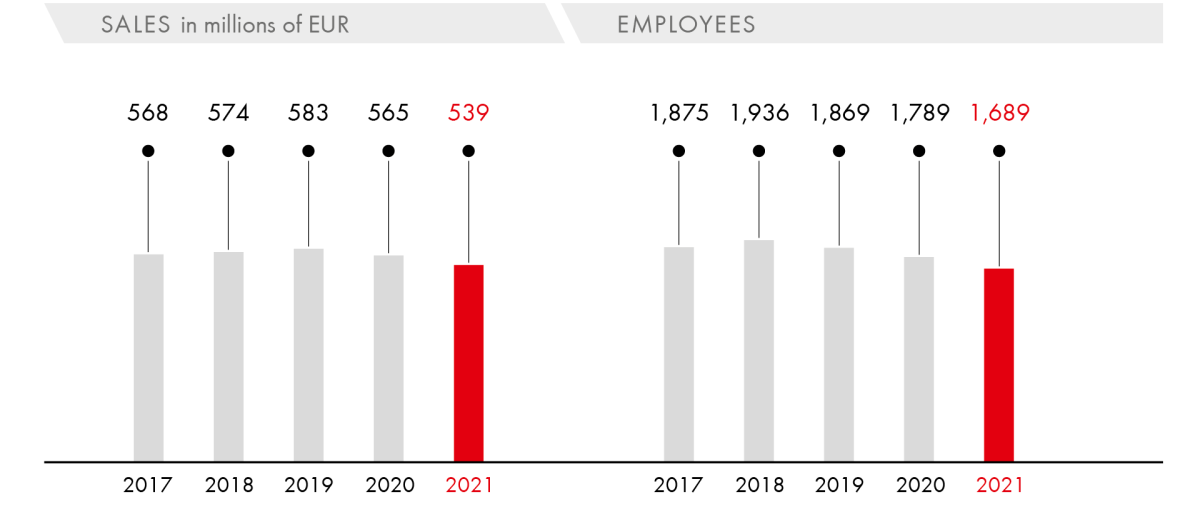
Tools
The tools companies supply customers in the metalworking and metal processing industries, particularly in the mechanical and plant engineering sector, and in the automotive manufacturing and automotive supplier industry. They sell products from the areas of drilling, milling, turning, clamping, grinding, testing and measurement equipment, hand tools, operating equipment, machinery, and personal protective equipment.
- Significant increase in order intake at companies in the mechanical and plant engineering sector and the automotive industry
- Lack of raw materials and semiconductors caused production backlogs
- E-business share increased by 3.0 percentage points to over 43 percent
- Development of expertise in process optimization for our customers’ machining production
- Continued focus on customer acquisition in the medical, food, transport and logistics, energy and environment, construction, and recreational vehicle sectors
- Expanded range of personal protective equipment products
- HAHN+KOLB: optimization of the logistics process through automatic carton packaging and expansion of the shuttle warehouse
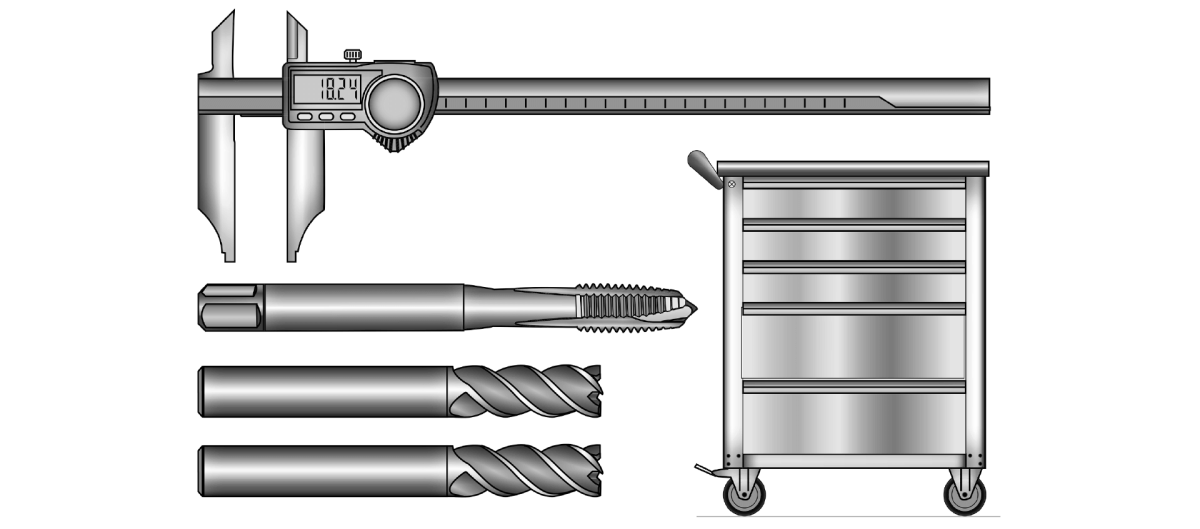
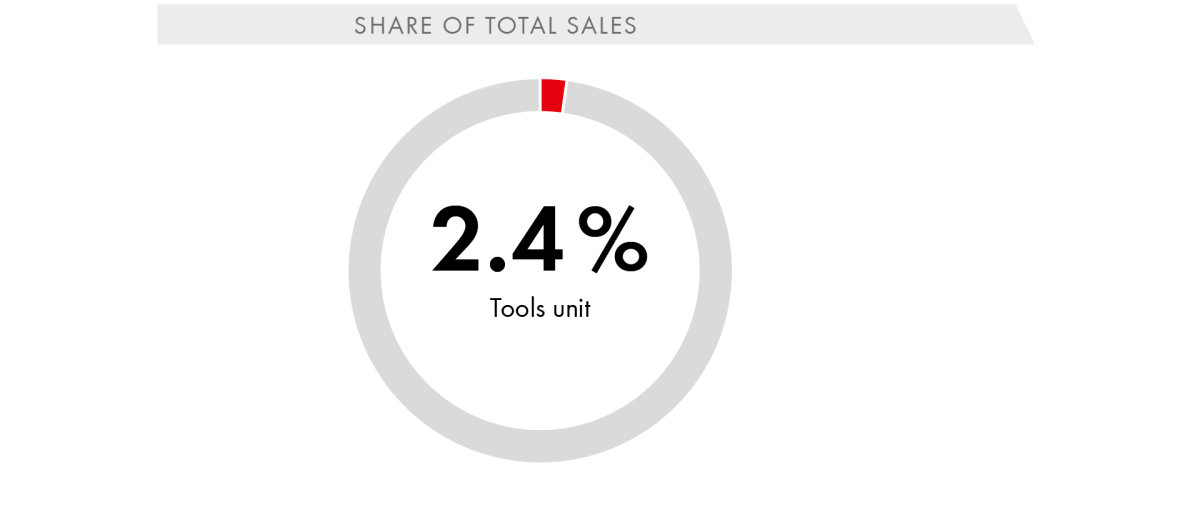
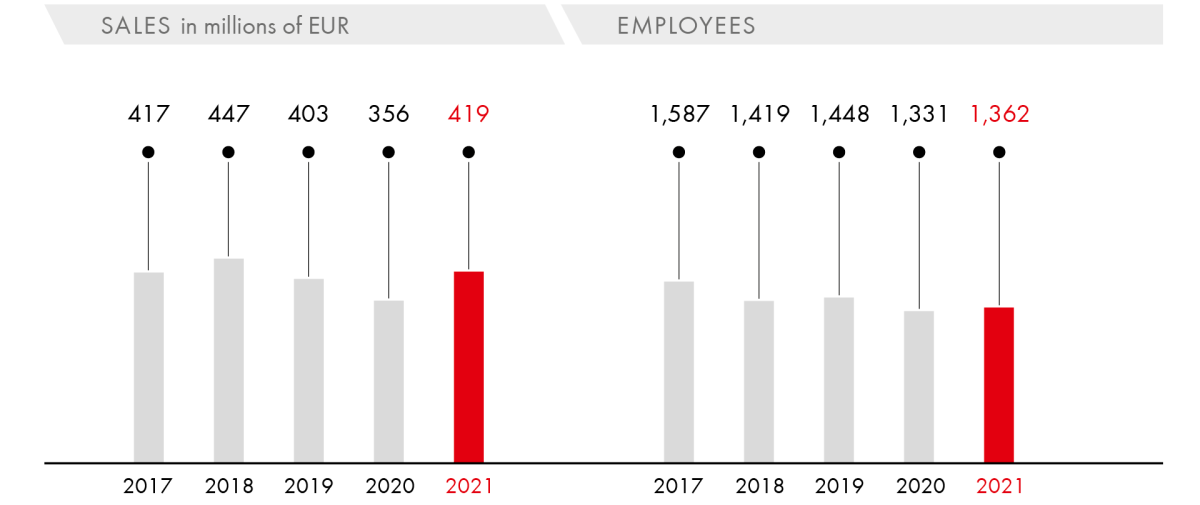
Screws and Standard Parts
The stainless steel companies are product specialists with supply concepts for industry and trade. The unit’s main business activity is the sale of stainless connecting elements, in particular DIN and standard parts. The hydraulic companies specialize in trading in hydraulic connection technology and providing the associated services.
- Marked increase in sales and operating result
- Focus on telemarketing: introduction of telemarketing tool for all stainless steel companies
- Difficulties in goods procurement due to COVID-19 pandemic
- Service sales reported by hydraulics companies bounced back in 2021 and returned to double-digit growth
- Trade also achieved double-digit growth in 2021 despite procurement problems and a marked increase in purchase prices
- HSR: focus on digital services
- Acquisition of CICMP in Austria supplements range of services to include series production of high-quality hydraulic hoses
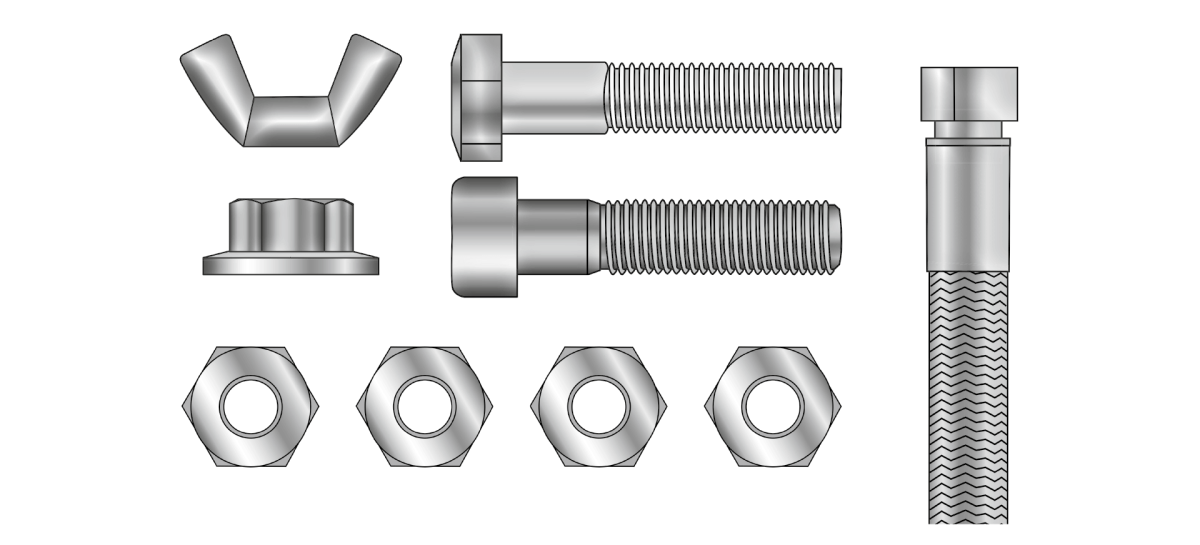
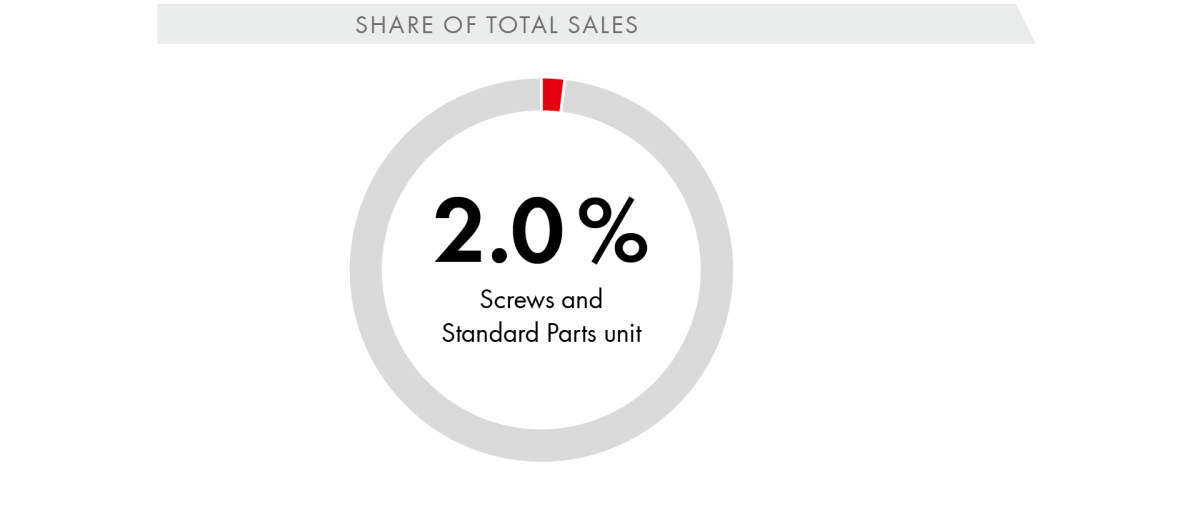
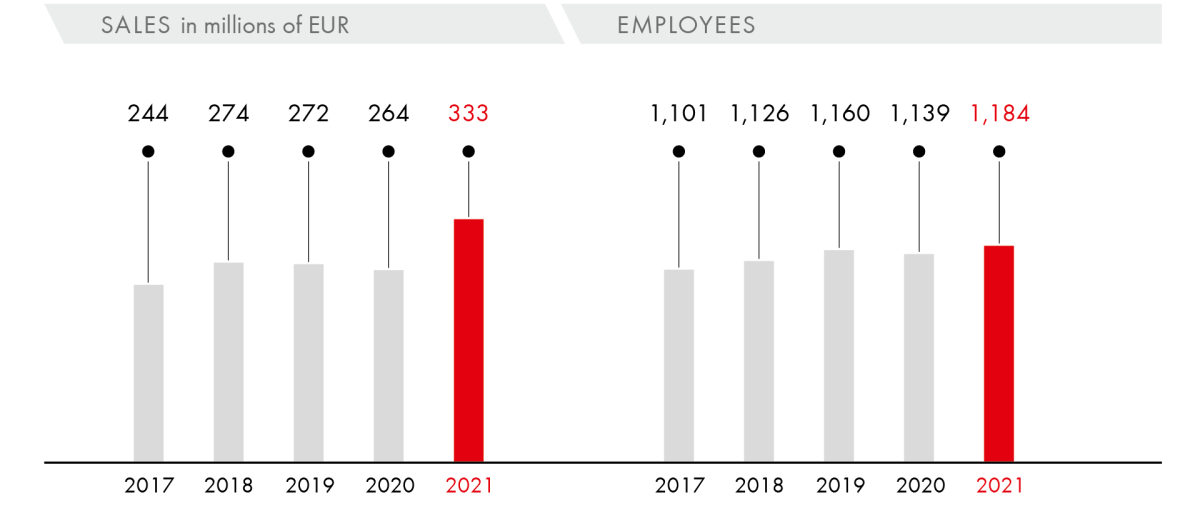
Financial Services
Security is a buzzword at the moment, especially in the financial sector. Thanks to its financial independence, the Würth Group offers this very security in all areas of financial services: financing, leasing, retirement plans, property and personal insurance, and asset management.
- IBB Internationales Bankhaus Bodensee AG: positive development again
- Innovation through technology: IBB expands digital private banking services with the help of a robo-advisor.
- Leasing companies record double-digit growth in new business volume and present value
- New Agrar Lease business unit launched successfully
- Waldenburger Versicherung: short response times thanks to direct customer contact with decision-makers
- Positive growth weakened by various severe weather disasters and associated high claims expenditure
- Further investments in digitalization, sales, and staff ensure future viability
- Navigating the COVID-19 crisis successfully: Würth Financial Services sets new sales record
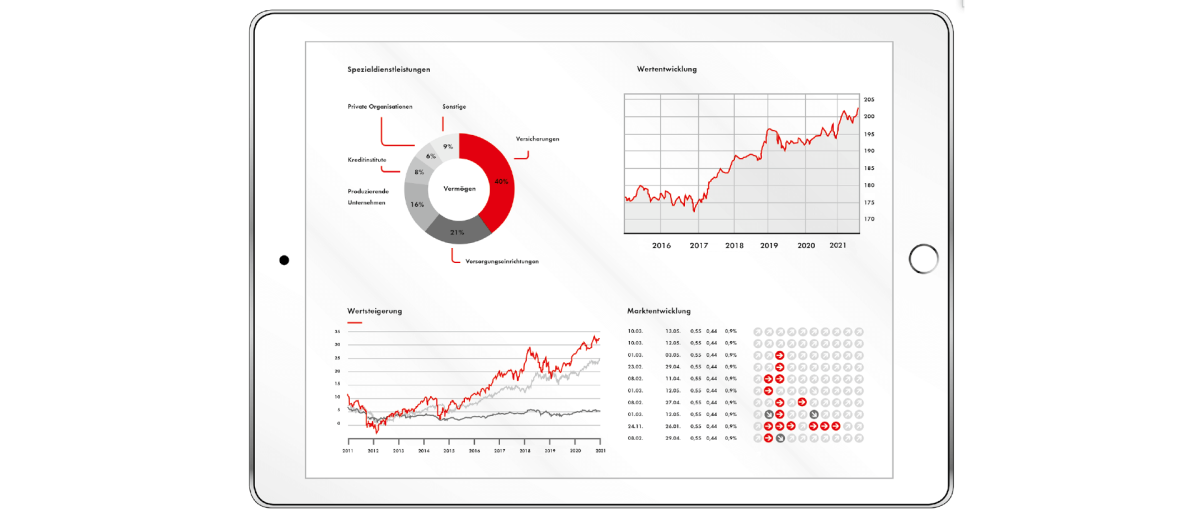
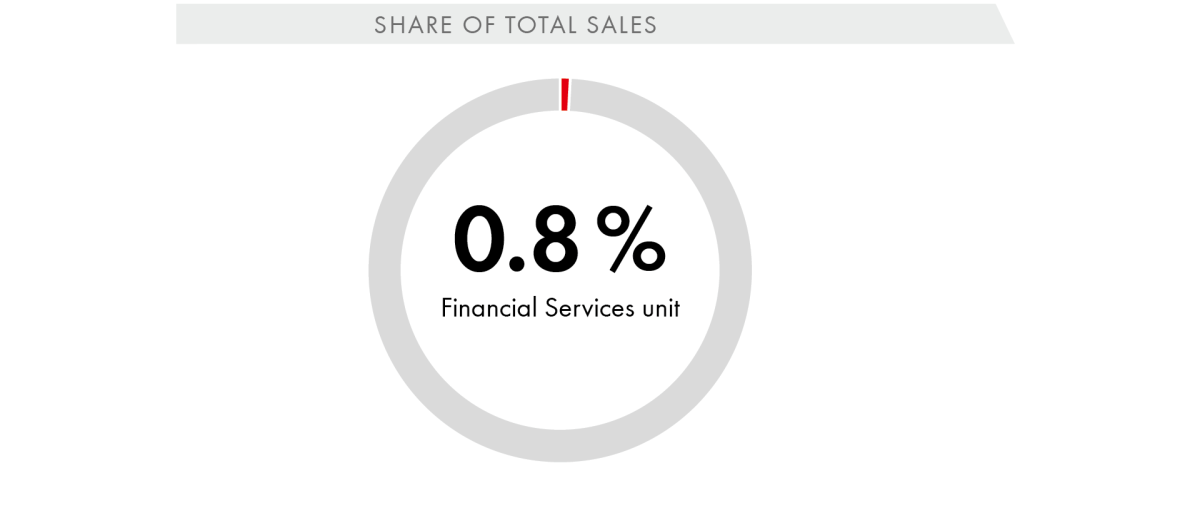
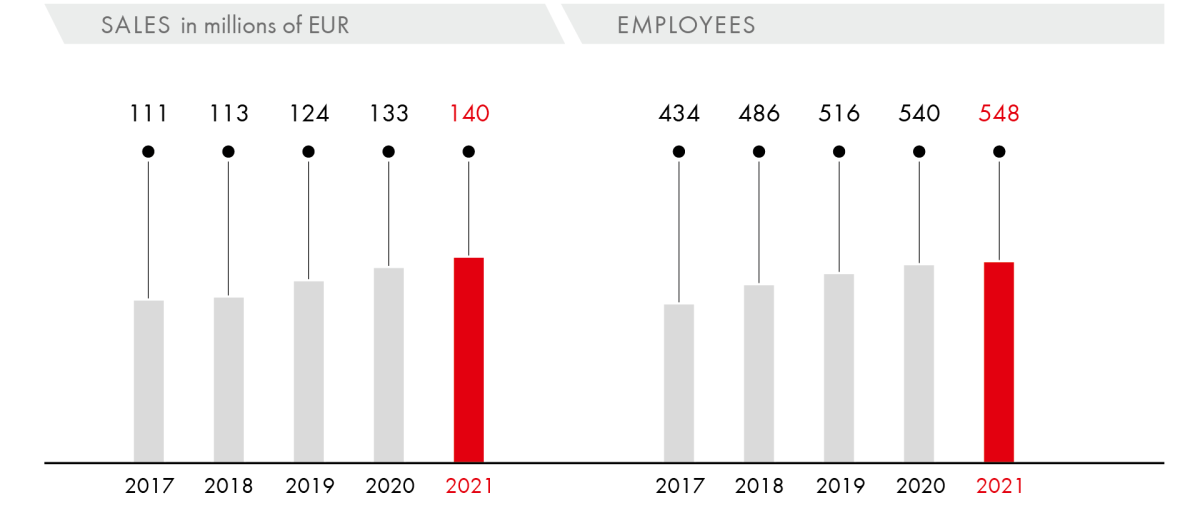
- Operating result up significantly
- Cash flow weaker due to inventory buildup
- in the second half of the year
- Equity ratio improves to 45.2 percent
In the past fiscal year, the Würth Group increased its operating result significantly to over EUR 1 billion for the first time. At EUR 1,270 million, it is up by 63.9 percent on the previous year (2020: EUR 775 million). Although sales also rose considerably by 18.4 percent, the return on sales improved to 7.4 percent (2020: 5.4 percent). We calculate the operating result as earnings before taxes, before amortization of goodwill, brands and financial assets, before the collection of negative differences recognized in profit or loss, before the adjustment of purchase price liabilities from acquisitions through profit or loss, and before changes recognized in profit or loss of non-controlling interests disclosed as liabilities.
The outstanding operating result was due not only to the significant increase in sales but also to the positive productivity trend. What is more, the pandemic meant that the costs incurred for travel, trade fairs, and conferences were minor in 2021. The Group’s own production plants in Germany and Europe ensure a certain degree of independence from global supply chains. Nevertheless, global supply bottlenecks also made themselves felt in individual areas of the Würth Group. The chip shortage, for example, had an impact on the companies in the Group that depend on the automotive industry. This development prevented an even more significant increase in earnings at companies trading in tools, within the Würth Elektronik Group, and at individual manufacturing companies.
In Germany, an operating result of EUR 639 million was generated in the fiscal year under review (2020: EUR 376 million). This equates to an increase of 69.9 percent. The very positive earnings performance is reflected in all business areas. The share of the Group’s overall result attributable to the German companies rose to 50.3 percent as a result, with the return on sales amounting to 9.2 percent (2020: 6.2 percent). With an operating result in excess of EUR 250 million for the first time, Adolf Würth GmbH & Co. KG made what was by far the biggest contribution to earnings within the Group. Other top performers within Germany include: Würth Elektronik eiSos, Würth Industrie Service, Fega & Schmitt Elektrogroßhandel, Uni Elektro Fachgroßhandel, and Reca Norm.
The companies outside of Germany boosted their operating result by 58.1 percent to EUR 631 million (2020: EUR 399 million). Here, too, the earnings growth is broad-based. Established companies in the Würth Line, Electrical Wholesale, Electronics, as well as stainless steel dealers, for example, showed that the measures taken to cope with the new challenges and the fundamental strategies adopted were once again effective in the second year of the pandemic. From a regional perspective, the operating result achieved in North America did not show satisfactory development. In particular, the procurement and transportation situation faced by industrial companies in the US dealt a blow to earnings. In addition, costs in connection with the consolidation of warehouse locations had a negative impact. While the past few years in the UK were hit by uncertainty surrounding Brexit, 2021 brought positive development in the operating result.

The ratio of cost of materials to sales was up on the previous year at 51.4 percent (2020: 50.4 percent). Material shortages and supply bottlenecks were the main reasons behind this increase. At EUR 96 million, other operating income was down only very slightly on the previous year (2020: EUR 110 million).
At the end of December 2021, the Würth Group had a total of 83,183 employees. This represents an increase of 4,044 employees and is the result of the deliberate decision not to make any structural staff adjustments during the COVID-19 pandemic. Person-to-person contact is the strength of our sales approach also, and particularly in times like the present. The sales force works closely with our in-house support departments. Employees were hired in both areas. The main focus of this recruitment, at +8.0 percent, was on internal staff and on the pick-up shops in particular, followed by colleagues working in logistics. The ratio of personnel expenses to sales was down on the previous year at 25.6 percent (2020: 26.7 percent), with improved productivity being one reason explaining this trend.
At EUR 776 million, amortization, depreciation and impairment losses were on a par with the previous year (2020: EUR 779 million). This reduces the ratio to 4.5 percent (2020: 5.4 percent). Amortization, depreciation and impairment losses include impairment losses on intangible assets, including goodwill, property, plant and equipment, and right-of-use assets amounting to EUR 68.8 million (2020: EUR 84.3 million), which were mainly incurred in the US industrial companies and in the Production unit. Amortization and depreciation were up by 1.8 percent on the previous year.
Other operating expenses rose by 12.6 percent compared to the previous year. The ratio was down on the previous year at 11.8 percent (2020: 12.4 percent). In addition to economies of scale related to sales growth, costs for conferences and travel were once again not incurred to the usual extent in 2021 due to the COVID-19 pandemic. Global mobility was still limited.
The tax rate increased in the 2021 fiscal year to 22.4 percent (2020: 19.9 percent). One key reason for this is a one-off tax refund relating to a different period in Germany in the 2020 fiscal year. Tax losses from the current fiscal year, where it was not reasonably certain that they could be used in subsequent periods, were not recognized in either fiscal year. For a detailed analysis, please refer to Section G. Notes on the consolidated income statement, [10] “Income taxes”, in the consolidated financial statements.
With sales in excess of EUR 17 billion and an operating result that surpassed the EUR 1 billion mark for the first time, the Würth Group set new records in 2021. The COVID-19 pandemic remains ever present. In the second year of the pandemic, the Group once again clearly demonstrated its performance with the diversification of risk resulting from its international positioning, diversification across various business areas, and its multi-channel strategy. The broad positioning of the Würth Group, which has proven to be relatively resistant to crisis, means that it is able to compensate for economic fluctuations in individual submarkets. We also benefited from the systemic importance of the area in which we operate.
Net income for the year increased considerably to EUR 965 million. Our gross profit, that is to say, sales minus the cost of goods sold, came under pressure due to developments on the global procurement markets. The staff turnover indicator deteriorated slightly compared with the previous year, which was to be expected in view of the improved economic conditions in our main core markets. In a long-term comparison over the last 20 years, staff turnover is at an acceptably low level, especially in the sales force. Productivity showed very positive development. All in all, the Central Managing Board is satisfied with developments in the past 2021 fiscal year. The targets set for sales and the operating result were surpassed.

Capital expenditures and cash flow
The year 2021 was extraordinary in many ways. Record figures were achieved in a large number of areas. The last time we achieved sales growth on this scale was in 2000. At that time, the millennium bug was the term on everyone’s lips and disaster scenarios were predicted in the run-up to the turn of the millennium in 1999/2000, which fortunately never materialized. In 2021, the coronavirus pandemic dominated large parts of life. As a result, we adopted a commercially cautious approach to capital expenditures despite the many records achieved. At EUR 553 million, capital expenditures excluding right-of-use assets under IFRS 16 were up by 16.9 percent on the level achieved in the previous year (2020: EUR 473 million). Growth is inextricably linked to the self-image of the Würth Group as a matter of principle. Growth by tapping into new markets and growth in existing markets require optimal underlying conditions. One of the ways in which the Würth Group achieves such conditions is through sustainable investment. Over the past ten years, the Group has invested more than EUR 5.0 billion in intangible assets and in property, plant, and equipment. All in all, investments in 2021 focused on the expansion of IT infrastructure and warehouse capacities for our distribution companies, as well as on production buildings and technical equipment and machinery for our manufacturing companies.
One example of the latter is SWG Schraubenwerk Gaisbach GmbH, the main supplier of wood screws for Würth. SWG acquired its largest electroplating service provider, based in Ellwangen, Germany, in 2020. This electroplating company focuses on surface coating screws ranging from 200 mm to 800 mm in length for the fast-growing “structural timber engineering” market. This segment plays an important role in our focus on sustainability. The existing capacity in the surface coating sector was only able to cover 50 percent of demand, and external resources are only available to a very limited extent in this segment. The successful integration of the acquired electroplating company involved developing a concept for the future. The objective is to double the electroplating capacity within the next two years. The structural extension for the innovative and sustainable timber construction activities is being planned by SWG’s in-house engineering department. The investment volume is forecast to come to around EUR 17 million.
With sales of EUR 467 million including intra-Group sales in the 2021 fiscal year, 1,829 employees at 19 locations and more than 200 sales partners in 60 countries, GRASS is one of the world’s leading specialists for motion systems. GRASS slide and drawer systems, hinge, flap and corner cabinet systems are branded products that move the furniture of renowned furniture brands. Trend-setting product developments are part of the company’s self-image. As a result, the past fiscal year saw the company make further investments in its “concealed drawer slide systems” product family, which includes both slides and drawers, to the tune of around EUR 11 million. Extremely narrow frames in particular can be created as a result of the investments. Thus, GRASS is following the trend toward minimalist designs and luxury materials extending even into the interior of the furniture.
In addition to the Allied Companies, the Würth Line companies also made substantial investments in stepping up their sales activities.
Würth Industrie Service GmbH & Co. KG entered into the most comprehensive investment in its company history at its central location for European industrial supplies in Bad Mergentheim. With a workforce of more than 1,700 employees, the company specializes in meeting the C-part requirements of manufacturing industrial customers and provides end-to-end support for more than 20,000 customers. As a system supplier, Würth Industrie Service offers its customers tailored procurement and service concepts. Planning for the further development of the site, with a clear focus on the integration of highly available automated and digitalized systems, began back in 2017 and was finalized in 2021 with operational commissioning and a total investment volume of EUR 165 million. In addition to a new shuttle warehouse featuring 195,000 container storage bins, the existing logistics complex was expanded to include 10,000 square meters of logistics space on a total of four levels. In the first stage, the location houses ten multi-purpose goods-to-person workstations, six robots for picking and palletizing, and a handling area for system-based goods receiving and shipping.
The successful growth of the Würth company in Croatia created a need for the company to build its own administrative and warehouse building. In Veliko Trgovišće, a suburb of Zagreb, new premises have been under construction since August 2020 and will be ready for occupancy in the first quarter of 2022. The new logistics building, which spans an area of 6,500 square meters, brings together several warehouses in a central location, significantly simplifying the complexity of logistics processes and improving customer service. The new office building, with an area of around 5,000 square meters, offers employees modern workstations with ample daylight, a company restaurant, and appropriately equipped premises that provide optimum support for creative and collaborative work. The total amount invested in the new buildings will come to around EUR 15 million.
In addition to investments in production and storage space, we have also, as in previous years, invested in our ORSY® storage management system, which offers our customers storage and provision options for various consumables and supplies in line with their needs.
A total of 45.8 percent of the total investments were made in Germany (EUR 253 million). This reflects how important the domestic market continues to be for the Würth Group.
The investment controlling system, which has been further refined in recent years to feature sophisticated recording and detailed evaluation options, allows the Central Managing Board to respond to any changes that emerge at very short notice and to adapt to new underlying conditions at any time of the year. The regulation adopted in the course of the COVID-19 crisis in 2020 limiting approvals for investment amounts was lifted again in the course of 2021 once it became apparent that the Würth Group’s stability and liquidity were sufficiently secured. In 2021, the Würth Group once again remained true to its approach of financing investments in intangible assets and property, plant and equipment entirely from its operating cash flow. Our cash flow from operating activities came in at EUR 1,034 million (2020: EUR 1,600 million). This represents a decrease of 35.4 percent year-on-year, which is mainly due to an increase in inventories in the second half of 2021 despite the increased result. This, in turn, bears testimony to the company’s prudent management of resources: The tense shipping container capacity situation prompted the company to build up safety stocks in order to ensure that it could continue fulfilling orders. The increase in trade receivables also contributed to the decrease.
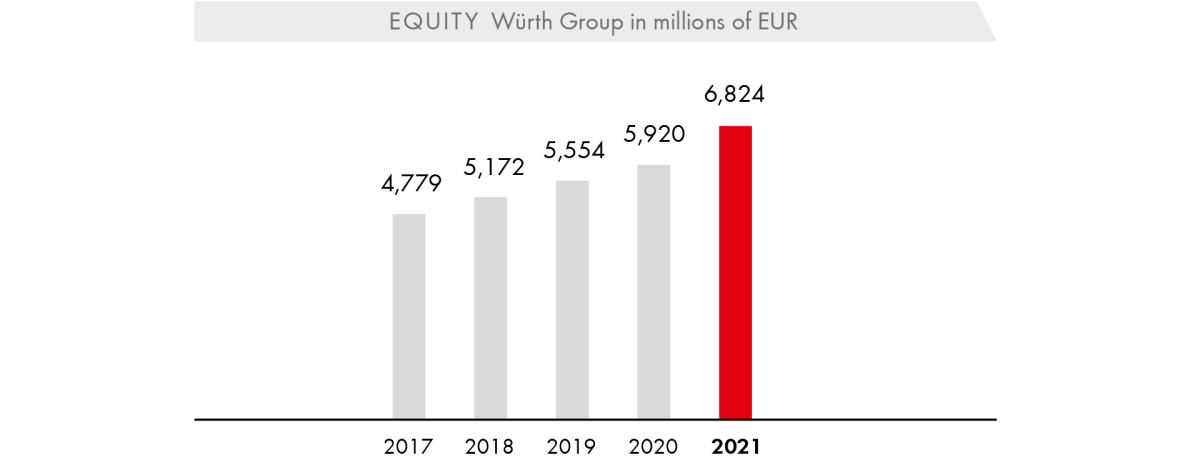
Purchasing
The ongoing raw material shortages in 2021 put the brakes on global production. This was also reflected in the purchasing managers’ indices for Europe and Germany. At the end of December 2021, the indices stood at 58.0 points for the eurozone and 57.4 points for Germany. This means that the purchasing managers’ index for Germany fell considerably in December 2021 for the fifth month in a row, and in Europe for the sixth month in a row. These values were more than eight points below the July 2021 value (65.9) in Germany and more than five points below the June 2021 value (63.4) in the eurozone. Nevertheless, the purchasing managers’ indices remained above the 50-point expansion threshold. This suggests that leading buyers in this economic area expect to see positive market developments. In China, the value rose to 50.9 points in December 2021. In the US, unlike in Europe and Germany, it climbed to 61.1 points between July and November 2021. In December 2021, however, the US value also fell to 58.7 points, marking a low point for this economic region in 2021.
The situation for the Würth Group’s buyers in 2021 was a very challenging one. The COVID-19 pandemic and the lockdowns imposed in response to the pandemic in a large number of countries meant that many of Würth’s suppliers had to stop production in some cases, resulting in massive delivery delays, capacity bottlenecks in production and, as a result, considerable price increases and availability problems for end products. On top of this, China developed ambitious CO2 reduction targets. In September 2021, for example, the Development and Reform Commission of China’s Yulin county in Shaanxi province announced that energy consumption would have to be reduced. Magnesium producers and suppliers from the chemical-technical sector in particular have been left grappling with the consequences of this measure. They have had to drastically reduce or even completely stop their production. This not only pushed the prices for these products up; massive supply shortages are also anticipated on the horizon.
Furthermore, almost all commodity indices rose to exorbitant levels. This means that the Würth Group is still faced with significantly higher purchase prices in many product groups and that many companies are being hit by delivery problems on a huge scale. Central Purchasing liaises with the price management team on a daily basis in order to be able to reflect these price increases in the company’s sales prices. In addition to rising costs, particularly for raw materials, the biggest challenges at the moment relate to disrupted supply chains, which are leading to freight bottlenecks and supplier failures.
The euro/dollar exchange rate was also heavily influenced by the pandemic in 2021. Whereas the dollar was still trading at USD 1.226 per EUR at the beginning of 2021, the companies in the Würth Group had to contend with a drop in the exchange rate to USD 1.132 per EUR for their imports at the end of the year.
The situation on the global procurement market remains chaotic. For example, the market outlook for sea freight shows that further port or terminal closures and quarantine restrictions are very likely. These will cause additional delays and have a negative impact on the freight market. Another challenge for 2022 will lie in the drastic price increases witnessed in 2021 as a whole, as well as further calls for price increases from the Würth Group’s upstream suppliers, which will put considerable pressure on gross profit.
Inventories and receivables
As a company with international operations, the Würth Group’s inventories and receivables are key balance sheet items that the company’s management is continually seeking to manage and optimize. The mounting difficulties in procuring goods played a major role in inventory management in the past fiscal year. On the one hand, the procurement process was affected by the sharp rise in freight prices and, on the other, we had to contend with supply bottlenecks in a number of areas, including silicones and solar substructures. It was foreseeable at the very beginning of 2021 that delivery capability would be a decisive success factor. In order to ensure continuous supplies to our customers, we took the conscious decision to increase inventories by purchasing safety stocks. Despite enormous efforts, the service level decreased somewhat over the course of the year and stood at 94.2 percent in December 2021, meaning that, for every 100 items ordered, 94 were delivered to the customer the next day. Irrespective of this development, stepping up our inventory control measures was a key focal point of 2021, and the Würth Line’s Central Purchasing department pushed ahead with projects to streamline the range of products on offer in cooperation with Product Management. The permanent objective is to eliminate products with very low demand.
In retrospect, it became clear that increasing inventories was exactly the right precautionary measure, because alongside sales, logistics is a central element within the Würth Group. Without the targeted measures to build up inventories, it would never have been possible to achieve the above-average sales growth of 18.4 percent. All in all, the Würth Group’s inventories increased to EUR 3,064 million (2020: EUR 2,222 million), up by 37.9 percent on the previous year. Stock turnover, calculated on a 12-month basis, nevertheless increased from 4.6 times at the end of 2020 to 4.9 times at the end of 2021.
Lockdowns, border closures, the blockade at the Suez Canal, and the associated supply chain interruption and shutdown of entire production plants all played a role in the 2021 fiscal year, accompanied by fears of an increasing number of corporate insolvencies. Massive bad debt losses, or at least delayed payments, were to be expected, and our focus was on closely monitoring the development of receivables. In this situation, too, the Würth Group was able to rely on its established sophisticated controlling systems, which allow the Group to take fast action in response to any undesirable developments that may emerge. Thanks to extremely efficient interaction between sales and receivables management, the Group succeeded in keeping the increase in trade receivables by 22.4 percent to EUR 2,376 million at a manageable level (2020: EUR 1,942 million). This increase can be traced back primarily to the very positive sales performance in the fourth quarter. The level of receivables in relation to sales, however, showed positive development. At 52.5 days, the collection days key figure (based on a 12-month calculation) was lower than the figure for 2020 (53.0 days). An excellent result was achieved in Germany, in particular, with 40.2 days (2020: 40.0 days).
We will continue to optimize accounts receivable by means of effective cooperation between sales and accounts receivable management, as well as by refining our analyses. We see the payment patterns of debtors as critical in Southern Europe, China, the Middle East, and India, as they can slow growth.
The percentage of bad debts and the expenses from additions to value adjustments related to sales fell slightly to 0.4 percent (2020: 0.6 percent).
Financing
The Würth Group’s equity increased to EUR 6,824 million last year (2020: EUR 5,920 million). This equates to an increase of 15.3 percent. This increase of EUR 904 million lifted the equity ratio to 45.2 percent (2020: 43.8 percent), putting it at a very good level for a trading company. For years, a good level of equity capitalization has been the basis for consistently high levels of financial stability and the solid financing of our group of companies, strengthening customers’ and suppliers’ trust in the Würth Group. This is due to the typical family business approach of reinvesting a large portion of profits in the company. The high level of equity financing allows the company to be largely independent of external capital providers, which is a must particularly in times of crisis.
Total assets rose by EUR 1,636 million to EUR 15,114 million (2020: EUR 13,478 million). The increase of 12.1 percent is due primarily to the increase in inventories and receivables. Financial service activities also contributed to the growth in total assets. Refinancing in the banking sector was mainly achieved via customer deposits and financial intermediaries, as well as via the European Central Bank, while refinancing in the leasing segment was achieved mainly through the ABCP (Asset Backed Commercial Paper) program created especially for this purpose, a global loan program launched by the German state-owned development bank KfW, as well as through non-recourse financing and internal funds.
The Würth Group has undergone an annual rating process for more than 25 years now. The leading rating agency Standard & Poor’s once again confirmed the Würth Group’s “A /outlook stable” rating in June 2021. This rating reflects the confidence that business and the financial KPIs will continue to develop successfully, even in the environment created by the pandemic. The outlook for the Würth Group is viewed in a positive light. Our long history of good ratings not only documents the positive credit rating. At the same time, it is proof of the continuous and successful development of our corporate group and the stability of our business model.
At the end of the 2021 fiscal year, the Würth Group had three bonds issued on the capital market. The USD 200 million private placement, which bears interest at a rate of 4.48 percent, was redeemed on 22 September 2021, and the 1 percent bond due in May 2022 was redeemed early using the company’s own funds on 21 February 2022. Further bonds of EUR 500 million and EUR 750 million will mature in 2025 and 2027 respectively. This means that the maturities are well spread out. For further details, please refer to [27] “Financial liabilities” in Section H. Notes on the consolidated statement of financial position, in the consolidated financial statements.
The Würth Group has sufficient liquidity reserves. As of 31 December 2021, cash and cash equivalents came to EUR 1,217 million (2020: EUR 1,386 million). Net debt fell to EUR 567 million as against EUR 601 million in 2020. In addition, the Group has a fixed undrawn credit line of EUR 400 million provided by a syndicate of banks until July 2023. As a result, the Würth Group continues to have extremely generous financial resources at its disposal, giving it the leeway it needs to act.
As a company with global operations, the success factors of the Würth Group are, first of all, a strong sales force and state-of-the-art logistics facilities. Second, the company’s competitive edge is driven by product innovations and services geared toward these innovations. In the 2021 fiscal year, for example, Adolf Würth GmbH & Co. KG generated more than one fifth of its sales with products that are no more than three years old.
For more than 30 years now, Würth has been investing in research and development with the aim of further expanding its expertise as a leading manufacturer of fastening technology for professional applications. At Würth, innovations are born out of the daily challenges faced by our customers. It is not just about making individual products available, but about providing comprehensive service and systems that offer real added value. Würth sees itself as a consultant and problem solver that allows its customers to devote their full attention to their work.
In order to achieve this aim, Würth is bringing together employees from product development and science, as well as users from industry and trade, in the new innovation center on the Gaisbach campus. Starting in the third quarter of 2022, a total area of 15,000 square meters will be home to around 250 employees from the product development and materials testing departments of Adolf Würth GmbH & Co. KG and from Group subsidiaries operating in the manufacturing sector, as well as external researchers, for work on product and system innovations. Cooperation with scientists from the Karlsruhe Institute of Technology KIT, as well as the University of Stuttgart and Reinhold-Würth-Hochschule of Heilbronn University of Applied Sciences on the Künzelsau campus, will create a cluster of specialized knowledge and application expertise.
Würth aims to shorten innovation cycles and establish highly competitive systems with added value on the market. The focus of the company’s research and development work is on Würth’s fields of expertise: connection technology, screws, anchors, chemicals, power tools, and systems.
In these endeavors, the company’s R&D staff already rely on state-of-the-art technology and their own certified fastening technology laboratory. The relevant environmental concerns are cross-checked in climate chambers. Thanks to the additional large-scale climate chambers installed in the new innovation center, it will be possible to test elements of relevant components even faster in the future.
The innovation center will also expand the IoT laboratory for digitally networked products. The existing PowerTools laboratory will be expanded as well. Power tools, which are adapted to suit Würth’s tools and our customers’ applications, allow our customers to be more productive.
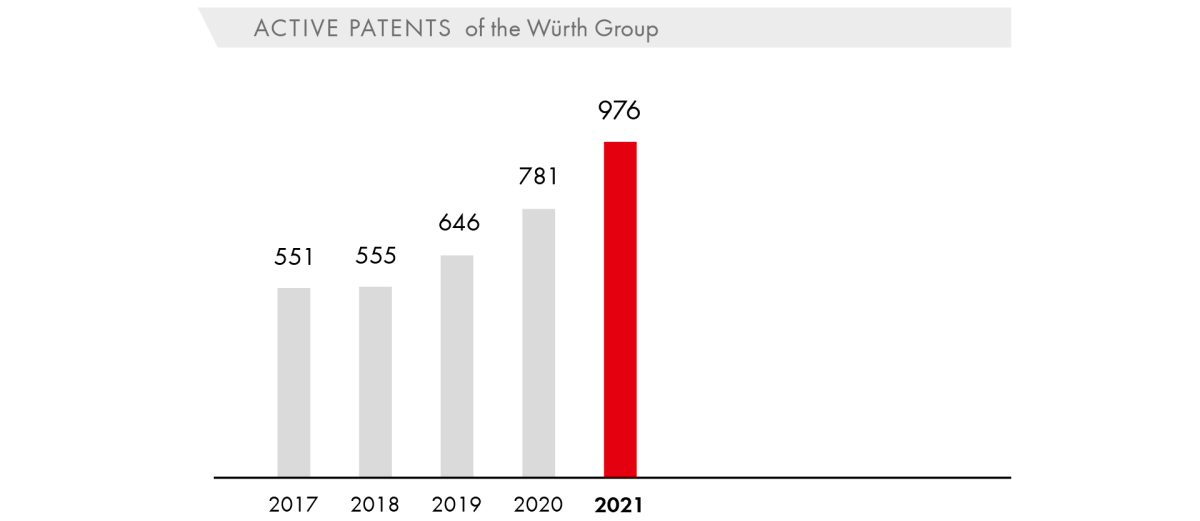
Innovations are a top priority throughout the Group. At present, the Group has 976 active patents, three utility models, 1,161 registered designs, and 8,009 active brands. The following are two forward-looking products that serve as examples of the wide range of innovations from the Würth Group:
Würth Line: Adolf Würth GmbH & Co. KG
M-CUBE® cordless power tools allow for maximum performance and freedom at work
Würth has been developing its in-house M-CUBE® cordless platform since 2018, with developments also taking account of customer experience. Würth’s M-CUBE® cordless power tools offer maximum freedom at work and are used with a uniform battery and charger.
The battery packs are available in 12 volt and 18 volt voltage categories. The outer rubber coating of the battery pack provides a safe and non-slip stand, as well as shock resistance for professional use. Special battery management ensures maximum performance and a long service life. The integrated cell frame offers the cells a firm fit and protects the battery against overheating and vibrations. An LED battery indicator shows the remaining battery level.
Würth will be expanding its research and development over the next few years in order to be competitive in the areas of cordless and charging technologies, as well as IoT, in addition to the power tools segment. The aim is to cover all relevant applications and customer requirements using Würth’s in-house M-CUBE® cordless platform and to offer a comprehensive platform solution with extensive service packages.
Allied Companies: Würth Elektronik CBT
Quantum magnetometer for more precision technology
Something that comes easy to migratory birds is considered a crucial capability for the industry of the future: The animals navigate their flight routes with extreme precision using their magnetic sense. As research suggests, their internal compass is based on subtle quantum effects in the eye on a tiny molecule on the retina.
The use of futuristic technology to measure magnetic fields is currently one of Würth Elektronik’s research topics—in its capacity as a development partner in the joint “Quamapolis” project launched by the Federal Ministry of Education and Research (BMBF). The project coordinator is Robert Bosch GmbH. Other participants include Q.ant GmbH and the Universities of Stuttgart and Ulm.
The focus is on quantum-based measuring systems that are expected to outperform conventional sensors. Within the electronics industry, localization with this level of accuracy opens up new opportunities, for example, for positioning and localization in smart systems, for the further automation of processes in the context of Industry 4.0, for smart homes, and for robotics applications in the healthcare and smart agriculture sectors. In the household sector, applications include parking assistance in cars or in automatic lawnmowers, for example.
The common goal pursued by industry and science for the project is to invent a novel sensor technology based on quantum effects that is ready for production. Würth Elektronik CBT is supporting the integration of the microoptical quantum sensor modules into the printed circuit board, as well as the development and provision of smart concepts to dissipate the heat generated from the system.
As a globally active company, the Würth Group is constantly exposed to risks, but also makes systematic use of opportunities that present themselves. Opportunities and risks can arise both as a result of our own actions or failure to act and as a result of external factors. The risk and opportunities policy of the Würth Group is aimed at meeting the company’s medium-term financial objectives and at ensuring the sustainable, long-term growth of the Group. In order to ensure this, the Würth Group has a system that identifies entrepreneurial opportunities and risks, assesses them using a standardized system, weighs them against each other, and communicates them. Our conscious and systematic approach to addressing opportunities and risks is inextricably linked to our entrepreneurial activities.
How the risk management system works
The Würth Group has a three-tier risk management system (RMS), comprising the cyclical monitoring system of the Auditing Department, the Group Controlling Department, and the early warning system. The Central Managing Board of the Würth Group holds overall responsibility for the Group-wide risk management process and defines the principles of our risk policy and strategy. The management of each company within the Group is responsible for installing a functioning and efficient RMS for themselves. They are supported by the risk manager, who reports directly to the Central Managing Board of the Würth Group and coordinates the risk management process at the Group level. The risk manager remains in close contact with the risk controller of the Advisory Board, who reports directly to the Chairwoman of the Advisory Board.
How the internal control system for financial reporting works
The aim of the internal control system for financial reporting is to ensure that all business transactions are completely recorded and correctly evaluated in line with the financial reporting requirements.
The Würth Information System is an integral component of the internal control and risk management system of the Würth Group. With the help of this reporting system, all key performance indicators required to steer the Würth Group are presented in a timely manner and are available for further evaluation by the Central Managing Board and Executive Board, based on standardized monthly reporting.
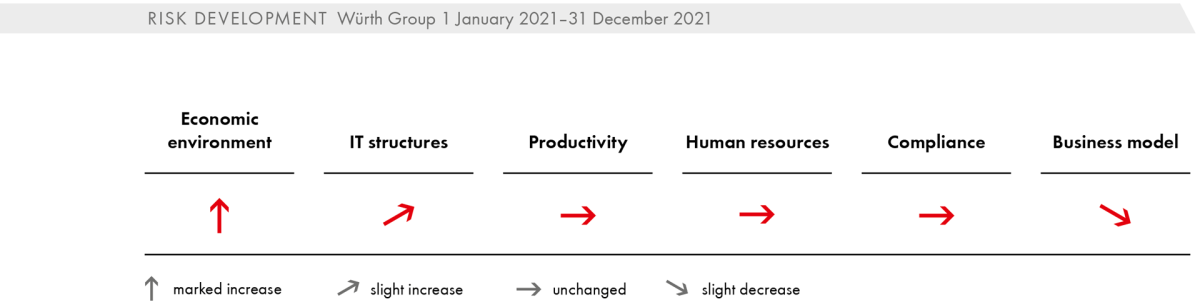
System-based control mechanisms such as validation and cross-checks optimize the quality of the information as a basis for decision-making. A Group-wide record of the financial statements of the Group entities, combined with monthly reporting, is not only efficient, it also avoids carry-over errors, safeguards the uniform provision of information, and includes numerous plausibility checks, without which the information cannot be forwarded. Standardized external and internal reporting also helps to ensure that financial reporting changes are implemented in a uniform manner across the Group. Changes to the data recorded are documented using check digits and authorized by a corresponding system of IT access rights. Standard software is used for consolidation. Changes in the system settings are logged centrally. The monthly and annual financial statements of Group companies are subject to regular automated assessment mechanisms, as are the consolidated financial statements. Moreover, Würth’s Policy and Procedure Manual (PAP) contains internal procedural instructions. Internal publications and training include detailed rules on financial reporting, compliance with which is regularly reviewed by the Auditing Department. External specialists are consulted to clarify the implications of legal and tax issues on accounting. External actuaries calculate pension obligations and similar obligations. Regular training courses for those in charge of finance departments, which were offered online in the year under review, also ensure that all employees involved in the financial reporting process are up to date on the latest legislation and information of relevance to them.
The opportunity and risk management process is updated within the Würth Group on an ongoing basis and adapted to changes in the Group or in its economic and legal environment. In addition, at the request of the Advisory Board’s Audit Committee, an analysis of the risk management system was carried out by an auditing firm at the beginning of the 2021 fiscal year. The focus was on determining the status quo, analyzing the degree of maturity, and performing a comparison with third-party companies. In addition to the recommendations, which we will be investigating in close consultation with the Central Managing Board and the Audit Committee, the results of the analysis basically confirm the approach to risk management we have adopted to date. In the 2021 fiscal year, the establishment of the IT-based risk reporting system was continued at further Group companies and the Executive Board and heads of the Group’s administrative departments were actively involved in the risk management process.
Risks
The Central Managing Board identifies, analyzes, and assesses the Group’s risks at a dedicated annual workshop. This workshop determines focus risks that could pose a threat to the net assets, financial position, and results of operations of individual entities or the Würth Group as a whole in the short, medium, or long term. Furthermore, with the support of the risk manager, all major Group entities carried out a risk inventory and recorded and assessed focus risks and other risks in the reporting system. The processes already in place were enhanced in 2021, undergoing improvements and adjustments in line with changing internal and external requirements.
Major risks that can be insured on an economically reasonable scale are covered by Group insurance programs for all Group entities whenever possible. In the area of credit insurance, further local insurance policies taken out by individual Würth companies were incorporated into existing master agreements with various credit insurers. This allowed us to expand and standardize our insurance coverage and achieve economies of scale. In 2021, the credit insurance master policies were extended ahead of schedule until 1 January 2025, and the conditions were secured for a further three years. In addition, receivables from customers are monitored by an extensive receivable management system, also at the Group level. Individual financial service providers are associated with a heightened risk of default due to the nature of the business model. We counter this risk through a strict credit verification procedure and appropriate insurance for our investments. Collection days continued to decline at a low level in 2021 for the second year running. This highlights that our risk in this area is currently relatively low and that the existing processes and systems are effective. We believe that other risks in Germany lie in the applicable insolvency challenge rights, which grant insolvency administrators extensive opportunities for reimbursement if we have supported our customers with generous payment terms in the past. While this risk has been reduced in the short term by the temporary suspension of the obligation to file for insolvency due to the COVID-19 pandemic, we expect corporate insolvencies and, as a result, also insolvency appeals, to increase again in 2022. We have an insurance policy in place to cover such reimbursement claims so as to protect all German companies against unforeseeable risks in this area. Overall insurance coverage is managed centrally.
The Central Managing Board has identified potential risks that could have a negative impact on the net assets, financial position, and results of operations of the company in the following risk areas, sorted by descending order of relevance:
Economic environment
Through our global purchasing and sales activities, we have a high natural diversification of risk and, as a result, are less sensitive to negative economic developments in individual countries, even though more than 80 percent of our sales are generated in Europe. In addition, the diversification in our business units makes us independent of specific industries and markets, which was confirmed in particular during the various phases of the COVID-19 pandemic. Due to the large proportion of sales generated in Europe, we are heavily affected by economic fluctuations in the eurozone. The Würth Group sources around 25 percent of its goods from the Far East. The supply chain problems coupled with a drastic increase in container freight rates have had a significant impact on the business development of the Würth Group. Inventories were built up throughout the year to ensure our delivery capability.
In addition to the risks associated with the ongoing COVID-19 pandemic, we believe that risks lie in political developments in Eastern European markets and in Turkey, as well as in the trade barriers between China, the US, and Europe. We believe that—despite all of the associated economic and social challenges—immigration to Europe still presents opportunities for the labor market and on the demand side for our customers and, as a result, for the Würth Group. We are observing the rise of right-wing populism and the ongoing debate surrounding the proportionality of the measures to combat the COVID-19 pandemic with just as much concern as the development of risks on the procurement markets. We do not, however, currently see this as a direct threat to our business targets for 2022.
Most of the financial risks of the Würth Group are measured, monitored, and controlled centrally by Würth Finance International B.V. With liquid assets of EUR 1,217 million and a committed, unused credit line of EUR 400 million running until July 2023, the Würth Group has sufficient liquidity reserves to meet its payment obligations at all times. Thanks to its “A” rating from Standard & Poor’s, the Würth Group has very good access to the public and private capital markets to procure further financial resources. Any risks arising from derivative financial instruments are accounted for. At the time this management report was prepared, there was no indication of any specific counterparty risks, which are automatically monitored on a daily basis. A Credit Support Annex (CSA) is in place with the main counterparties to derivatives, thus further reducing counterparty risk. Cluster risks are avoided by means of internal deposit limits for individual banks. For a description of derivatives and associated risks, please refer to the notes on the consolidated financial statements under I. Other notes, [4] “Financial instruments.”
IT structures
As a company with a decentralized structure, the Würth Group had previously used various different IT systems, software components, platforms, and process control systems. This structure, which allows for a high degree of flexibility at the local level, increasingly emerged as a disadvantage in light of changing business models, digitalization, disruption, and the ever growing requirements as far as cyber security is concerned. In line with our corporate philosophy, which allows for a significantly higher degree of centralization in IT, the Würth Group’s IT organization, which is represented by the IT companies, has established a global ecosystem featuring platform-based IT solutions to suit the various business models within the Würth Group.
IT standardization
The central management of the IT companies with what is now a standardized product portfolio in the form of the IT ecosystem allows us to reflect the international multiplication strategy in our IT systems, too. Further standardization is achieved in line with a roll-out plan that sets out the launch dates at the individual companies, with numerous roll-out teams working on the introduction of the components in question in parallel to ensure a broad multiplication platform for the individual applications, processes, and functions.
The roll-outs will make existing processes more uniform, more efficient, more transparent, and faster. This will allow the individual companies to respond to the rising demand for individual ordering and delivery services among our customers, with the option of making the components available to other companies, too. Efficiency gains can still be achieved as the standardization of the IT structures through central development will result in economies of scale. Harmonization of the system environment and support by experts provide the IT ecosystem with significantly better protection against attacks.
The Würth Group’s IT service has proven its ability to perform in line with high standards. The uniform system platforms will allow further developments to be made available to all companies working on the platform in question within a very short period of time.
IT security
The number of cyber attacks has steadily increased worldwide in recent years. The Würth Group also saw an increase in attempted attacks in 2021. Risks arising from global integration are minimized by applying high security standards to make sure that the company has the best level of protection possible. Despite these efforts, cyber attacks have inflicted damage on a small financial scale at individual companies in the Würth Group. Thanks to our internal expertise in the area of incident response, we were able to quickly return the affected companies to full normal operations as soon as possible after the incidents concerned. The topic of IT security is a top priority within the Würth Group, right up to the top management level, and lessons learned from the incidents are incorporated directly into the security policies. IT system standards are reviewed by means of IT checks at the Group entities in accordance with a plan coordinated with the Group Auditing Department. This allows us to analyze and reduce the potential threat that cyber risks pose on a regular basis. We combat the resulting risks by taking organizational and technical measures and also by transferring risks that can be insured to external risk carriers, such as insurers. All measures relating to data security and IT risks are supported and implemented by our IT security officers in the national companies. They work in line with an IT Compliance Code of Conduct. The IT Compliance Officer of the Würth Group, together with his team and the IT security officers, ensures that the IT Compliance Code of Conduct is further developed and applied. The network of IT security officers in the companies is used to take measures to ward off security risks quickly at the level of the Group companies and implement those measures with regard to the continuous improvement of IT security. In companies where the IT systems have already been centralized, it is also possible to implement far-reaching and multi-level security procedures. At a physical level, these relate to our own data centers, and at the logistical level, they relate to various system and program components.
Raising employee awareness for information security risks is a top priority. Various media such as e-learning sessions, poster campaigns, information letters, and specialist presentations are used to show employees the behaviors and habits that reduce IT security risks. Targeted simulated attacks on individual companies and on particularly vulnerable functions are used, for example, in the form of phishing attacks, to test the success of the measures and adjust them if necessary.
Productivity
Every year, the Würth Group invests an amount running into the mid triple-digit million range to secure its planned sales growth and further expand its market shares in individual regions and market areas. As a result, any deviations from the planned route require a timely response, with targeted measures to counteract such developments. These measures include management using key productivity figures, the in-depth analysis of loss-making companies, a detailed, multi-stage investment controlling process, scenario calculations, and a firm focus on achieving the targeted operating results. As a general rule, we take care to ensure that sales and gross profit grow faster than personnel expenses, in line with one of the Würth Group’s fundamental principles: “Growth without profit is fatal.”
Human resources
Staff turnover, particularly among our sales force employees, remains a key focus. This is documented and analyzed across all hierarchy levels for every entity within the Würth Group. Regular employee surveys conducted by independent institutions and the monthly monitoring of staff turnover are key tools that allow us to identify unfavorable developments, analyze their impact on recruitment processes, customer loyalty, and training programs, and combat these effects using targeted measures. The overall staff turnover rate of the Würth Group remains at a very encouraging low level at below the 15-percent mark. We aim to ensure that this remains the case in the future. The COVID-19 pandemic has also changed the working world at Würth for good. Mobile working, in particular, has shown that employees do not have to be physically present in the office to work effectively. The “New Work” approach illustrates ways of structuring work in the Würth Group for the future, and how time at home and in the office can be combined effectively. As part of this development, the Würth employer brand is strengthened by the fact that our employees enjoy working together, regardless of where they work.
The lack of specialist employees to work as members of the in-house staff or the sales force is another challenge for HR management. For many companies, it is becoming increasingly difficult to find skilled trainees. This prompted us to further expand the activities of Würth Business Academy for the in-house staff and the sales force when it comes to training management employees and new management talent. Up-and-coming management talents partake in development courses to prepare them for various levels of management within the Würth Group via the Würth Potential, High Potential, and Top Potential training programs. These programs give employees targeted training that is tailored to suit their own individual ambitions and skills in order to prepare them for further management duties within the Group.
In order to ensure that the process involved in providing all central functions of the Würth Group with up-and-coming management talent is structured and targeted, two processes are in place at larger companies: The Management Assessment Process (MAP) is the qualitative tool used for the objective and standardized evaluation of executives. The talent management system is used to identify whether there is a sufficient number of qualified successors for functions that are relevant to the success of the Würth Group companies and, if not, by when these successors need to be available. Up-and-coming management talent is included in this system as well in order to ensure a structured and transparent development process. There is also a succession and contingency plan in place for managing directors, which ensures that succession arrangements that can be planned are made in good time.
In order to meet the increased requirements within HR, the Global HR Group function has been tasked with bundling and organizing the strategically relevant human resources issues at the Group level since January 2021. Within this context, the Würth Business Academy will now focus exclusively on the core topic of management development.
The international technical and management seminars will gradually be transferred to Akademie Würth, which will ensure that the necessary technical and management knowledge is available throughout the Würth Group in the future. The seminars include, for example, training measures in the areas of product management, purchasing, and logistics or financial topics. Since 2017, the Learning Campus has been a platform for digital learning on which all employees can complete e-learning courses. Together with the specialist departments, targeted activities are under way to digitize knowledge about global standards so as to make it available across the globe.
The third pillar of Global HR, HR Services and Processes, is currently in the process of being established. This includes the topic of global mobility in order to provide professional support to employees and managers on international assignments and also to support the optimal filling of key positions via this service function. A second area is addressing the establishment of a uniform IT infrastructure for the HR function that provides the Würth Group companies with the best possible support for their HR processes and makes state-of-the-art tools available to applicants, employees, and managers alike.
Würth Business Academy North America (in Chicago) was established back in October 2017 in order to provide the decentralized local companies with even better support with regard to HR development and talent management. Since January 2020, Würth Business Academy Asia-Pacific (in Shanghai) has been supporting talent development in the Asia-Pacific region.
Compliance risks
National and international transactions involving goods, services, payments, capital, technology, software, and other types of intellectual property are subject to numerous regulations and limitations that also have to be observed by the companies in the Würth Group. There is no question that we aim to comply with all statutory and official regulations for our business, both nationally and internationally. This applies when dealing with our customers and suppliers, employees, competitors, other business partners, and public authorities. Due to increasing legal complexity, we have in-house experts and consult renowned external consultants on a case-by-case basis. Particularly in China and emerging markets such as Brazil, complex, inconsistent, and constantly changing legal principles pose a challenge and also create risks that are difficult to assess and will persist in the long term due to the possibility of retroactive effects.
Value-oriented corporate culture
Mutual trust, predictability, honesty, and straightforwardness both internally and externally are fundamental principles that are deeply ingrained in Würth’s corporate culture. Our commitment to these values can be found as far back as the corporate philosophy penned by Prof. Dr. h. c. mult. Reinhold Würth back in the 1970s. This does not just entail adhering to all applicable laws and in-house regulations, but also means ensuring that employees maintain the proper mindset, which forms a key component of the sustainable corporate success of the Würth Group. Extensive internal guidelines known as the “PAP” (Policy and Procedure Manual) operationalize these fundamental principles in the form of descriptions of the structure and process organization, in addition to setting out specific rules and codes of conduct.
Compliance organization
With regard to the mounting requirements that compliance organizations have to meet at both the national and international level, the Central Managing Board made the decision in 2015, with the consent of the Advisory Board and the Supervisory Board of the Würth Group’s Family Trusts, to combine and restructure the existing components to form a Group-wide compliance management system and considerably strengthen the compliance organization. In addition to the role of Chief Compliance Officer and Group Compliance Officer, compliance officers were appointed at the level of the units and also within the largest individual companies in the Würth Group during the 2016 fiscal year. The responsibilities and structures for product, tax, and IT compliance that are already in place across the Group will remain in force, but the individuals responsible also report to the Chief Compliance Officer of the Würth Group. The Compliance Board provides advice on compliance incidents as and when required and makes recommendations regarding any measures that need to be taken. The Compliance Board is also responsible for the further development of the compliance organization and reports to the Central Managing Board and the Advisory Board of the Würth Group in all compliance matters. One particular focus was on further training for compliance officers at the company level.
Compliance regulations
The fundamental features of the corporate philosophy are summarized in a Code of Compliance and supplemented with regard to compliance with international standards. In order to anchor the compliance organization within the Group in the long term, Group-wide training sessions are conducted on the compliance organization and on compliance issues. Training sessions initially focus on “Dealing with gifts and invitations,” “Antitrust law and price fixing,” “Company secrets,” “Data protection,” “European General Data Protection Regulation,” and “Export control.” Due to increasing information security risks, further training measures were established in the 2021 fiscal year.
Group-wide reporting system
The Group-wide reporting system means that not only employees but also customers, suppliers, and other individuals will be able to report any suspected compliance breaches directly to the Würth Group’s Compliance Office. The use of a technical system made available by an external service provider means that reports can be submitted completely anonymously.
Prerequisite for sustainable corporate success
The compliance organization is supported by the firm conviction of the Central Managing Board, the Würth family, the Supervisory Board of the Würth Group’s Family Trusts, and the Advisory Board that a living and breathing compliance culture will play a key role in ensuring the further sustainable success of the Würth Group. At the same time, the management teams of the Group companies can proactively live up to their responsibilities with regard to the mounting national and international demands that compliance organizations have to meet.
Continuous further development of the compliance management system
In the 2020 fiscal year, in consultation with the Advisory Board of the Würth Group, we conducted a status quo assessment of our compliance management system together with an external consultant. As well as reviewing its fundamental orientation, we also wanted to receive impetus for further development and improvement. The results of this assessment have confirmed that we are pursuing the right focus with our compliance management system and form part of the continuous improvement process at the same time.
Business model
The business model of direct selling still offers considerable opportunities for the Würth Group in that it places us very close to the market and ensures customer loyalty. Nevertheless, customer ordering behavior has changed considerably in recent years. Digitalization offers a whole host of opportunities for working directly with suppliers. The relative ease with which businesses can establish Internet-based business models is resulting in growing competitive pressure. Our business model has to adapt to reflect this development. We want direct selling to continue to play a key role but also want issues such as logistics, services, and a broad product range to open up market opportunities. The sales representatives of today are no longer just salespeople, but rather manage the various customer contact points: the sales force, the pick-up shops, and the Internet. We refer to this as a multi-channel sales model in which e-business serves as a practical complement to the traditional sales methods in a manner that is tailored to suit our customers’ procurement organization. In 2021, the COVID-19 crisis and the resulting change in our customers’ purchasing behavior led to an above-average increase in e-business sales, as our systemic importance gave us the green light to deliver and our delivery capacity was virtually unrestricted. This development shows that we are on the right track with the services that we are offering with our customers’ needs in mind and that our strategy of multi-channel sales is bearing fruit.
Opportunities
The opportunities set out below could have a positive impact on our net assets, financial position, and results of operations. Like the risks, they are listed in decreasing order of relevance.
Decentralized structure
Würth’s decentralized structure is a great advantage for the Group, especially in light of the fact that the individual countries in which we operate display such variation in their economic development. We believe that this structure presents an opportunity for further sustainable growth. It allows for a quick local response to circumstances and changes in any given market environment, meaning that we can implement efficient measures. We will continue to push the development of the Würth Group while maintaining our decentralized structure. The term “decentralized” within this context not only refers to regional aspects, but also covers our large array of different business models. However, the fact that we pursue the principle of decentralization does not mean that we cannot standardize processes further where it makes sense to do so in order to make more efficient use of our resources.
Market penetration
Our share of the market is estimated at just five percent due to a low share of the market in most countries, with a few exceptions. What would appear to be a disadvantage actually signals major growth potential that we can tap into by further expanding our customer base and intensifying our customer relationships, for example, by continually enhancing intelligent distribution systems that offer real benefits to our customers.
Customer relations
Our more than four million customers form the basis for our business success. As a result, expanding and maintaining our customer relations are key components of our day-to-day work. We will continue to focus on comprehensive customer management at all Group companies. Around 300,000 customer contacts a day and a large number of long-standing relationships between our customers and our more than 33,000 sales representatives help us to exploit the existing potential to the greatest extent possible. Grouping our customers based on their individual needs is a key control mechanism for strategic management. Being close to our customers is our declared objective. The correlation between additional customers and sales growth, together with the service level, are important indicators of business success for us. Customer insolvencies are a manageable risk for the Würth Group. Due to our very extensive core range of over 125,000 products, the comparatively low average order values, and our broad customer base, we are well positioned to keep these risks at a minimum.
Quality
It is the express aim of the Würth Group to meet, or where possible exceed, the highest quality standards. For this reason, the guiding principle “Würth is quality—everywhere, every time” was anchored in the Würth Group’s quality management back in 2010 and consistently developed further in the years that followed. This brand promise applies to all our markets. Implementation of this principle opens up further key market opportunities for us both in the professional trades and with industrial customers. For us, ensuring reliable compliance with standards, in addition to fulfilling product requirements and approval criteria, is a fundamental quality management task to enable us to be a dependable partner for our customers. This is important, but we do not consider it enough in and of itself: We strive to surpass customer expectations wherever possible with our services and inspire our customers in the process.
In the 2021 fiscal year, the Würth Group’s central quality team (WQT) continued its activities. Despite ongoing restrictions due to the COVID-19 pandemic, training courses were held on management systems and product and process quality during the year under review and 233 participants received further training on a total of 435 training days.
Key components of the Würth quality promise include, first of all, the validation of new products by the quality department, for example, at Adolf Würth GmbH & Co. KG and Würth International AG, and, secondly, measures to safeguard the quality of delivery by conducting supplier training and systematic checks along the supply chain. As early as 2020, investments were made in training and systems to conduct remote audits, resulting in approximately 17 percent of supplier-related activities being conducted “remotely” by 2021. The Würth Group now has over 28 active “Supplier Quality Engineers” (SQEs) as well as its own test laboratories/goods checkpoints spread across Europe, Asia, and the US with a total of over 175 employees. By the end of the reporting period, seven test laboratories had been awarded ISO 17025 accreditation. Further investments were made in the expansion of the SAP-supported system WS1, to be used as a mandatory requirement throughout the Group, focusing on the advance quality planning function, the verification of tests, and measures aimed at the further integration of Group laboratories and suppliers.
Sustainability
As a family business, Würth is aware of its social responsibility and is focused on sustainable growth in the long term. As part of our sustainability management system, we have started to supplement our existing management processes to include components that provide us with valuable data on products and processes at each individual company and form the basis for Group-wide sustainability management. These components include the global sustainability indicators developed by the Global Reporting Initiative (GRI), the reporting of greenhouse gas emissions, and the strategic focus centering on the 17 United Nations Sustainable Development Goals (SDGs). Sustainability reporting helps us to make the inclusion of environmental and social aspects transparent and to incorporate them as an even more firmly established component of our management decisions. The data for sustainability reporting is recorded and collected using Würth’s internal reporting tool, CIS. It forms the basis for making sustainability measurable within the Würth Group. At the same time, the idea is to identify forward-looking approaches and solutions and communicate them to the participating companies. In this respect, sustainability reporting provides a Group-wide empirical basis of reliable facts and figures, as well as best-practice examples, that will be incorporated into the Würth Group’s first-ever sustainability report in 2022.
Diversity
Different opinions and outlooks boost creativity and innovation, while paving the way for new solutions. In order to make the best possible use of the considerable potential that diversity offers within the Würth Group, the aim is not only to build diverse teams, but also to involve and listen to all employees. This is why the Würth Group provides a working environment and overall conditions that are free of prejudice and intolerance and enable each and every individual to make a valuable contribution. Consequently, we adopt a strict zero-tolerance approach to all forms of discrimination based on gender, gender identity, sexual identity, physical or mental impairment, social or ethnic origin, age, nationality, language, skin color, and religion. As an initial step on the way to greater diversity within the company, the focus is on a higher proportion of women at all hierarchical levels, especially in management positions. Initial measures have already been introduced in the form of a mentoring program, but also through networks for women in the Group. At the same time, the development and expansion of diversity expertise among employees and management will help drive this development further.
Overall assessment
The opportunities available will generally enable us to achieve further profitable growth in 2022 and beyond. The risks for the Würth Group are limited by the established and functioning risk management system, even in the ongoing COVID-19 pandemic, and are monitored very closely. Existing risks are consistently monitored and assigned measures to ensure that they do not jeopardize the Würth Group’s continued prosperity.
We are very concerned as we follow the current developments in the Ukraine conflict and the associated impact on the population. The direct and indirect economic implications and risks for the Würth Group are difficult to forecast at the present time.
- Number of employees rises to 83,183
- Broad-based in-house employee development program
Workforce development
The number of employees in the Würth Group rose by 5.1 percent to 83,183 as of 31 December 2021 (2020: 79,139). In Germany, the Würth Group had 25,438 employees on its payroll (2020: 24,514), while Würth companies abroad reported 57,745 employees (2020: 54,625). There were 33,536 employees working as permanent sales representatives worldwide in the 2021 fiscal year (2020: 33,176).
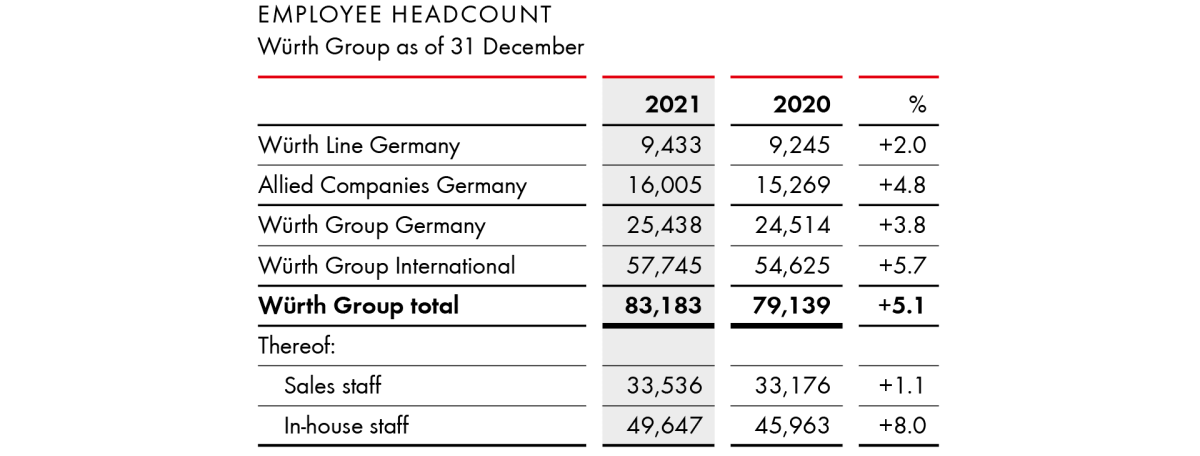
HR strategy
The shortage of specialists and managers is having an impact in many countries and qualified employees are increasingly becoming a limiting factor for growth. It is therefore important to retain employees at the company and to offer a positive working environment with interesting development opportunities. The Würth Group, with its diverse business models and international orientation, has many possibilities in this respect.
In order to meet the increased requirements within HR, the Global HR Group function has been tasked with bundling and organizing the strategically relevant HR issues at the Group level since January 2021. One area of these activities relates to Würth Business Academy (WBA), which focuses on management development and talent management. Akademie Würth, as the second pillar of the global HR function, is being further expanded to become a global provider of training and consultancy services for companies in the Würth Group and their customers. The third area, HR services and processes, ensures, for example, that a state-of-the-art IT infrastructure is available for HR processes, while an attractive Global Mobility Policy ensures that key functions can be filled internationally.
WBA ensures holistic management training and the systematic development of up-and-coming talent. The aim is for management positions to be filled primarily from the company’s own ranks. WBA supports this process by offering suitable training programs for different stages in an employee’s development. It also supports management teams worldwide in succession planning as part of a structured process and makes its information available to the Central Managing Board and the executive bodies of the Würth Group as part of the risk assessment process. This information is condensed and analyzed with the top management team of the Würth Group at regular intervals, with agreements being made on the measures to be taken and talent pools being defined.
The location for training, HR, and talent development activities in North America has also brought us closer to our target groups there, thus encouraging the internationalization of our operations with regard to HR. Since January 2020, an additional HR development site has been up and running in China for the entire Asia-Pacific region. This decentralized approach allows the programs to be adapted to better suit regional requirements and allows for talent management on location to be focused and managed based on the specific needs.
Digitalization will lead to major changes and associated challenges with regard to human resources. The newly established HR Services and Processes function works together with the companies in the Würth Group and the IT department to develop an appropriate strategy and provide the companies with suitable software solutions. In the area of digital learning, the Learning Campus is a platform that has been open to all employees of the Würth Group since 2017.
Under the leadership of the Global HR function, international cooperation within the Group is being strengthened by an HR network and a platform for sharing best practices. In order to develop and establish HR-related and strategically important topics, an HR Board has been set up comprising HR managers with operational responsibility.
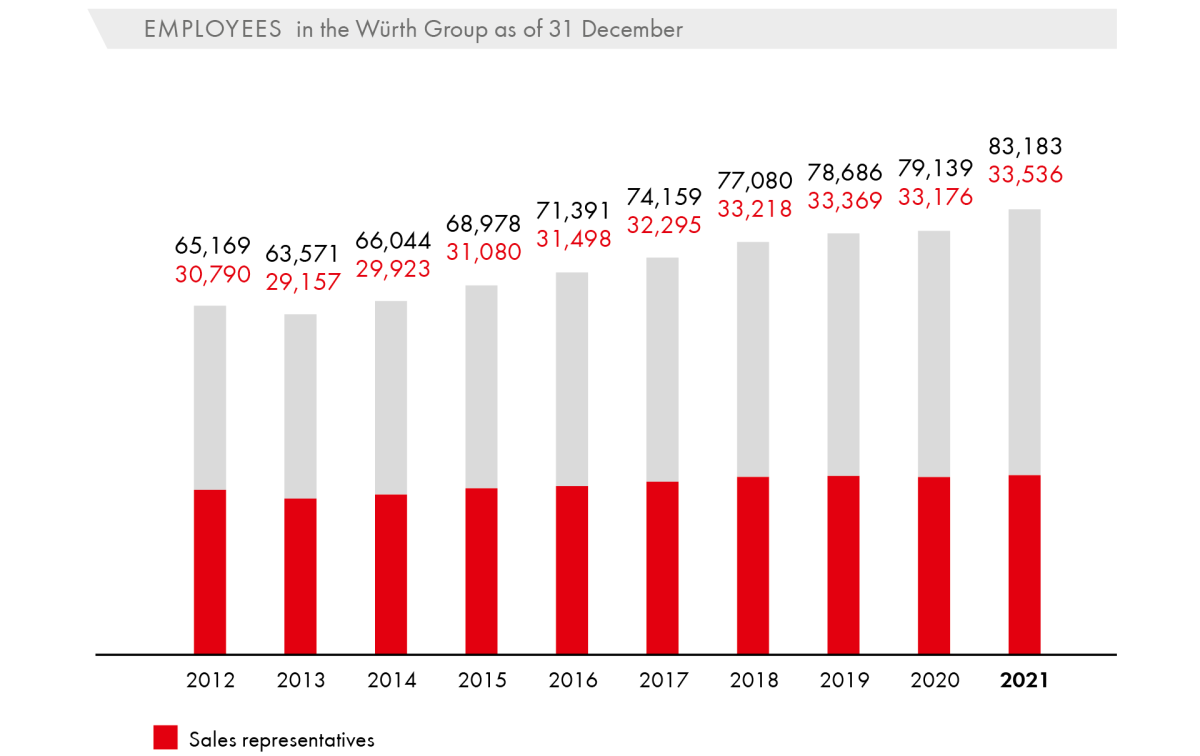
Employee training
The skills, competences, and qualifications of all employees, together with their motivation and enthusiasm, form the basis for a successful future. For this reason, personal development and further professional qualification are of particular relevance in order to meet the demands of the market. There are various phases in each employee’s working life: There are times at which personal issues such as self-worth or self-confidence play a key role and there are also times in which focus is placed on career advancement—be it in an employee’s career as a manager or in the various specialist departments. The programs available at Würth aim to offer each and every employee training that suits their individual skills and professional objectives.
As a family business, Würth is committed to long-term corporate development. This also applies when it comes to promoting the talents of the future. In Germany, where there is a long tradition of dual training concepts, Würth has been committed to providing people with extensive initial training for more than 60 years now. At the end of 2021, the Würth Group in Germany had 1,312 trainees for around 50 different occupations. Young professionals can also study for bachelor’s degrees at the Baden-Württemberg Cooperative State University. The main focus in the German companies is on commercial, technical, and catering apprenticeships.
Akademie Würth offers a holistic further training concept for employees of the Würth Group, as well as for customers and interested parties outside the Würth Group. Akademie Würth offers a practice-oriented range of further training courses specifically for craft businesses in the form of technically oriented training courses. The targeted courses focus on specific topics such as fire safety, metalworking, fasteners, sealants and adhesives, motor vehicles, and occupational safety. This allows Würth to support its customers as a service provider, driver of innovation, and mentor as well. The concept is rounded off by consultancy services on all matters relating to quality and process management, organizational development, and business excellence. This gives the Würth Group a unique opportunity in the market to actively support its customers’ current and future success, thus allowing it to secure sustainable business relationships. Based on an independent representative customer survey, this approach was awarded the “TOP CONSULTANT” award in 2021.
Companies within the Würth Group are given support to help them meet the requirements that apply to them. This includes the implementation of overall statutory conditions, such as the creation and implementation of integrated management systems, or support with certification processes, as well as compliance with specific customer requirements. With its range of courses, Akademie Würth allows employees and managers to engage in lifelong learning in order to successfully achieve the goals they have set for themselves, both now and in the future. All employees have the opportunity to acquire the relevant knowledge on the basis of the Würth Group’s culture and strategy at any time. The focus is on putting theory into practice. In addition, Akademie Würth helps the specialist departments to multiply relevant knowledge in the Group in order to successfully face current and future challenges. Akademie Würth also provides companies with support in areas such as strategy development and the implementation of change processes. Lean Management and Six Sigma have already been launched successfully at companies in various sectors. In order to ensure sustainability, the approach chosen tends to involve providing support with projects that will have an impact on the organization’s profit or loss.
Degree programs for working professionals at Akademie Würth Business School, which are open both to employees of the Group and to interested individuals from outside the Group, allow people to study for academic degrees. The Bachelor of Business Administration in cooperation with Hamburger Fern-Hochschule university is a seven-semester program leading to a Bachelor of Arts (B.A.) degree. The bachelor’s program in Industrial Engineering and Technical Sales in cooperation with SRH Distance-Learning University of Applied Sciences takes six semesters, finishing with a Bachelor of Science (B.Sc.). In collaboration with the University of Louisville in Kentucky (USA), Würth also offers an internationally recognized master’s degree in Global Business. This one-year program, which is conducted in English, awards graduates a Master of Business Administration (MBA). As of this year, a Master of Science with a focus on Family Business can be obtained after completing the MBA course. The courses last six months and are offered in cooperation with Heilbronn University of Applied Sciences. The master’s program in Digital Management & Transformation confers a Master of Science (M.Sc.) in four semesters, also in cooperation with SRH Distance Learning University. Würth also offers a Doctor of Business Administration (DBA) as a three-year program in conjunction with Northumbria University, Newcastle. The DBA is a professional doctorate in business administration, equivalent to a PhD but with a clear focus on developing and improving professional practice.
Health management
In these times dominated by the COVID-19 pandemic, the in-house health management program “Fit mit Würth” continued to raise awareness among the employees of Adolf Würth GmbH & Co. KG and a large number of other companies in the German Würth Group of healthy living and working and the creation of an overall environment that is conducive to employee health. This was achieved primarily with the help of new digital options: Online health courses, active breaks, and lectures helped employees and their families to stay healthy. The main beneficiaries of these digital offerings were employees working from home, members of the sales force, and pick-up shop employees. A holistic approach to health management is crucial, spanning areas such as exercise, nutrition, physical regeneration, safety, social affairs, and prevention. “Fit mit Würth” takes part in a regular audit to obtain the Corporate Health Award. A large number of subsidiaries are now also developing health programs of their own.
Employee survey
Employee satisfaction has always been a top priority for the Würth Group. A standardized and uniform employee survey has been carried out since 2005 in order to obtain regular information on how satisfied employees are with the Würth Group company they work for and how these satisfaction levels are developing. The results also provide structured information on the soft factors of corporate and leadership culture. The focus is on boosting employee satisfaction with the aim of improving company performance. The survey provides a benchmark both within and between individual companies in the Würth Group. Brief “pulse check” surveys on current topics are now also being used alongside the standardized regular survey. The surveys are carried out together with the Mannheim-based WO Institute (Institute for Economic and Organizational Psychology).
Thanks to our employees
The Central Managing Board of the Würth Group would like to thank all employees and employee representatives for the considerable commitment they have shown. In the second year dominated by the pandemic, all employees yet again showed a particularly high degree of flexibility and a willingness to pursue new avenues together. We are as grateful for this as we are for the trust they have placed in the company and their loyalty to their employer.
Macroeconomic environment
The full impact of the war in Ukraine remains to be seen. The impact on the global economic situation is as uncertain as the question of how the situation will continue to unfold. Experts are becoming increasingly pessimistic as the war will fundamentally change the overall geopolitical and economic environment, especially for Europe. In the short term, it will trigger a significant slowdown in economic activity, partly due to the exacerbation of supply chain issues, further increases in raw material, energy and food prices, and financial market reactions to the sanctions. In the medium and long term, the breaking of some of the links between the economic areas and the resulting need for diversification will slow economic development down even further. What this will mean in detail for individual economies, for example, whether they will be able to compensate for their reliance on gas, oil, and coal from Russia in particular, is difficult to predict at present.
One thing that is certain, however, is that the ongoing impacts of the COVID-19 pandemic on the markets, the supply chain issues, and the further increase in energy and raw material prices represent a precarious starting position. Coupled with the consequences of the war in Ukraine, these factors make the prospect of a stagflationary recession increasingly likely.
Across the eurozone, hefty price increases are likely to coincide with a lack of economic growth, which could prompt the European Central Bank to rethink its monetary policy.
As far as Germany is concerned, Deutsche Bundesbank expects to see an inflation rate of 5.0 percent on average for 2022 (2021: 3.2 percent), and high levels of inflation are also expected throughout the eurozone. Scenarios of a recession in Western Europe—at least for a short period—can no longer be ruled out.
Whereas economists and experts were still cautiously optimistic at the beginning of the year, especially as individual economies were increasingly relaxing their stringent restrictions imposed in response to the COVID-19 pandemic and had unveiled plans to reopen, any easing of the economic situation now ultimately seems to be a distant prospect. The economic forecasts for Germany vary accordingly. One thing they all have in common is that as of 24 February 2022, the institutions started making downward revisions to their previous forecasts: The Hamburg Institute of International Economics (HWWI), for example, revised its forecast of +3.5 percent for the German economy at the beginning of the year to +2.0 percent, meaning that it expects economic output to grow at a slower pace than in the previous year (2021: +2.7 percent). The Scope rating agency also lowered its economic forecast from +4.4 percent for the current year to +3.5 percent. The picture for Europe as a whole is similarly subdued. The European Commission now expects growth to slow to below the 4.0 percent originally forecast (2021: +5.2 percent).
It is also difficult to predict how the individual sectors will develop over the course of the year. The Association of German Chambers of Commerce and Industry (DIHK) no longer considers its forecast export growth of 6.0 percent to be achievable—despite order books being full to the brim. Further disruptions to global supply chains due to the sanctions are also within the realms of possibility. This is already hitting the automotive industry very hard: Due to a shortage of wire harnesses, a large proportion of which are supplied from Ukraine, almost all major car makers brought production at their German sites to a halt at the beginning of March. Construction and industry are currently benefiting from substantial order backlogs, which could stimulate production in these sectors. Here, too, however the catch-up process is likely to be less dynamic than previously expected.
All in all, it is currently difficult to arrive at any reliable forecasts in the mixed global political and macroeconomic situation. The duration and severity of the war will be decisive for further developments. So too will the question as to how the economies outside NATO, and China in particular, will position themselves.
Development of the Würth Group
- Economic impact of the Ukraine conflict difficult to estimate
- Multi-channel strategy as a success factor during the pandemic
- Adolf Würth GmbH & Co. KG invests in Künzelsau-Gaisbach location
With sales of EUR 17.1 billion and an operating result of EUR 1,270 million, the Würth Group set new records in the 2021 fiscal year. Group sales in Germany grew by 14.3 percent to EUR 6.9 billion (2020: EUR 6.1 billion). With EUR 10.1 billion (2020: EUR 8.3 billion), the Würth companies abroad achieved even more successful results.
This positive development is based on the strategy of further digitalization in conjunction with multi-channel sales. Particularly during the pandemic, where contactless purchases and compliance with hygiene regulations is essential, Würth has the right solutions at its fingertips. Key components include the online shop, the Würth App, and the entire e-procurement area, supplemented by the dense network of pick-up shops for bricks-and-mortar purchases. The world’s 2,000th Würth Line pick-up shop opened in Norway in December 2021. Together with the pick-up shops of the Allied Companies, the Würth Group has 2,497 pick-up shops. The e-business sales area was expanded further in 2021 and became increasingly relevant in strategic terms: Sales in this area grew by 23 percent in a year-on-year comparison.
The Würth Group relies on its own digital solutions for the online shop, e-procurement, and the app. This allows it to create a shared uniform technical foundation that enables not only innovative further developments, but also their rapid, cost-effective roll-out. These central solutions are now used at around 60 companies within the Würth Group. Today, e-business accounts for around 20 percent of total sales. More than 1,000 employees across the globe work in the e-business environment.
E-procurement has continued to become more important within the Würth Line. More and more customers are professionalizing and digitalizing their procurement, which is also reflected in the 38 percent growth compared to 2020. In many countries, specialists are deployed to help defined key accounts optimize and automate their purchasing processes.
Within the Würth Line, regional competence centers are being set up in Southeast Asia and Latin America in order to drive forward e-business activities in those markets and to support the local companies with individually customized expertise.
Würth is making extensive use of the opportunities offered by digitalization during the COVID-19 pandemic. Since the beginning of the pandemic, a large part of the workforce has been working from home where it makes sense to do so. Nevertheless, personal contact forms the basis of our corporate culture and is something we want to spend more time cultivating after the pandemic.
In addition to personal contact, Würth’s corporate culture is characterized by values such as diversity and tolerance. The Group has been devoting increased attention to the issue of diversity since 2021, and it will be one of the focal areas for 2022. As a first step, Würth Business Academy has launched a mentoring program to support female high-potentials. The aim is to provide additional support for female talent, make them more visible to top management, and raise awareness of factors that can facilitate women’s career paths. The topic of diversity is also being given greater consideration in our recruitment processes.
Another focal topic for 2022 is sustainability: Würth has set itself the goal of striking an even better balance between environmental, economic, and social issues in the future. Adolf Würth GmbH & Co. KG, for example, as the largest individual company in the Group, has set itself the objective of achieving climate-neutral status (Scope 1 and 2) at all its locations throughout Germany by 2024. It has defined far-reaching measures for implementation at its headquarters in Künzelsau-Gaisbach and all of its pick-up shops in Germany: switching to electromobility, increasing energy efficiency by implementing an energy management system, expanding the supply of electricity generated in-house, purchasing green electricity, offsetting any carbon emissions that cannot be avoided. In addition to Adolf Würth GmbH & Co. KG, numerous other companies are also implementing sustainability projects. The North American Würth Additive Group Inc., for example, is currently developing filaments, plastic threads for 3D printing, from recycled carbon fibers. The aim of the pilot project is to develop processes and structures for the recycling and use of used carbon fibers and ultimately to serve as a role model for a successful circular economy model in the field of 3D printing. The Würth Group will publish its first sustainability report in 2022.
To strengthen the future of the Würth brand in the long term, Adolf Würth GmbH & Co. KG is investing in the Künzelsau-Gaisbach site. With an investment volume of EUR 70 million, the nucleus of the Group will complete an innovation center in the third quarter of 2022 where state-of-the-art workshops, testing facilities for screw and anchor technology, mechatronics, and chemical-technical products will drive application- and customer-oriented product development. In addition, the company is planning a new administration building with around 375 workstations. The focus is on sustainable construction that meets the requirements of a sustainable circular economy: The 49-meter high-rise building will be based on a hybrid timber construction. The construction is scheduled to begin in 2024.
Overall statement on the future development of the Würth Group
Due to the current economic and global political situation, it is difficult to arrive at any reliable forecast regarding the further development of the Würth Group in 2022. The direct effects of the Ukraine crisis on the Würth Group’s sales are not material at present; the indirect effects are impossible to quantify.
We are now entering the third year of the COVID-19 pandemic. The critical factor in ending this crisis remains a high vaccination rate. This is the only way to achieve herd immunity. Numerous vaccines were developed and approved within a very short period of time from 2020 onward. To ensure that everyone, including people living in the world’s poorest countries, has access to vaccination, the World Health Organization (WHO) joined forces with other global stakeholders to launch the COVAX initiative. Adolf Würth GmbH & Co. KG supported this initiative by donating EUR 500,000 in March 2021. The milder Omicron variant of coronavirus offers hope that, together, we can come to grips with the pandemic.
The ongoing supply bottlenecks, material shortages, and dramatic price increases will doubtlessly continue to affect our business in the near future. In addition, the European Commission imposed anti-dumping duties ranging from 22.1 percent to 86.5 percent on steel fasteners originating in China, effective 18 February 2022. This will cause additional upheaval on the procurement markets and further increase the pressure on purchase prices. Our own production plants in Germany and Europe, however, ensure a certain independence from global supply chains. The Group company SWG Schraubenwerk Gaisbach GmbH in Waldenburg, for example, produces the ASSY® screw for timber construction.
We are watching the situation in Ukraine with great concern. Current developments will force us to build up increasing safety stocks, which is likely to result in an increasing volume of financial resources being tied up and in the Würth Group’s net debt increasing too. The top priority in this complex situation, however, is the safety of our employees in Ukraine. They are receiving financial support so that they can get themselves and their families to safety. We are also providing financial support for our employees in Russia and Belarus.
Provided that the military conflict remains confined to the territory of Ukraine and does not escalate further, we expect sales growth in the high single-digit percentage range and slight earnings growth in 2022.